Heat treatment processes for steel are essential for altering its mechanical properties, such as hardness, ductility, toughness, and strength, to meet specific application requirements. The most common heat treatment methods include annealing, quenching, tempering, normalizing, case hardening, and carburizing. Each process involves controlled heating and cooling cycles to achieve desired structural changes in the steel. For instance, annealing softens the metal for improved machinability, while quenching increases hardness by rapid cooling. Tempering reduces brittleness after quenching, and case hardening enhances surface hardness while maintaining a tough core. These processes are critical in industries like automotive, aerospace, and manufacturing, where material performance is paramount.
Key Points Explained:
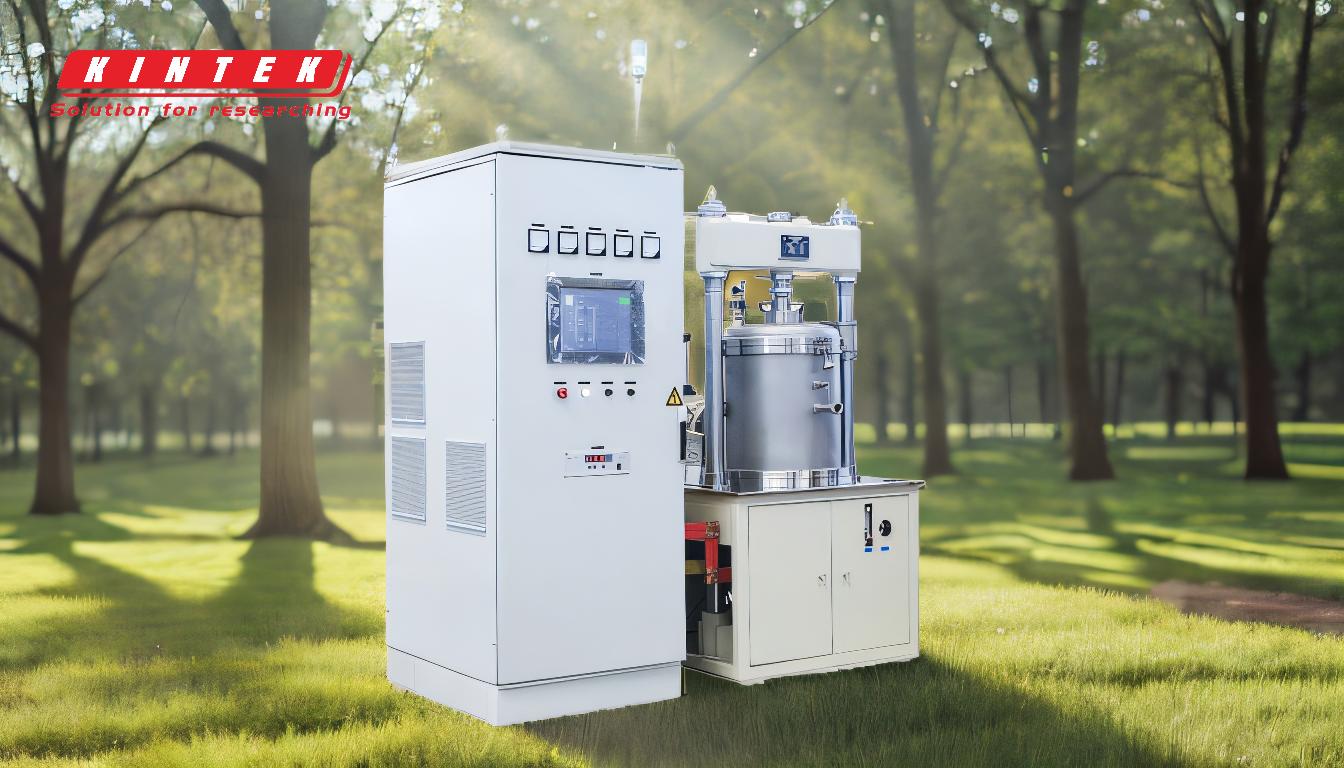
-
Annealing
- Purpose: Softens steel to improve machinability, ductility, and reduce internal stresses.
- Process: The steel is heated to a specific temperature (above its critical point), held for a period, and then slowly cooled in a furnace.
- Applications: Used for materials that need to be worked on further, such as machining or forming.
-
Quenching
- Purpose: Increases hardness and strength by rapidly cooling the steel.
- Process: The steel is heated to a high temperature and then rapidly cooled in water, oil, or air.
- Applications: Ideal for components requiring high wear resistance, such as gears and cutting tools.
-
Tempering
- Purpose: Reduces brittleness and improves toughness after quenching.
- Process: The quenched steel is reheated to a temperature below its critical point and then cooled.
- Applications: Used for tools and structural components that require a balance of hardness and toughness.
-
Normalizing
- Purpose: Refines the grain structure and improves mechanical properties.
- Process: The steel is heated above its critical temperature and then air-cooled.
- Applications: Suitable for preparing steel for further processing or improving its mechanical properties.
-
Case Hardening
- Purpose: Increases surface hardness while maintaining a tough core.
- Process: The steel is heated in a carbon-rich environment, allowing carbon to diffuse into the surface layer.
- Applications: Commonly used for gears, bearings, and other components requiring high surface wear resistance.
-
Carburizing
- Purpose: Adds carbon to the surface of low-carbon steel to increase hardness.
- Process: The steel is heated in a carbon-rich atmosphere, allowing carbon atoms to penetrate the surface.
- Applications: Used for parts like camshafts and crankshafts that need a hard surface and a tough core.
-
Precipitation Strengthening
- Purpose: Enhances strength by forming fine particles within the steel matrix.
- Process: The steel is heated to dissolve alloying elements, then cooled and aged to allow precipitation.
- Applications: Common in high-strength alloys used in aerospace and automotive industries.
-
Martensitic Transformation
- Purpose: Achieves high hardness and strength through a phase transformation.
- Process: The steel is rapidly cooled to form martensite, a hard and brittle phase.
- Applications: Used for cutting tools, knives, and components requiring extreme hardness.
-
Stress Relieving
- Purpose: Reduces internal stresses caused by machining, welding, or cold working.
- Process: The steel is heated to a temperature below its critical point and then slowly cooled.
- Applications: Used to prevent distortion or cracking in machined or welded parts.
-
Bright Annealing
- Purpose: Minimizes oxidation and maintains a clean surface finish.
- Process: The steel is annealed in a protective atmosphere (e.g., hydrogen, nitrogen, or argon).
- Applications: Suitable for stainless steel and other materials requiring a bright, oxide-free surface.
By understanding these heat treatment processes, manufacturers can select the appropriate method to achieve the desired properties for specific applications, ensuring optimal performance and longevity of steel components.
Summary Table:
Process | Purpose | Applications |
---|---|---|
Annealing | Softens steel, improves machinability, and reduces internal stresses. | Materials requiring further machining or forming. |
Quenching | Increases hardness and strength by rapid cooling. | Gears, cutting tools, and high-wear components. |
Tempering | Reduces brittleness and improves toughness after quenching. | Tools and structural components needing hardness-toughness balance. |
Normalizing | Refines grain structure and improves mechanical properties. | Preparing steel for further processing or enhancing properties. |
Case Hardening | Increases surface hardness while maintaining a tough core. | Gears, bearings, and components requiring high surface wear resistance. |
Carburizing | Adds carbon to low-carbon steel surfaces to increase hardness. | Camshafts, crankshafts, and parts needing hard surfaces with tough cores. |
Precipitation Strengthening | Enhances strength by forming fine particles in the steel matrix. | High-strength alloys in aerospace and automotive industries. |
Martensitic Transformation | Achieves high hardness and strength through phase transformation. | Cutting tools, knives, and components requiring extreme hardness. |
Stress Relieving | Reduces internal stresses from machining, welding, or cold working. | Preventing distortion or cracking in machined or welded parts. |
Bright Annealing | Minimizes oxidation and maintains a clean surface finish. | Stainless steel and materials needing bright, oxide-free surfaces. |
Optimize your steel components with the right heat treatment—contact our experts today!