Chemical Bath Deposition (CBD) is a widely used technique for depositing thin films, particularly in the production of semiconductors, solar cells, and other electronic devices. However, like any other deposition method, it has its own set of disadvantages. These include issues related to the toxicity of chemicals used, the need for precise control over deposition conditions, limitations in the types of materials that can be deposited, and challenges in scaling up the process for industrial applications. Understanding these drawbacks is crucial for researchers and engineers to optimize the process and mitigate potential risks.
Key Points Explained:
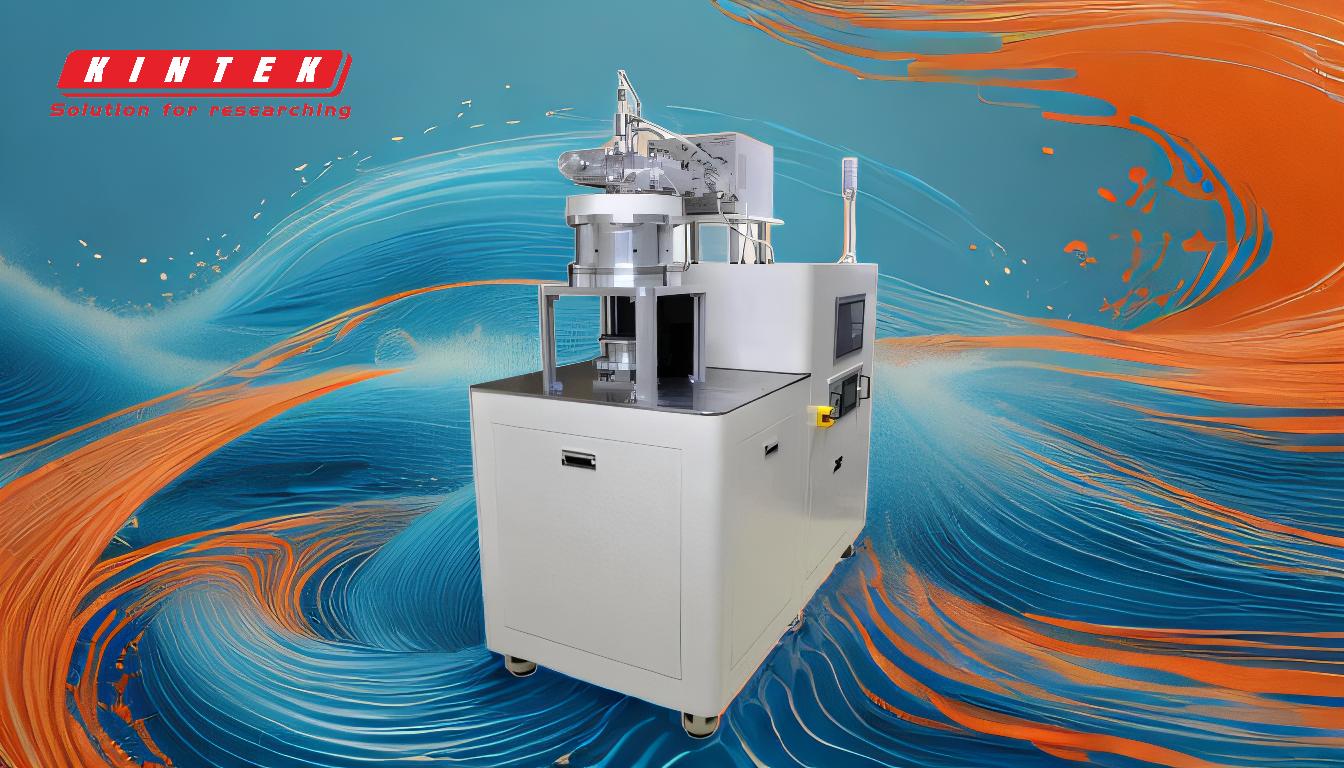
-
Toxicity and Environmental Concerns:
- Chemical Handling: CBD involves the use of various chemicals, some of which are highly toxic and hazardous. For example, cadmium sulfide (CdS) and other metal sulfides are commonly used in CBD, and these materials can pose significant health risks if not handled properly. The disposal of these chemicals also requires careful management to prevent environmental contamination.
- Waste Management: The byproducts of the CBD process can be toxic and corrosive, necessitating specialized waste treatment facilities. This adds to the overall cost and complexity of the process, particularly in industrial settings where large volumes of waste are generated.
-
Precision and Control:
- Deposition Rate: One of the challenges with CBD is controlling the deposition rate. The process is highly sensitive to factors such as temperature, pH, and the concentration of reactants. Even slight variations in these parameters can lead to significant differences in the quality and thickness of the deposited film.
- Uniformity: Achieving uniform deposition over large areas can be difficult with CBD. The process tends to be more effective for small, flat surfaces, but when applied to larger or more complex geometries, it may result in uneven coatings. This limitation can be a significant drawback in applications where uniform film thickness is critical.
-
Material Limitations:
- Limited Material Choices: CBD is primarily used for depositing metal sulfides, oxides, and hydroxides. While these materials are useful in many applications, the technique is not suitable for depositing a wide range of other materials, such as metals or complex alloys. This restricts the versatility of CBD compared to other deposition methods like Chemical Vapor Deposition (CVD) or Physical Vapor Deposition (PVD).
- Multi-Component Materials: Synthesizing multi-component materials using CBD can be challenging due to variations in the deposition rates of different components. This can lead to films with heterogeneous compositions, which may not meet the desired specifications for certain applications.
-
Scalability and Industrial Application:
- Batch Processing: CBD is typically a batch process, meaning that it is not well-suited for continuous, high-throughput production. This can be a significant limitation in industrial settings where large volumes of material need to be processed quickly and efficiently.
- Equipment Limitations: The equipment used in CBD, such as reaction baths and temperature control systems, can be relatively simple and inexpensive compared to other deposition methods. However, scaling up the process for industrial production often requires more sophisticated and costly equipment, which can offset some of the initial cost advantages.
-
Temperature Sensitivity:
- Substrate Limitations: While CBD generally operates at lower temperatures compared to methods like CVD, the process can still be sensitive to temperature variations. Some substrates may not tolerate even the relatively mild temperatures used in CBD, leading to issues such as thermal stress or degradation of the substrate material.
- Thermal Expansion: Differences in the thermal expansion coefficients between the substrate and the deposited film can lead to stress and potential delamination, particularly when the coated material is subjected to temperature changes during subsequent processing or use.
-
Process Complexity:
- Chemical Complexity: The CBD process involves multiple chemical reactions, including nucleation, growth, and precipitation. Each of these stages must be carefully controlled to achieve the desired film properties. This complexity can make the process difficult to optimize, particularly for new or less-experienced users.
- Post-Deposition Treatment: In many cases, films deposited using CBD require additional post-deposition treatments, such as annealing, to achieve the desired properties. These additional steps can add to the overall time and cost of the process.
In conclusion, while Chemical Bath Deposition offers several advantages, such as simplicity and cost-effectiveness for certain applications, it also comes with significant disadvantages. These include issues related to chemical toxicity, challenges in achieving uniform and controlled deposition, limitations in material choices, difficulties in scaling up for industrial production, and sensitivity to temperature and process conditions. Understanding these drawbacks is essential for optimizing the CBD process and ensuring its safe and effective use in various applications.
Summary Table:
Disadvantage | Key Challenges |
---|---|
Toxicity & Environmental | Handling hazardous chemicals, costly waste management, and environmental risks. |
Precision & Control | Sensitive to temperature, pH, and reactant concentration; uneven film deposition. |
Material Limitations | Limited to metal sulfides, oxides, and hydroxides; challenges with multi-components. |
Scalability | Batch processing limits high-throughput production; costly scaling for industries. |
Temperature Sensitivity | Substrate degradation and thermal stress due to temperature variations. |
Process Complexity | Requires precise control of chemical reactions; often needs post-deposition treatments. |
Need help optimizing your Chemical Bath Deposition process? Contact our experts today for tailored solutions!