Thin film deposition is a critical process in various industries, including electronics, optics, and coatings, where thin layers of material are deposited onto substrates to achieve specific properties. The methods of thin film deposition are broadly categorized into Physical Vapor Deposition (PVD) and Chemical Vapor Deposition (CVD), with each category encompassing several techniques. PVD involves physical processes like vaporization of solid materials in a vacuum, while CVD relies on chemical reactions in the vapor phase to deposit thin films. Additionally, some classifications include liquid coating deposition and epitaxial processes as distinct categories. Below, we explore the key types of thin film deposition methods, their mechanisms, and applications.
Key Points Explained:
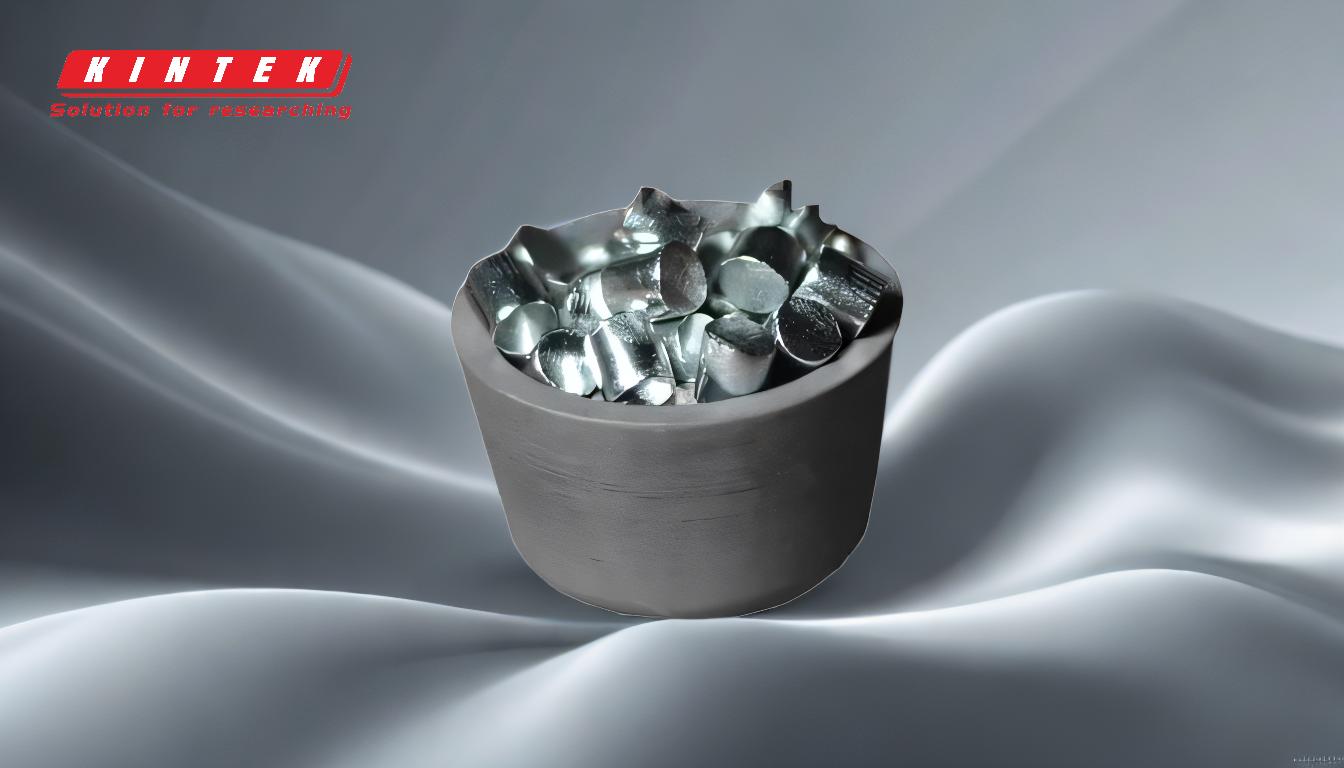
-
Physical Vapor Deposition (PVD)
- Definition: PVD involves the physical vaporization of a solid material in a vacuum environment, which is then deposited onto a substrate.
-
Key Techniques:
- Sputtering: A high-energy process where atoms are ejected from a solid target material due to bombardment by energetic ions. The ejected atoms then deposit onto the substrate.
- Evaporation: The solid material is heated to its vaporization point, and the resulting vapor condenses onto the substrate.
- Sublimation: Similar to evaporation but involves the direct transition of a solid to a gas phase without passing through a liquid phase.
- Applications: PVD is widely used in manufacturing semiconductors, optical coatings, and wear-resistant coatings.
-
Chemical Vapor Deposition (CVD)
- Definition: CVD involves chemical reactions in the vapor phase to produce a thin film on a substrate.
-
Key Techniques:
- Thermal CVD: Uses heat to drive chemical reactions in the vapor phase.
- Plasma-Enhanced CVD (PECVD): Utilizes plasma to lower the reaction temperature, making it suitable for temperature-sensitive substrates.
- Atomic Layer Deposition (ALD): A precise technique where thin films are deposited one atomic layer at a time through sequential chemical reactions.
- Applications: CVD is essential for creating high-purity, uniform films in semiconductor manufacturing, solar cells, and protective coatings.
-
Liquid Coating Deposition
- Definition: This method involves depositing thin films from liquid precursors, often through techniques like spin coating, dip coating, or spray coating.
-
Key Techniques:
- Spin Coating: A liquid precursor is applied to a substrate, which is then spun at high speeds to spread the liquid into a uniform thin layer.
- Dip Coating: The substrate is immersed in a liquid precursor and then withdrawn at a controlled speed to form a thin film.
- Spray Coating: The liquid precursor is atomized into fine droplets and sprayed onto the substrate.
- Applications: Liquid coating deposition is commonly used in photoresist applications, anti-reflective coatings, and organic electronics.
-
Epitaxial Processes
- Definition: Epitaxy involves the growth of a crystalline thin film on a crystalline substrate, where the film’s crystal structure aligns with the substrate.
-
Key Techniques:
- Molecular Beam Epitaxy (MBE): A highly controlled process where atoms or molecules are deposited onto the substrate in an ultra-high vacuum.
- Chemical Beam Epitaxy (CBE): Combines aspects of CVD and MBE, using chemical precursors to grow thin films.
- Applications: Epitaxial processes are crucial for producing high-quality semiconductor materials used in advanced electronics and optoelectronics.
-
Comparison of PVD and CVD
-
PVD Advantages:
- High deposition rates.
- Suitable for a wide range of materials, including metals, alloys, and ceramics.
- Environmentally friendly, as it typically does not involve hazardous chemicals.
-
CVD Advantages:
- Produces high-purity, uniform films.
- Can deposit complex materials like nitrides, carbides, and oxides.
- Suitable for conformal coatings on complex geometries.
-
PVD Advantages:
-
Emerging and Hybrid Techniques
- Hybrid Methods: Combining PVD and CVD techniques to leverage the advantages of both, such as improved film quality and versatility.
- Emerging Techniques: Innovations like pulsed laser deposition (PLD) and ion beam-assisted deposition (IBAD) are gaining traction for specialized applications.
By understanding these categories and techniques, equipment and consumable purchasers can make informed decisions based on the specific requirements of their applications, such as film quality, material compatibility, and process scalability.
Summary Table:
Method | Key Techniques | Applications |
---|---|---|
Physical Vapor Deposition (PVD) | Sputtering, Evaporation, Sublimation | Semiconductors, Optical Coatings, Wear-Resistant Coatings |
Chemical Vapor Deposition (CVD) | Thermal CVD, Plasma-Enhanced CVD (PECVD), Atomic Layer Deposition (ALD) | Semiconductor Manufacturing, Solar Cells, Protective Coatings |
Liquid Coating Deposition | Spin Coating, Dip Coating, Spray Coating | Photoresist, Anti-Reflective Coatings, Organic Electronics |
Epitaxial Processes | Molecular Beam Epitaxy (MBE), Chemical Beam Epitaxy (CBE) | Advanced Electronics, Optoelectronics |
Need help selecting the right thin film deposition method for your application? Contact our experts today!