Induction furnaces, while highly efficient and versatile for melting metals, come with several notable disadvantages. One of the primary drawbacks is their lack of refining capacity, which means the charge materials must already be free of oxides and have a known composition. Additionally, certain alloying elements can be lost due to oxidation during the melting process, necessitating their re-addition. These limitations can increase operational complexity and costs. Below, we explore these and other disadvantages in detail.
Key Points Explained:
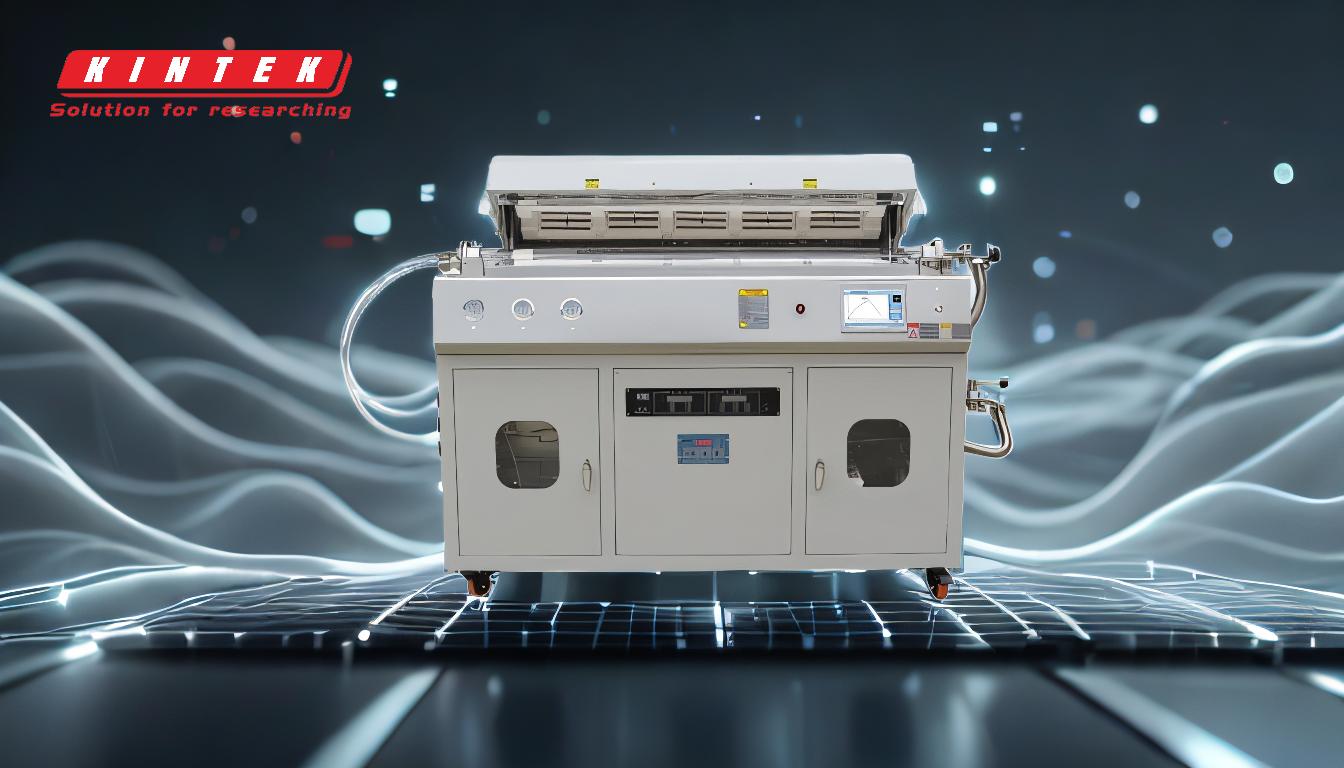
-
Lack of Refining Capacity
- Induction furnaces do not have the ability to refine the metal during the melting process. This means that the charge materials must be clean, free of oxides, and of a known composition before being introduced into the furnace.
- For industries requiring high-purity metals, this limitation can be a significant drawback, as it necessitates additional pre-processing steps to ensure the quality of the charge materials.
-
Oxidation and Loss of Alloying Elements
- During the melting process, certain alloying elements, such as magnesium, aluminum, and silicon, can oxidize and be lost from the melt.
- This requires operators to monitor the melt composition carefully and re-add these elements, which can increase both material costs and processing time.
-
Dependence on Charge Material Quality
- Since induction furnaces rely on the quality of the charge materials, any impurities or inconsistencies in the feedstock can directly affect the final product.
- This makes it challenging to use scrap or recycled materials without thorough sorting and preparation, which can add to operational costs.
-
High Initial Investment and Operational Costs
- Induction furnaces, particularly those using advanced technologies like IGBT induction furnaces, require a significant initial investment.
- Additionally, the operational costs, including electricity consumption and maintenance, can be higher compared to other types of furnaces.
-
Limited Capacity for Large-Scale Production
- Induction furnaces are typically better suited for smaller-scale operations or batch production. For large-scale continuous production, other types of furnaces, such as arc furnaces, may be more efficient.
- This limitation can make induction furnaces less suitable for industries requiring high-volume output.
-
Complexity in Temperature Control
- While induction furnaces offer precise temperature control, maintaining consistent temperatures throughout the melt can be challenging, especially for larger furnaces.
- Variations in temperature can lead to inconsistencies in the final product, requiring careful monitoring and adjustment.
-
Susceptibility to Power Supply Issues
- Induction furnaces are highly dependent on a stable and reliable power supply. Any fluctuations or interruptions in power can disrupt the melting process and potentially damage the furnace.
- This makes them less suitable for areas with unreliable electricity infrastructure.
-
Limited Flexibility for Certain Metals
- While induction furnaces are versatile, they may not be ideal for melting certain metals or alloys that require specific refining processes or atmospheres.
- For example, metals that require vacuum or inert gas environments may not be suitable for standard induction furnaces.
-
Maintenance and Wear of Components
- The components of an induction furnace, such as the crucible and coils, are subject to wear and tear over time.
- Regular maintenance is required to ensure optimal performance, and replacing these components can be costly.
-
Environmental and Safety Concerns
- Induction furnaces generate electromagnetic fields, which can pose safety risks to operators if not properly shielded.
- Additionally, the melting process can produce fumes and emissions, requiring adequate ventilation and environmental controls.
In summary, while induction furnaces offer many advantages, such as energy efficiency and precise temperature control, their disadvantages—including the lack of refining capacity, oxidation of alloying elements, and high operational costs—must be carefully considered when selecting a furnace for specific applications. For industries requiring high-purity metals or large-scale production, alternative furnace types may be more suitable.
Summary Table:
Disadvantage | Description |
---|---|
Lack of Refining Capacity | Cannot refine metals; requires clean, oxide-free charge materials. |
Oxidation of Alloying Elements | Loss of elements like magnesium, aluminum, and silicon during melting. |
Dependence on Charge Quality | Impurities in feedstock affect final product quality. |
High Initial and Operational Costs | Significant investment and higher electricity/maintenance costs. |
Limited Large-Scale Capacity | Better suited for small-scale or batch production, not continuous large-scale. |
Complex Temperature Control | Difficult to maintain consistent temperatures in larger furnaces. |
Power Supply Sensitivity | Requires stable power; interruptions can disrupt operations. |
Limited Metal Flexibility | Not ideal for metals requiring specific refining or controlled atmospheres. |
Component Wear and Maintenance | Regular maintenance and costly component replacements needed. |
Environmental and Safety Risks | Electromagnetic fields and fumes require proper shielding and ventilation. |
Need help choosing the right furnace for your needs? Contact our experts today for personalized advice!