Liquid phase sintering, while beneficial for enhancing densification and reducing sintering temperatures, comes with several disadvantages. These include challenges with microstructure control, potential for uneven densification, and limitations in material selection due to the need for a compatible liquid phase. Additionally, the process can lead to issues such as grain growth, residual stresses, and anisotropy in properties. The high temperatures and energy consumption associated with liquid phase sintering also contribute to increased operational costs and environmental concerns. Understanding these drawbacks is crucial for optimizing the process and selecting the right materials and parameters for specific applications.
Key Points Explained:
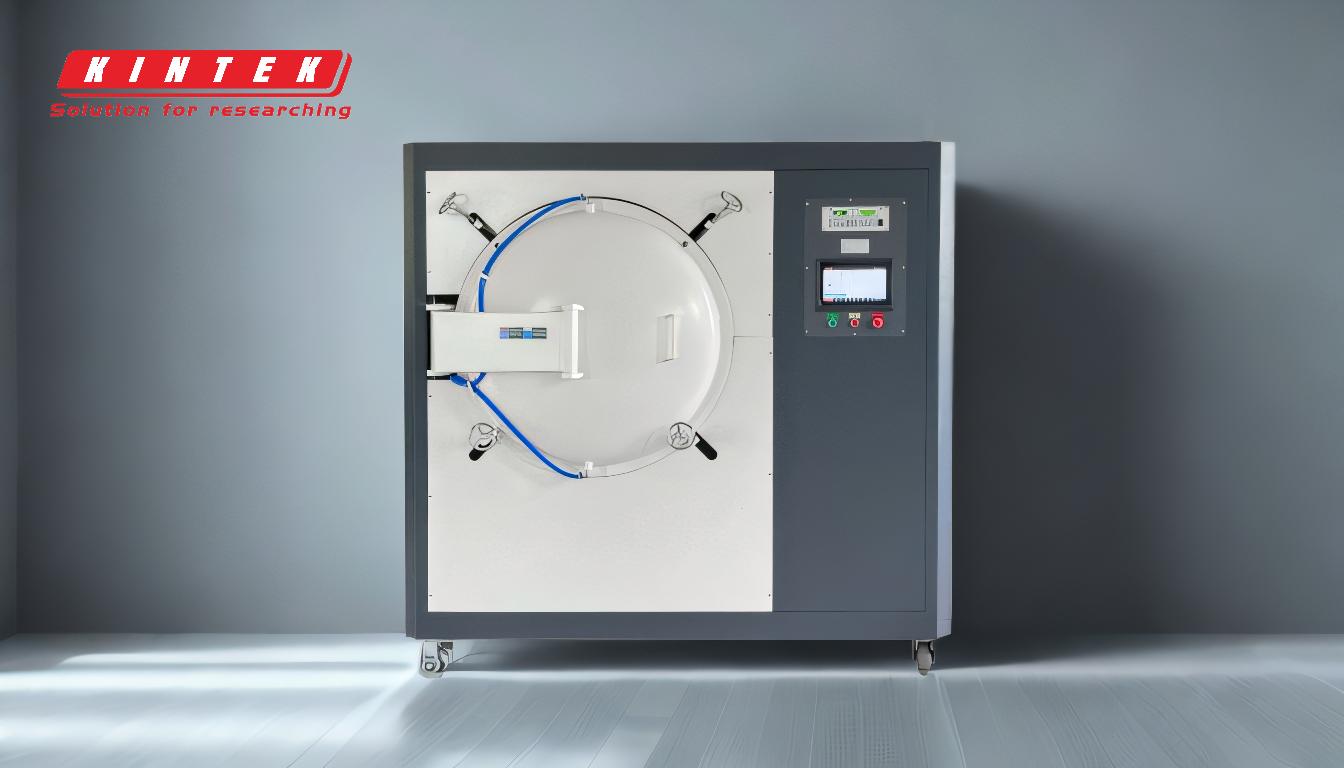
-
Microstructure Control Challenges:
- Liquid phase sintering can lead to uneven grain growth and coarsening, resulting in a less uniform microstructure.
- The presence of a liquid phase can cause localized densification, leading to variations in density and mechanical properties across the sintered part.
-
Anisotropy in Properties:
- The flow of the liquid phase during sintering can cause directional alignment of grains, leading to anisotropy in mechanical, thermal, and electrical properties.
- This anisotropy can be problematic for applications requiring isotropic behavior.
-
Material Selection Limitations:
- Liquid phase sintering requires the formation of a compatible liquid phase, which limits the range of materials that can be effectively sintered using this method.
- The need for specific additives to form the liquid phase can complicate material formulation and increase costs.
-
Residual Stresses and Defects:
- The cooling process after liquid phase sintering can induce residual stresses due to differential shrinkage between the solid and liquid phases.
- These stresses can lead to cracking, warping, or other defects in the final product.
-
High Energy Consumption:
- Liquid phase sintering often requires high temperatures to achieve the necessary liquid phase formation, leading to increased energy consumption.
- This contributes to higher operational costs and environmental impact.
-
Grain Growth and Coarsening:
- The liquid phase can accelerate grain growth, which may degrade the mechanical properties of the sintered material.
- Controlling grain size becomes more challenging, requiring precise control of sintering parameters.
-
Cost and Complexity:
- The equipment and process control required for liquid phase sintering are more complex and expensive compared to solid-state sintering.
- The need for specialized molds, additives, and high-temperature furnaces adds to the overall cost.
-
Shrinkage and Dimensional Control:
- Parts sintered with a liquid phase often experience greater shrinkage, which must be accounted for during the design and production process.
- This can complicate the manufacturing of parts with tight dimensional tolerances.
-
Environmental and Safety Concerns:
- The high temperatures and potential use of hazardous materials in liquid phase sintering can pose safety risks and environmental challenges.
- Proper handling and disposal of materials and by-products are necessary to mitigate these concerns.
By understanding these disadvantages, manufacturers can better evaluate the suitability of liquid phase sintering for their specific applications and take steps to mitigate potential issues through careful process design and material selection.
Summary Table:
Disadvantage | Key Details |
---|---|
Microstructure Control | Uneven grain growth, localized densification, and non-uniform properties. |
Anisotropy in Properties | Directional grain alignment leading to inconsistent mechanical/thermal behavior. |
Material Selection Limitations | Requires compatible liquid phase, limiting material options and increasing costs. |
Residual Stresses and Defects | Differential shrinkage causes cracking, warping, or other defects. |
High Energy Consumption | High temperatures increase energy usage and operational costs. |
Grain Growth and Coarsening | Accelerated grain growth degrades mechanical properties. |
Cost and Complexity | Specialized equipment and additives raise costs and process complexity. |
Shrinkage and Dimensional Control | Greater shrinkage complicates tight tolerance manufacturing. |
Environmental and Safety Concerns | High temperatures and hazardous materials pose risks and environmental issues. |
Need help optimizing your sintering process? Contact our experts today for tailored solutions!