Sintering, a process used to compact and form solid materials using heat and pressure without melting, has several disadvantages that can impact its efficiency and effectiveness. These include challenges related to equipment durability, process control, material requirements, and operational costs. For instance, sintering furnaces, such as pusher plates, face severe thermal-shock loads, especially during rapid quenching, which can lead to material failures. Additionally, the process can be slow, as seen with muffle furnaces, and may require precise control over temperature and pressure to ensure product quality. High equipment costs and the need for professional operation further add to the disadvantages of sintering.
Key Points Explained:
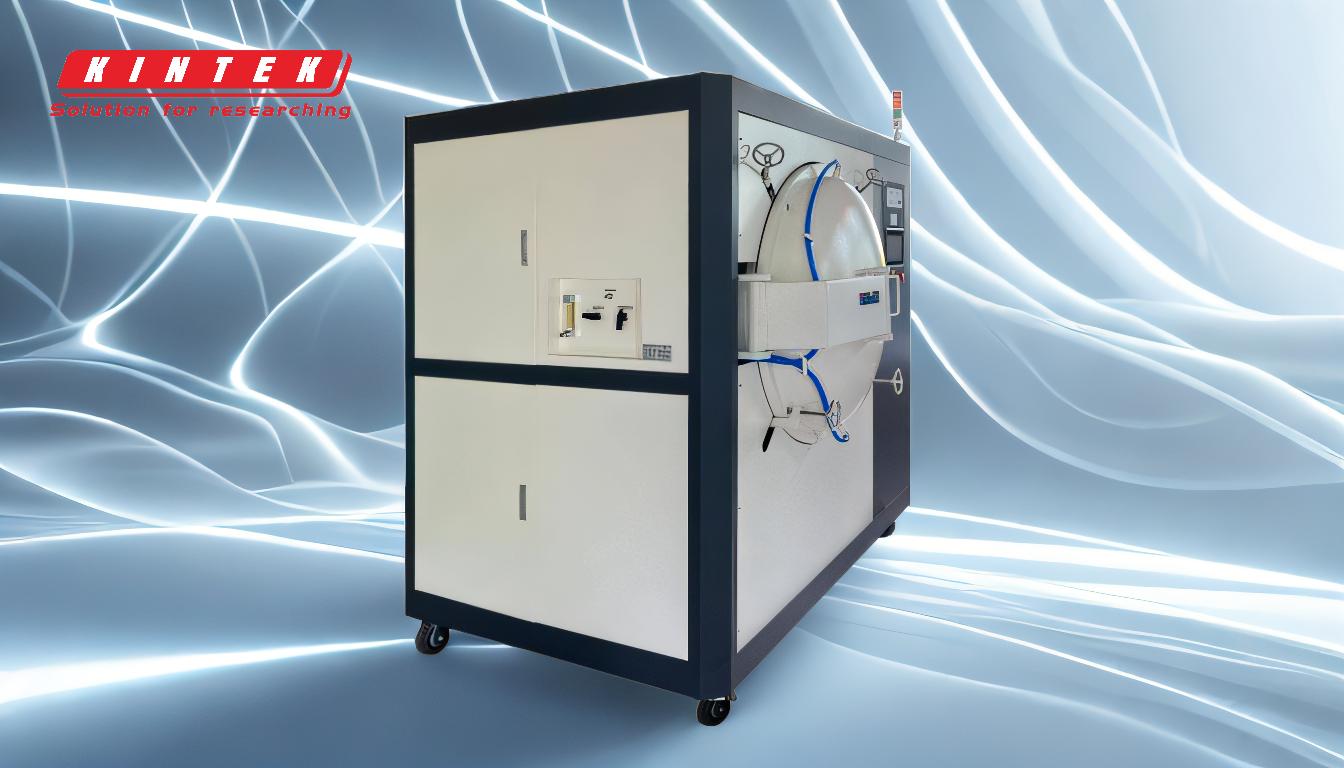
-
Thermal-Shock Loads in Sintering Furnaces:
- Pusher plates in sintering furnaces are subjected to severe thermal-shock loads, particularly when parts are quenched immediately after sintering. This rapid temperature change can cause material failures, especially if the plates are made from high-purity alumina without silica. The lack of silica can make the material more brittle and less resistant to thermal cycling, leading to cracks and other forms of degradation over time.
-
Slow Heating Rates in Muffle Furnaces:
- Muffle furnaces, another type of sintering furnace, take longer to reach the desired temperature compared to open-flame methods. This slow heating rate can be a significant disadvantage for projects that require quick warm-ups and rapid processing. Additionally, the design of muffle furnaces makes it harder to access the interior, requiring careful placement of materials and potentially complicating the sintering process.
-
Lack of Refining Capacity in Induction Furnaces:
- Induction furnaces, while efficient in many respects, lack refining capacity. This means that the charge materials used must be free of oxides and of a known composition. Any impurities or unknown elements can lead to defects in the final product. Furthermore, some alloying elements may be lost due to oxidation during the sintering process, necessitating their re-addition to the melt, which can complicate the process and increase costs.
-
High Equipment and Operational Costs:
- The equipment cost for sintering furnaces, particularly hot press sintering furnaces, is high. These furnaces require precise control over temperature and pressure to ensure uniformity and stability, which can be challenging to achieve. Additionally, the need for professional operation and maintenance adds to the overall cost, making sintering a more expensive option compared to other manufacturing processes.
-
Material and Process Control Challenges:
- Sintering requires precise control over various parameters, including temperature, pressure, and material composition. Any deviation from the optimal conditions can lead to product defects, such as uneven density, cracks, or incomplete sintering. This level of control can be difficult to achieve consistently, especially in large-scale production, leading to potential quality issues and increased waste.
In summary, while sintering is a valuable process for creating solid materials with specific properties, it comes with several disadvantages that can impact its efficiency and cost-effectiveness. These include challenges related to equipment durability, slow heating rates, lack of refining capacity, high equipment and operational costs, and the need for precise process control. Understanding these disadvantages is crucial for making informed decisions about when and how to use sintering in manufacturing processes.
Summary Table:
Disadvantage | Description |
---|---|
Thermal-Shock Loads | Pusher plates face severe thermal-shock loads, leading to material failures. |
Slow Heating Rates | Muffle furnaces take longer to heat, slowing down processing. |
Lack of Refining Capacity | Induction furnaces require pure materials, increasing complexity and costs. |
High Equipment and Operational Costs | Sintering furnaces are expensive and require professional operation. |
Material and Process Control | Precise control over temperature and pressure is challenging and costly. |
Need help optimizing your sintering process? Contact our experts today for tailored solutions!