Crucible furnaces, including graphite crucible furnaces, are widely used in various industries for melting metals, alloys, glass, and ceramics due to their versatility, ease of operation, and cost-effectiveness. However, they also come with several disadvantages that can affect their efficiency, safety, and suitability for certain applications. These drawbacks include low thermal efficiency, high emissions, size limitations, crucible wear and tear, safety risks, and material compatibility issues. Understanding these disadvantages is crucial for making informed decisions when selecting a furnace for specific industrial or laboratory needs.
Key Points Explained:
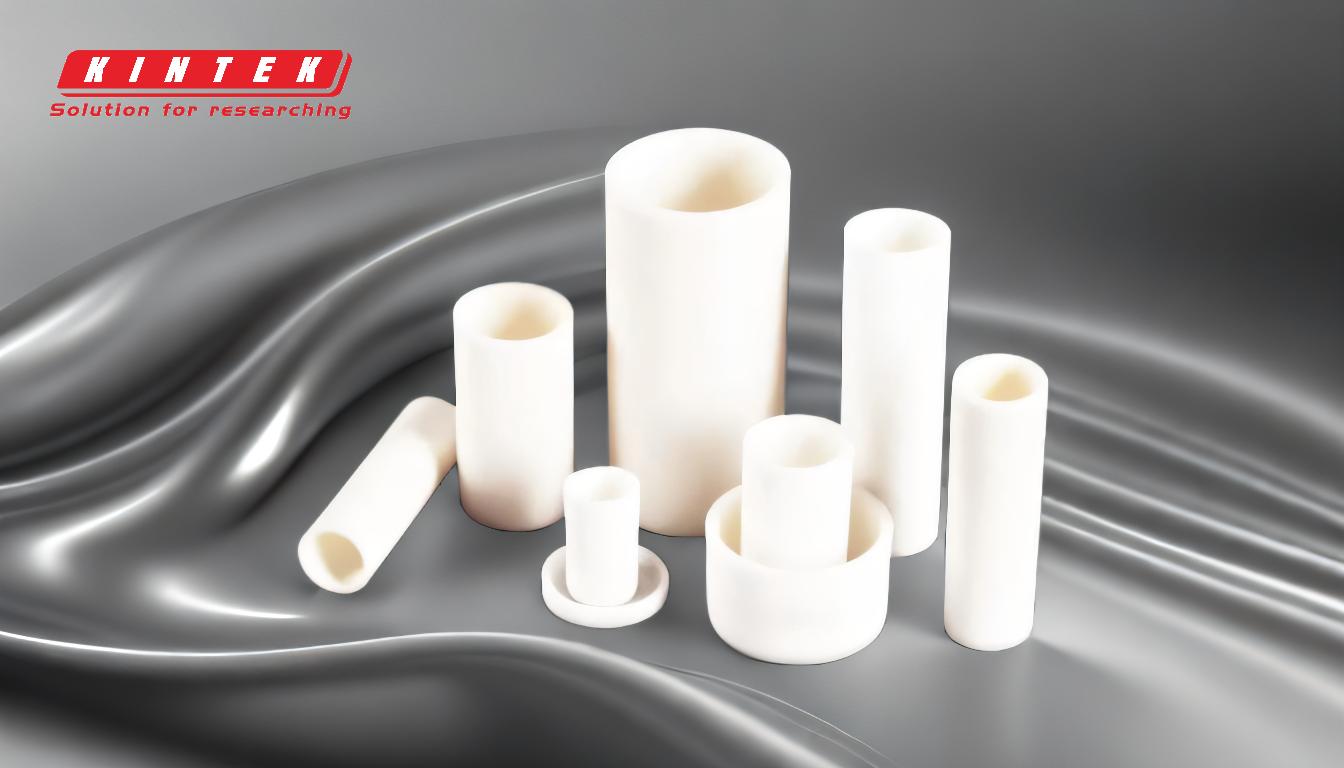
-
Low Thermal Efficiency:
- Crucible furnaces often have low thermal efficiency, sometimes as low as 12%. This inefficiency results in higher energy consumption and increased operational costs.
- The heat loss is primarily due to the open design of the furnace, which allows heat to escape into the surrounding environment.
- For industries requiring frequent melting operations, this inefficiency can lead to significant energy waste and higher fuel costs, especially in electric crucible furnaces.
-
High Emissions:
- Traditional crucible furnaces, particularly those fueled by gas or oil, tend to produce high levels of emissions, including harmful gases and particulate matter.
- These emissions can contribute to environmental pollution and may require additional equipment, such as scrubbers or filters, to meet regulatory standards.
- While electric crucible furnaces reduce emissions, they are not entirely emission-free and may still produce some pollutants depending on the materials being melted.
-
Size Limitations:
- Crucible furnaces are generally limited in size, making them unsuitable for large-scale industrial applications that require melting large quantities of material.
- The compact design, while advantageous for small-scale or laboratory use, restricts the volume of material that can be processed at once.
- This limitation can result in longer processing times and reduced productivity for industries with high-volume melting needs.
-
Crucible Wear and Tear:
- The crucible itself is subject to wear and tear over time, especially when exposed to high temperatures and corrosive materials.
- Frequent replacement of crucibles can increase maintenance costs and downtime, affecting overall operational efficiency.
- The choice of crucible material (e.g., graphite, clay, or ceramic) can mitigate this issue to some extent, but it does not eliminate the need for regular maintenance.
-
Safety Risks:
- Operating a crucible furnace involves high temperatures, which pose significant safety risks to workers if proper precautions are not taken.
- Risks include burns, fires, and exposure to toxic fumes, particularly when melting certain alloys or materials.
- Adequate safety measures, such as protective gear, proper training, and ventilation systems, are essential to minimize these risks.
-
Material Compatibility Issues:
- Not all materials are suitable for melting in a crucible furnace due to their chemical composition or physical properties.
- For example, some materials may react with the crucible material, leading to contamination of the melt or damage to the crucible.
- Careful selection of crucible material and furnace design is necessary to ensure compatibility with the specific materials being processed.
-
Temperature Control Challenges:
- Maintaining precise temperature control in a crucible furnace can be challenging, particularly for materials with narrow melting ranges.
- Overheating or underheating can result in poor-quality melts, affecting the final product's properties.
- Advanced temperature monitoring and control systems can help address this issue, but they may add to the overall cost of the furnace.
By understanding these disadvantages, users can better evaluate whether a crucible furnace, including a graphite crucible furnace, is the right choice for their specific application. While crucible furnaces offer many advantages, their limitations must be carefully considered to ensure optimal performance and safety.
Summary Table:
Disadvantage | Key Details |
---|---|
Low Thermal Efficiency | Heat loss due to open design; energy consumption increases; efficiency as low as 12%. |
High Emissions | Gas/oil-fueled furnaces produce harmful emissions; electric furnaces reduce but not eliminate emissions. |
Size Limitations | Compact design restricts volume; unsuitable for large-scale industrial applications. |
Crucible Wear and Tear | Frequent replacement increases maintenance costs; material choice affects durability. |
Safety Risks | High temperatures pose risks like burns, fires, and toxic fume exposure. |
Material Compatibility Issues | Some materials react with crucible, causing contamination or damage. |
Temperature Control Challenges | Precise control is difficult; overheating or underheating affects melt quality. |
Need help choosing the right furnace for your application? Contact our experts today!