Induction furnaces are primarily categorized into two main types: coreless and channel-type. Coreless induction furnaces use a water-cooled solenoid coil to generate an alternating magnetic field, which induces eddy currents in the metal, causing it to melt. Channel-type induction furnaces, on the other hand, rely on a loop of molten metal acting as a single-turn secondary winding around an iron core. Both types are widely used for melting and alloying metals with minimal melt losses, though they offer limited refining capabilities. Additionally, induction furnaces can vary in size, capacity, frequency, and design, making them suitable for different industrial applications.
Key Points Explained:
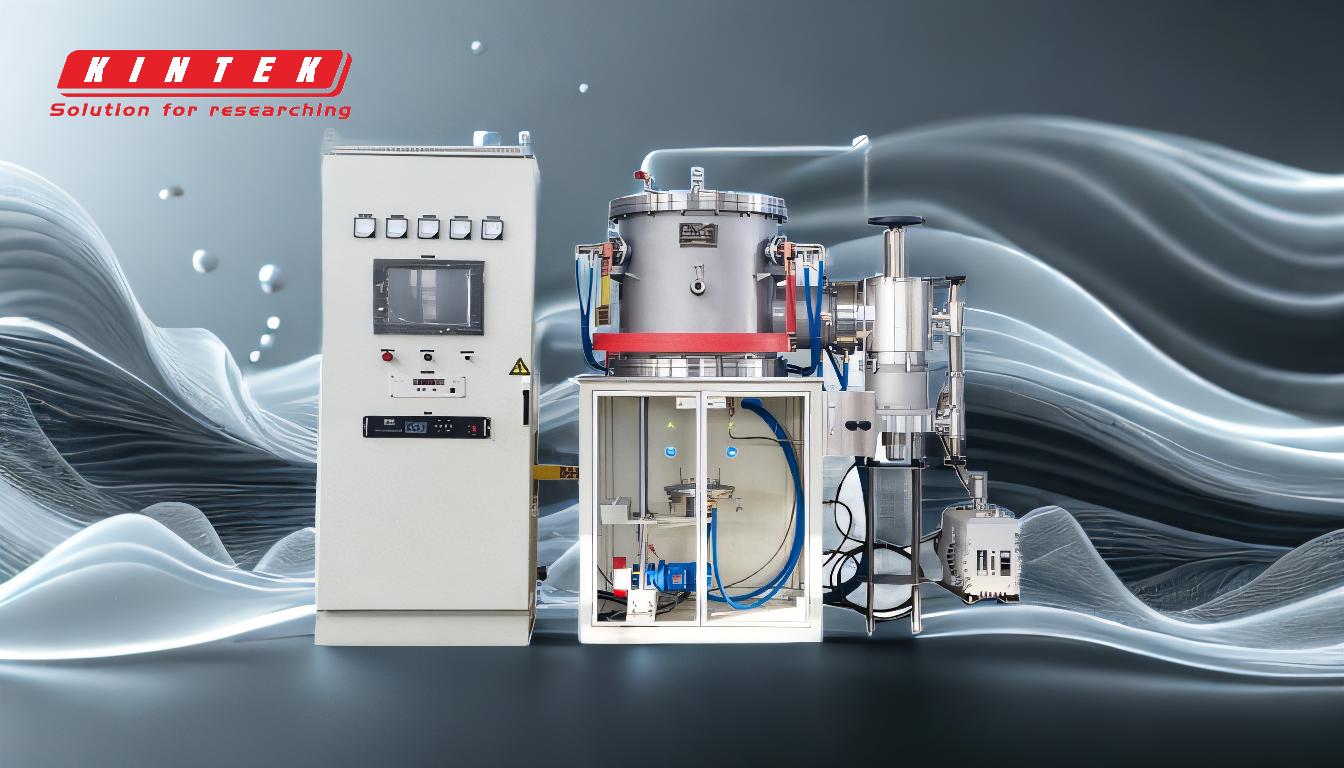
-
Coreless Induction Furnaces:
- Design: Coreless induction furnaces consist of a crucible surrounded by a water-cooled alternating current solenoid coil. The metal to be melted is placed inside the crucible.
- Working Principle: The alternating current in the coil generates a magnetic field, which induces eddy currents in the metal. These currents generate heat, melting the metal.
- Applications: Ideal for melting and alloying a wide variety of metals, including steel, iron, copper, and aluminum.
-
Advantages:
- High efficiency and fast melting rates.
- Minimal melt losses and contamination.
- Flexibility in handling different metals and alloys.
-
Disadvantages:
- Limited refining capabilities.
- Requires a crucible, which may need periodic replacement.
-
Channel-Type Induction Furnaces:
- Design: Channel-type induction furnaces feature a loop of molten metal that acts as a single-turn secondary winding around an iron core.
- Working Principle: The primary coil generates a magnetic field, inducing a current in the molten metal loop, which heats and maintains the metal in a molten state.
- Applications: Commonly used for holding and superheating molten metals, particularly in foundries and metal casting operations.
-
Advantages:
- High thermal efficiency and energy savings.
- Suitable for continuous operation and long holding times.
- Low maintenance and long service life.
-
Disadvantages:
- Limited to specific types of metals and alloys.
- Requires a pre-melted charge to initiate the loop.
-
Variations in Size, Capacity, and Frequency:
- Size and Capacity: Induction furnaces can range from small laboratory units to large industrial furnaces capable of handling several tons of metal.
- Frequency: The operating frequency of induction furnaces can vary, with higher frequencies typically used for smaller furnaces and lower frequencies for larger ones. This affects the depth of penetration of the induced currents and the heating efficiency.
-
Comparison with Other Furnace Types:
- Natural Gas, Oil, and Propane Furnaces: These furnaces rely on combustion for heating and are typically used for space heating rather than metal melting.
- Electric Furnaces: While electric furnaces can also be used for metal melting, induction furnaces offer faster heating and better control over the melting process.
-
Industrial Applications:
- Foundries: Induction furnaces are widely used in foundries for melting and casting metals.
- Metal Alloying: They are ideal for creating specific metal alloys with precise compositions.
- Recycling: Induction furnaces are often used in metal recycling operations due to their efficiency and minimal melt losses.
-
Considerations for Purchasers:
- Energy Efficiency: Induction furnaces are generally more energy-efficient compared to traditional furnaces.
- Operational Costs: While the initial investment may be higher, the operational costs, including maintenance and energy consumption, are often lower.
- Flexibility: The ability to handle different metals and alloys makes induction furnaces versatile for various industrial applications.
In summary, coreless and channel-type induction furnaces are the two main types, each with distinct designs and applications. Coreless furnaces are versatile and efficient for melting a wide range of metals, while channel-type furnaces are ideal for holding and superheating molten metals. Both types offer significant advantages in terms of energy efficiency and minimal melt losses, making them essential tools in modern metallurgy and metal processing industries.
Summary Table:
Feature | Coreless Induction Furnace | Channel-Type Induction Furnace |
---|---|---|
Design | Crucible with water-cooled solenoid coil | Molten metal loop around an iron core |
Working Principle | Magnetic field induces eddy currents in metal | Magnetic field induces current in molten loop |
Applications | Melting and alloying various metals | Holding and superheating molten metals |
Advantages | High efficiency, minimal contamination | High thermal efficiency, low maintenance |
Disadvantages | Limited refining, crucible replacement | Limited metal types, pre-melted charge |
Industrial Uses | Foundries, metal alloying, recycling | Foundries, metal casting |
Looking for the right induction furnace for your needs? Contact our experts today for personalized advice!