Muffle furnaces, while highly effective for high-temperature applications, come with several disadvantages that users should be aware of. These include slower heating times compared to open-flame methods, limited accessibility to the interior, and safety concerns such as the risk of burns, electric shock, and fire hazards. Additionally, muffle furnaces require careful handling of materials to avoid damage to the heating elements and ensure safe operation. Proper protective equipment, adherence to safety protocols, and consideration of operational limitations are essential when using a muffle furnace.
Key Points Explained:
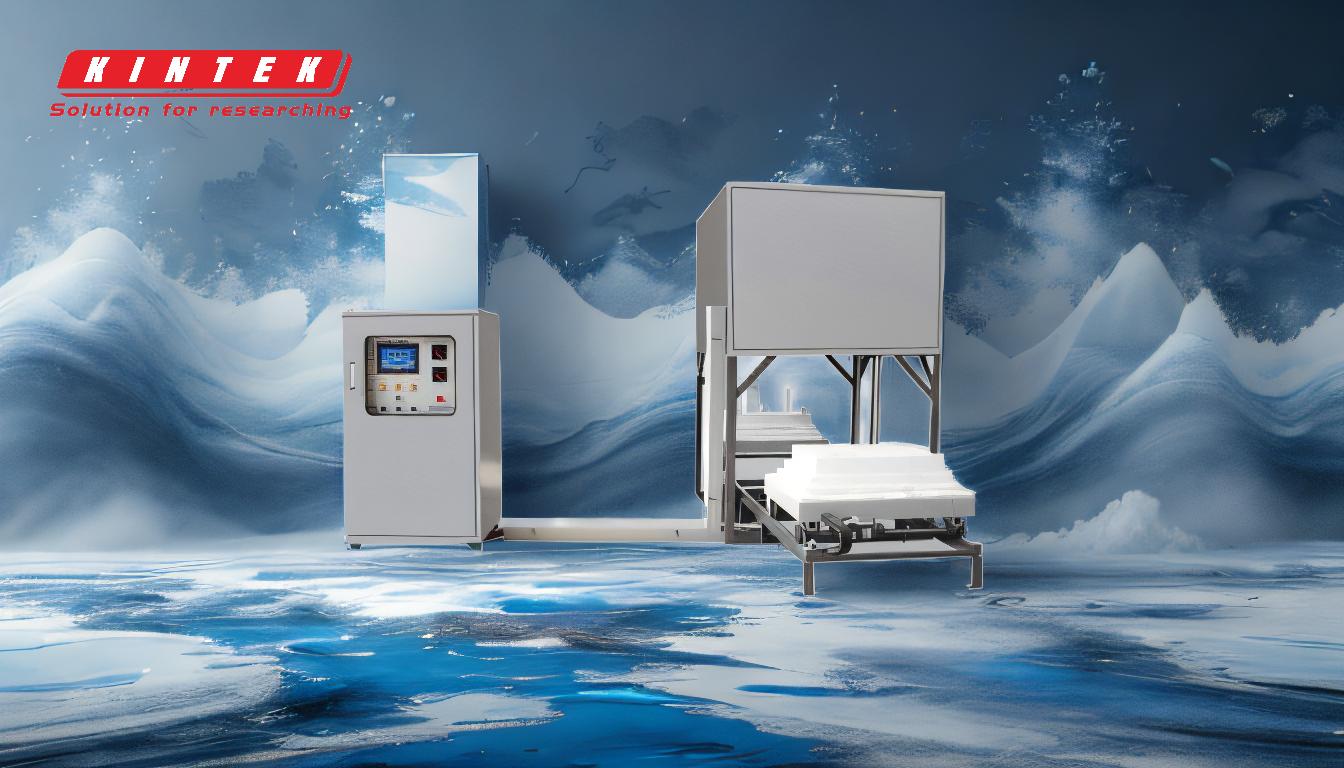
-
Slower Heating Times
- Muffle furnaces take longer to reach the desired temperature compared to open-flame heating methods. This makes them less suitable for applications requiring rapid warm-ups or quick results.
- The enclosed design, which is essential for maintaining consistent temperatures and preventing contamination, contributes to the slower heating process.
-
Limited Accessibility
- The design of a muffle furnace makes it harder to access the interior during operation. Users must carefully place materials inside before heating begins, as adjustments or additions during the process are challenging.
- This limitation can be particularly inconvenient for experiments or processes requiring frequent monitoring or modification of samples.
-
Safety Hazards
- Risk of Burns: The furnace reaches extremely high temperatures, posing a risk of burns if users come into contact with the exterior or interior surfaces. Proper protective equipment, such as heat-resistant gloves and goggles, is essential.
- Electric Shock: Loading or unloading samples while the furnace is powered can lead to electric shock. It is critical to cut off the power supply during these operations.
- Fire Hazards: Materials containing fats or oils can release volatile gases, increasing the risk of fire. Additionally, quenching oil used in some processes can catch fire if not handled carefully.
-
Material Handling Precautions
- Samples with water or oil content should not be placed in the furnace, as they can cause splattering, damage to the heating elements, or even explosions.
- Volatile or corrosive gases released during heating can degrade the heating elements, reducing their lifespan and requiring costly replacements.
-
Operational Limitations
- Exceeding the maximum temperature of the furnace can damage the heating elements and compromise safety. Users must ensure the furnace is not overloaded or operated beyond its specified limits.
- Sudden temperature changes, such as pulling out a thermocouple at high temperatures, can cause equipment failure or safety incidents.
-
Maintenance and Grounding Requirements
- Proper grounding of both the furnace and its controller is essential to prevent electrical hazards.
- Installing an additional power switch at the power line entry point ensures better control over the main power supply, enhancing safety during operation.
-
Cost and Complexity
- Advanced features such as programmable controls, alarms, and timers can increase the cost of a muffle furnace. While these features improve usability, they may not be necessary for all applications.
- The need for regular maintenance and adherence to strict safety protocols adds to the operational complexity and cost.
In summary, while muffle furnaces are invaluable for high-temperature applications, their disadvantages—such as slower heating times, limited accessibility, and safety concerns—must be carefully managed. Proper training, adherence to safety protocols, and consideration of operational limitations are essential for safe and effective use.
Summary Table:
Disadvantage | Key Details |
---|---|
Slower Heating Times | Longer warm-up compared to open-flame methods; less suitable for rapid results. |
Limited Accessibility | Harder to access interior during operation; inconvenient for frequent changes. |
Safety Hazards | Risk of burns, electric shock, and fire hazards; requires protective equipment. |
Material Handling | Avoid water/oil samples to prevent splattering, explosions, or element damage. |
Operational Limitations | Exceeding temperature limits or sudden changes can damage equipment. |
Maintenance Requirements | Proper grounding, power control, and regular maintenance are essential. |
Cost and Complexity | Advanced features and safety protocols increase operational costs. |
Need help choosing or operating a muffle furnace? Contact our experts today for personalized advice!