Melting processes are essential in various industries, particularly in metallurgy and materials science, to transform solid materials into liquid form for further processing. The primary types of melting processes include smelting, induction melting, suspension melting, and arc melting. Each method has distinct mechanisms, applications, and advantages depending on the material being processed and the desired outcome. Smelting is commonly used for extracting metals from ores, while induction melting is favored for its precision and efficiency in melting metals. Suspension melting is a specialized technique often used in high-temperature applications, and arc melting is ideal for producing high-purity metals and alloys. Understanding these processes helps in selecting the appropriate method for specific industrial needs.
Key Points Explained:
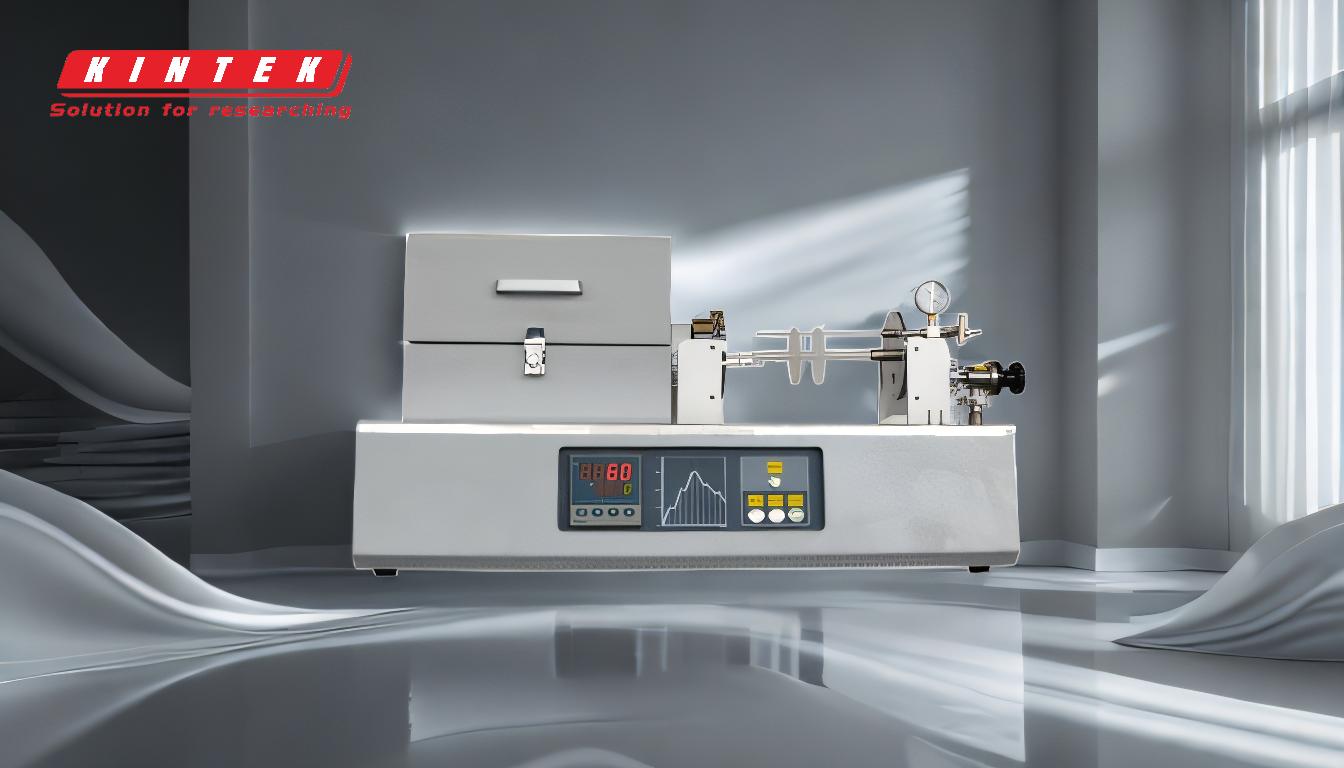
-
Smelting
- Definition: Smelting is a process used to extract metals from their ores by heating the ore beyond its melting point, often in the presence of a reducing agent like coke or charcoal.
- Applications: Primarily used in the extraction of metals such as iron, copper, and lead from their respective ores.
- Mechanism: The process involves chemical reactions that separate the metal from impurities, resulting in a molten metal and slag (waste material).
-
Advantages:
- Efficient for large-scale metal extraction.
- Can process low-grade ores.
-
Limitations:
- High energy consumption.
- Generates significant waste (slag) and emissions.
-
Induction Melting
- Definition: Induction melting uses electromagnetic induction to generate heat within a conductive material, causing it to melt.
- Applications: Widely used in foundries for melting metals like steel, aluminum, and copper.
- Mechanism: An alternating current passes through a coil, creating a magnetic field that induces eddy currents in the metal, generating heat.
-
Advantages:
- Precise temperature control.
- Clean and efficient process with minimal contamination.
- Suitable for small to medium-scale operations.
-
Limitations:
- High initial equipment cost.
- Limited to conductive materials.
-
Suspension Melting
- Definition: Suspension melting involves suspending particles in a high-temperature environment, such as a plasma or flame, to achieve melting.
- Applications: Used in advanced materials processing, such as the production of fine powders or high-purity materials.
- Mechanism: Particles are suspended in a high-temperature gas stream, where they melt and solidify into desired forms.
-
Advantages:
- Suitable for high-temperature materials.
- Produces fine, uniform particles.
-
Limitations:
- Complex and expensive equipment.
- Limited to specific applications.
-
Arc Melting
- Definition: Arc melting uses an electric arc to generate intense heat, melting materials in a controlled environment.
- Applications: Commonly used for producing high-purity metals and alloys, such as titanium and zirconium.
- Mechanism: An electric arc is created between an electrode and the material, generating temperatures high enough to melt the material.
-
Advantages:
- Produces high-purity metals.
- Suitable for reactive and refractory metals.
-
Limitations:
- Requires a controlled atmosphere (e.g., vacuum or inert gas).
- High energy consumption.
Summary of Key Differences:
Process | Primary Use | Mechanism | Advantages | Limitations |
---|---|---|---|---|
Smelting | Metal extraction from ores | Heating with reducing agents | Large-scale efficiency | High energy use, waste generation |
Induction Melting | Melting conductive metals | Electromagnetic induction | Precision, cleanliness | High equipment cost, material limit |
Suspension Melting | High-temperature materials | Suspension in high-temperature gas | Fine particle production | Complex and costly |
Arc Melting | High-purity metals/alloys | Electric arc heating | High purity, reactive metals | Controlled environment needed |
By understanding these melting processes, purchasers and engineers can make informed decisions about the most suitable method for their specific applications, balancing factors such as cost, efficiency, and material requirements.
Summary Table:
Process | Primary Use | Mechanism | Advantages | Limitations |
---|---|---|---|---|
Smelting | Metal extraction from ores | Heating with reducing agents | Large-scale efficiency | High energy use, waste generation |
Induction Melting | Melting conductive metals | Electromagnetic induction | Precision, cleanliness | High equipment cost, material limit |
Suspension Melting | High-temperature materials | Suspension in high-temperature gas | Fine particle production | Complex and costly |
Arc Melting | High-purity metals/alloys | Electric arc heating | High purity, reactive metals | Controlled environment needed |
Need help choosing the right melting process for your application? Contact our experts today!