Induction hardening, while effective for improving wear and fatigue resistance in simple workpieces, has several disadvantages. It is not suitable for complex mechanical workpieces due to poor adaptability, limiting its application to simpler parts in assembly line production. Additionally, the process lacks refining capacity, requiring charge materials to be free of oxides and of known composition. Alloying elements may also be lost during the process due to oxidation, necessitating their re-addition to the melt. These limitations make induction hardening less versatile and more challenging to manage in certain manufacturing scenarios.
Key Points Explained:
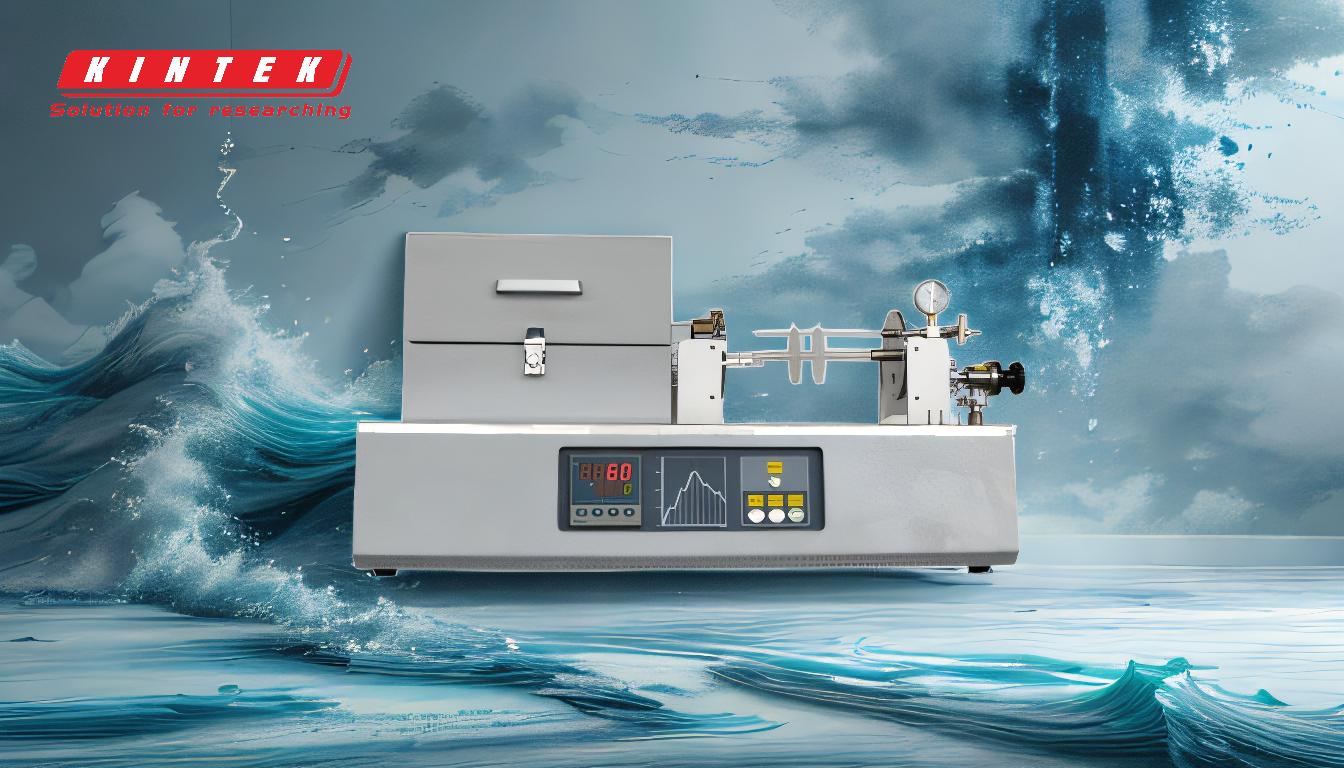
-
Poor Adaptability for Complex Workpieces:
- Induction hardening is primarily effective for simple workpieces, such as those used in assembly line production. However, it struggles with complex mechanical parts due to its limited adaptability. The process requires precise control of heating and cooling, which can be difficult to achieve with intricate geometries. This limitation restricts its use to simpler components, reducing its versatility in manufacturing.
-
Lack of Refining Capacity:
- Unlike other hardening processes, induction hardening does not refine the material. This means that the charge materials used must already be free of oxides and have a known composition. Any impurities or inconsistencies in the material can lead to suboptimal results, making the process less forgiving and more dependent on high-quality input materials.
-
Loss of Alloying Elements:
- During the induction hardening process, some alloying elements may be lost due to oxidation. This can alter the material's properties and reduce the effectiveness of the hardening process. To counteract this, manufacturers may need to re-add these elements to the melt, adding complexity and cost to the process. This issue is particularly problematic when working with materials that require precise alloy compositions for optimal performance.
-
Limited Application Scope:
- The technology's limitations in handling complex shapes and its reliance on high-quality input materials restrict its application scope. It is most suitable for high-volume production of simple parts, where the benefits of improved wear and fatigue resistance can be maximized. However, for more specialized or intricate applications, other hardening methods may be more appropriate.
-
Challenges in Process Control:
- Achieving consistent results with induction hardening requires precise control over the heating and cooling rates. Any deviations can lead to uneven hardening, reducing the effectiveness of the process. This need for tight control can increase the complexity of the manufacturing process and require more sophisticated equipment and expertise.
In summary, while induction hardening offers significant advantages in terms of wear and fatigue resistance for simple workpieces, its disadvantages—such as poor adaptability for complex parts, lack of refining capacity, and potential loss of alloying elements—limit its broader application. These factors make it less suitable for certain manufacturing scenarios, particularly those involving intricate geometries or specialized materials.
Summary Table:
Disadvantage | Description |
---|---|
Poor Adaptability for Complex Parts | Limited effectiveness for intricate geometries, restricting use to simpler components. |
Lack of Refining Capacity | Requires high-quality, oxide-free materials; no refining during the process. |
Loss of Alloying Elements | Oxidation during hardening can lead to loss of alloying elements, requiring re-addition. |
Limited Application Scope | Best suited for high-volume production of simple parts; less effective for specialized materials. |
Challenges in Process Control | Requires precise control of heating and cooling rates for consistent results. |
Need a hardening solution tailored to your needs? Contact us today to explore alternatives!