Pelletizers are essential equipment in various industries, particularly in pharmaceuticals, food processing, and chemical manufacturing, where they are used to convert powdered or granular materials into uniform pellets. The choice of pelletizer depends on the material properties, desired pellet size, production capacity, and specific application requirements. There are several types of pelletizers, each with unique mechanisms and advantages, including extrusion pelletizers, rotary pelletizers, fluidized bed pelletizers, and spheronizers. Understanding the differences between these types helps in selecting the most suitable equipment for a given process.
Key Points Explained:
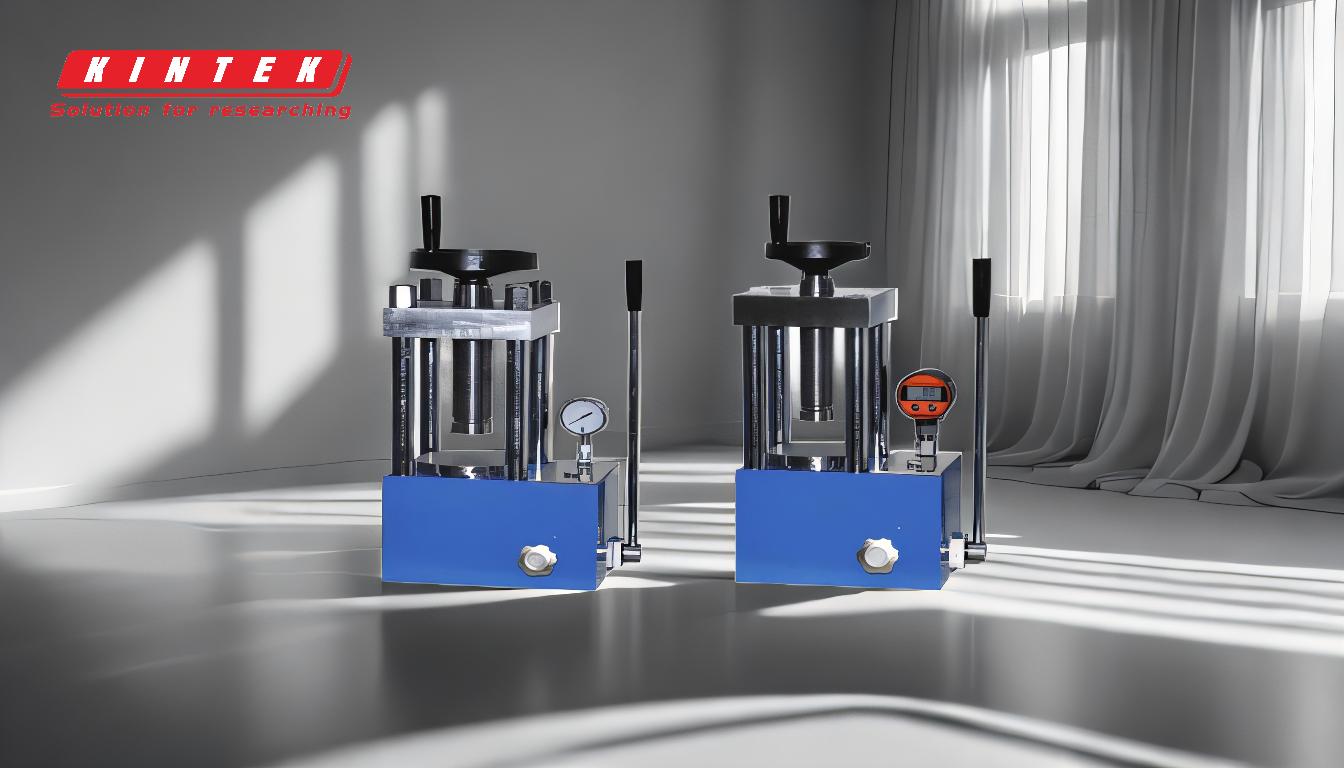
-
Extrusion Pelletizers:
- Extrusion pelletizers are widely used for their ability to produce dense and uniform pellets. They work by forcing material through a die under high pressure, which is then cut into pellets by rotating blades.
- Applications: Commonly used in the pharmaceutical industry for creating drug pellets and in the food industry for producing animal feed and snacks.
- Advantages: High production capacity, consistent pellet size, and suitability for a wide range of materials.
- Limitations: Requires significant energy input and may not be suitable for heat-sensitive materials.
-
Rotary Pelletizers:
- Rotary pelletizers, also known as drum pelletizers, use a rotating drum to agglomerate fine particles into larger pellets. The material is fed into the drum, and as it rotates, the particles stick together, forming pellets.
- Applications: Ideal for industries like mining and fertilizers, where large-scale pellet production is required.
- Advantages: Scalable for high-capacity production, low maintenance, and effective for materials that require gentle handling.
- Limitations: Less precise control over pellet size compared to extrusion methods.
-
Fluidized Bed Pelletizers:
- Fluidized bed pelletizers use a stream of air to suspend particles in a chamber, where they are coated with a binding agent and agglomerated into pellets. This method is particularly effective for creating porous or lightweight pellets.
- Applications: Suitable for pharmaceutical and chemical industries, especially for producing controlled-release pellets or granules.
- Advantages: Gentle processing, ideal for heat-sensitive materials, and ability to produce pellets with specific porosity.
- Limitations: Higher operational complexity and cost compared to other methods.
-
Spheronizers:
- Spheronizers are specialized equipment used to create spherical pellets. The process involves extruding the material into cylindrical shapes, which are then placed in a spheronizer to round them into spheres through friction and centrifugal force.
- Applications: Primarily used in the pharmaceutical industry for producing uniform, spherical pellets for drug delivery systems.
- Advantages: Produces highly uniform and spherical pellets, ideal for applications requiring precise dosing.
- Limitations: Limited to materials that can withstand the mechanical forces involved in the spheronization process.
-
Selection Criteria:
- Material Properties: Consider the physical and chemical properties of the material, such as moisture content, particle size, and heat sensitivity.
- Pellet Size and Shape: Determine the required pellet size and shape, as different pelletizers produce varying results.
- Production Capacity: Evaluate the production volume needed, as some pelletizers are better suited for high-capacity operations.
- Cost and Maintenance: Factor in the initial investment, operational costs, and maintenance requirements of the equipment.
By understanding the different types of pelletizers and their respective advantages and limitations, you can make an informed decision when selecting the most appropriate equipment for your specific application. Each type offers unique benefits, and the choice ultimately depends on your production goals and material characteristics.
Summary Table:
Type of Pelletizer | Mechanism | Applications | Advantages | Limitations |
---|---|---|---|---|
Extrusion Pelletizers | Forces material through a die, cut by rotating blades | Pharmaceuticals, food processing (animal feed, snacks) | High production capacity, consistent pellet size | High energy use, not ideal for heat-sensitive materials |
Rotary Pelletizers | Rotating drum agglomerates particles | Mining, fertilizers | Scalable, low maintenance, gentle handling | Less precise pellet size control |
Fluidized Bed Pelletizers | Air suspends particles, binding agent forms pellets | Pharmaceuticals, chemicals (controlled-release pellets) | Gentle processing, ideal for heat-sensitive materials | Higher cost, operational complexity |
Spheronizers | Extrudes material into spheres via friction and centrifugal force | Pharmaceuticals (drug delivery systems) | Uniform, spherical pellets | Limited to durable materials |
Need help choosing the right pelletizer for your application? Contact our experts today!