Conformal coatings, while beneficial for protecting electronic components from environmental factors, come with several disadvantages. These include challenges in masking specific areas, limitations due to the size of the reaction chamber, and the requirement for parts to be broken down into individual components. Additionally, the process is not suitable for on-site application, which can be a significant limitation for certain industries. Furthermore, the aggressive nature of some coating processes, such as PVD, can lead to material wastage and require expensive, specialized equipment and expertise.
Key Points Explained:
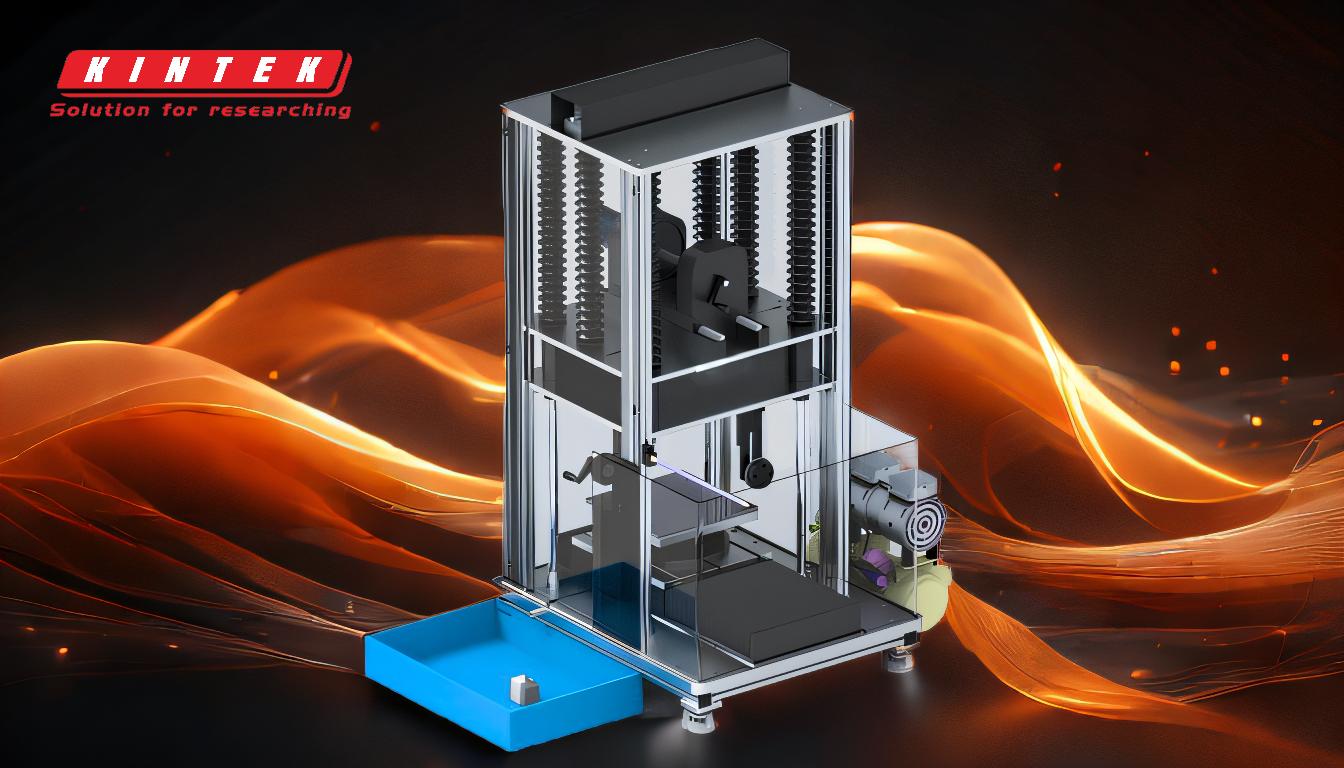
-
Difficulty in Masking Specific Areas:
- Conformal coatings, especially those applied through Chemical Vapor Deposition (CVD), are typically applied at higher temperatures. This makes it challenging to mask specific areas that do not require coating, leading to potential issues in precision applications.
-
Size Limitations:
- The process is size-limited to the capacity of the reaction chamber. This means that larger components or assemblies may need to be broken down into individual parts, which can be time-consuming and may increase the complexity of the coating process.
-
Not Suitable for On-Site Application:
- Conformal coating processes like CVD are not designed for on-site application. This can be a significant drawback for industries that require immediate or on-site protection for their components, as it necessitates transportation to a specialized facility.
-
Material Wastage:
- Some coating processes, such as Physical Vapor Deposition (PVD), can aggressively destroy colors, leading to material wastage. This not only increases costs but also raises environmental concerns due to the unnecessary consumption of materials.
-
Specialized Equipment and Expertise:
- The application of conformal coatings often requires specialized equipment, such as large vacuum chambers for PVD. This equipment can be expensive to purchase and maintain. Additionally, the process demands a high level of expertise, which can further increase operational costs.
-
Cost Implications:
- The need for specialized equipment and expertise, combined with potential material wastage, can significantly increase the overall cost of applying conformal coatings. This can be a deterrent for smaller companies or those with limited budgets.
-
Environmental and Safety Concerns:
- The high temperatures and specialized equipment required for conformal coating processes can pose environmental and safety concerns. Proper ventilation, safety protocols, and waste management practices must be in place to mitigate these risks.
In summary, while conformal coatings offer significant protection for electronic components, the disadvantages such as difficulty in masking, size limitations, lack of on-site application capability, material wastage, high costs, and environmental concerns must be carefully considered when deciding whether to use this technology.
Summary Table:
Disadvantage | Description |
---|---|
Difficulty in Masking Specific Areas | High-temperature application makes masking precision areas challenging. |
Size Limitations | Limited by reaction chamber size; larger components may need disassembly. |
Not Suitable for On-Site Application | Requires specialized facilities, limiting on-site use. |
Material Wastage | Aggressive processes like PVD can lead to material wastage and higher costs. |
Specialized Equipment and Expertise | Requires expensive equipment and skilled operators, increasing operational costs. |
Cost Implications | High costs due to equipment, expertise, and material wastage. |
Environmental and Safety Concerns | High temperatures and equipment pose safety and environmental risks. |
Considering conformal coatings for your project? Contact us today to discuss your needs and find the right solution!