Sintering is a critical process in materials science and manufacturing, involving the consolidation of powder materials into a solid mass through heat and sometimes pressure, without melting the material to the point of liquefaction. There are several types of sintering, each with unique mechanisms and applications. This answer explores the different types of sintering, focusing on their processes, equipment, and applications, with a particular emphasis on the role of a sintering furnace in these processes.
Key Points Explained:
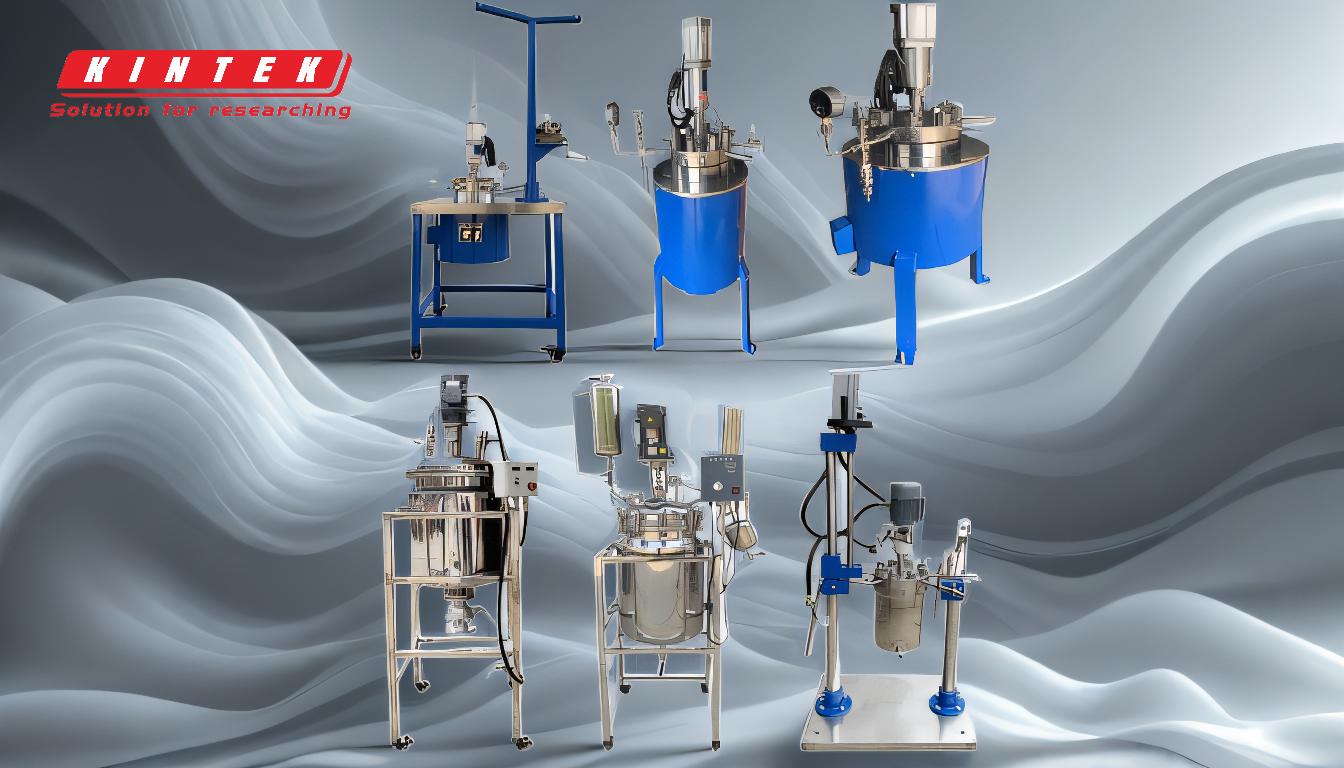
-
Hot Press Sintering
- Process: Involves the application of high temperature and high pressure in a vacuum environment. The ceramic powder is heated to a specific temperature, causing it to melt and fuse into a solid material under high pressure.
- Equipment: Utilizes a specialized sintering furnace that includes a furnace body, heater, pressure system, and vacuum system.
- Applications: Commonly used for producing dense ceramic materials and composites, where high strength and minimal porosity are required.
-
Pressureless Sintering
- Process: The material is sintered at high temperatures without the application of external pressure. The powder particles bond through diffusion mechanisms.
- Equipment: Typically conducted in a standard sintering furnace without the need for a pressure system.
- Applications: Suitable for manufacturing ceramic components where dimensional precision and surface finish are critical.
-
Spark Plasma Sintering (SPS)
- Process: A rapid sintering technique that uses pulsed electric current to generate spark plasma, which heats the powder particles directly and facilitates rapid densification.
- Equipment: Requires a specialized sintering furnace equipped with an electric pulse generator and a die-punch system.
- Applications: Ideal for producing nanostructured materials and composites with enhanced mechanical properties.
-
Microwave Sintering
- Process: Utilizes microwave energy to heat the powder particles volumetrically, leading to uniform heating and faster sintering times.
- Equipment: Conducted in a sintering furnace designed to generate and control microwave energy.
- Applications: Effective for sintering ceramics and metals, especially when rapid processing and energy efficiency are desired.
-
Liquid Phase Sintering
- Process: Involves the presence of a liquid phase during sintering, which enhances the densification process by facilitating particle rearrangement and solution-reprecipitation.
- Equipment: Typically performed in a conventional sintering furnace with controlled atmosphere capabilities.
- Applications: Commonly used in the production of cemented carbides, ferrites, and some ceramic materials.
-
Reactive Sintering
- Process: Combines the sintering process with a chemical reaction, where the reactants form a new compound during the sintering process.
- Equipment: Requires a sintering furnace capable of maintaining precise temperature and atmosphere control.
- Applications: Used in the synthesis of advanced ceramics and intermetallic compounds.
-
Selective Laser Sintering (SLS)
- Process: A type of additive manufacturing where a laser selectively sinters powdered material, layer by layer, to create a 3D object.
- Equipment: Utilizes a specialized sintering furnace integrated with a laser system and powder bed.
- Applications: Widely used in rapid prototyping, custom manufacturing, and the production of complex geometries.
Each type of sintering offers distinct advantages and is chosen based on the material properties desired, the complexity of the part, and the specific application requirements. The sintering furnace plays a pivotal role in each of these processes, providing the necessary environment for heat and pressure application, atmosphere control, and precise temperature management. Understanding these different types of sintering helps in selecting the most appropriate method for a given material and application, ensuring optimal performance and quality of the final product.
Summary Table:
Type of Sintering | Process | Equipment | Applications |
---|---|---|---|
Hot Press Sintering | High temperature and pressure in a vacuum environment. | Specialized sintering furnace with pressure and vacuum systems. | Dense ceramic materials and composites. |
Pressureless Sintering | High-temperature sintering without external pressure. | Standard sintering furnace. | Ceramic components requiring dimensional precision. |
Spark Plasma Sintering | Rapid sintering using pulsed electric current for direct heating. | Sintering furnace with electric pulse generator and die-punch system. | Nanostructured materials and composites. |
Microwave Sintering | Volumetric heating using microwave energy for uniform and fast sintering. | Sintering furnace designed for microwave energy control. | Ceramics and metals requiring rapid processing. |
Liquid Phase Sintering | Sintering with a liquid phase to enhance densification. | Conventional sintering furnace with controlled atmosphere. | Cemented carbides, ferrites, and ceramics. |
Reactive Sintering | Combines sintering with a chemical reaction to form new compounds. | Sintering furnace with precise temperature and atmosphere control. | Advanced ceramics and intermetallic compounds. |
Selective Laser Sintering | Additive manufacturing using a laser to sinter powdered material layer by layer. | Sintering furnace integrated with a laser system and powder bed. | Rapid prototyping, custom manufacturing, and complex geometries. |
Need help choosing the right sintering method for your materials? Contact our experts today!