Vacuum hardening, while offering numerous advantages such as clean processing environments, precise temperature control, and improved mechanical properties, also comes with several disadvantages. These include high initial investment costs, slower heating rates, limitations in production volume due to batch processing, and potential challenges in maintaining uniform heating across large or complex parts. Despite its ability to produce high-quality, contamination-free components, these drawbacks must be carefully considered when choosing vacuum hardening for specific applications.
Key Points Explained:
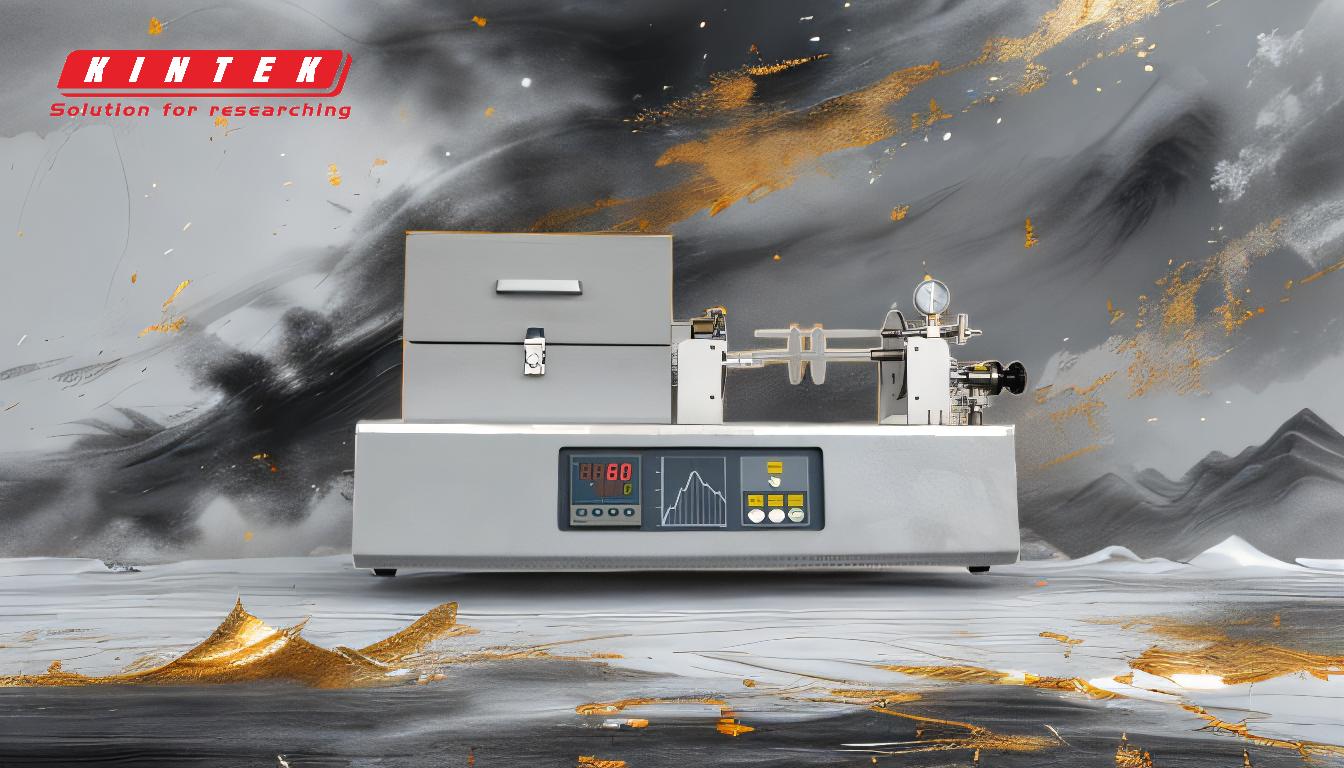
-
High Initial Investment Costs:
- Vacuum hardening furnaces are technologically advanced and require sophisticated construction, leading to significant upfront costs. This can be a barrier for smaller operations or those with limited budgets. The initial investment includes not only the furnace itself but also associated infrastructure and maintenance systems.
-
Slower Heating Rates:
- Compared to other types of furnaces, vacuum furnaces generally have slower heating rates. This can be a disadvantage in processes where rapid heating is crucial. The slower heating can also extend the overall processing time, potentially affecting production schedules.
-
Batch Processing Limitations:
- Vacuum hardening furnaces are typically suited for batch processing rather than continuous production. This can limit the volume of parts that can be processed at any given time, making it less ideal for high-volume manufacturing environments. Batch processing also requires careful planning and grouping of parts, which can add complexity to the workflow.
-
Uniform Heating Challenges:
- Achieving uniform heating across large or complex parts can be challenging in a vacuum furnace. Variations in part geometry and size can lead to uneven heating, which may affect the quality and consistency of the final product. This necessitates careful design and placement of parts within the furnace to minimize temperature gradients.
-
Energy Consumption:
- While vacuum furnaces are designed to be energy-efficient, the need to heat not only the parts but also the fixtures, baskets, or racks used to hold them can increase the overall heat load. This can lead to higher energy consumption compared to other furnace types that do not require such additional heating.
-
Maintenance and Operational Complexity:
- The advanced technology and precise control systems of vacuum furnaces require regular maintenance and skilled operators. Any malfunction or misoperation can lead to costly downtime and potential quality issues. The complexity of the system also means that troubleshooting and repairs can be more challenging and time-consuming.
-
Limited Refining Capacity:
- Similar to induction furnaces, vacuum furnaces have limited refining capacity. The charge materials must be free of oxides and of a known composition to achieve the desired results. Any oxidation or contamination of the charge materials can affect the quality of the hardened parts, necessitating additional steps to ensure material purity.
In summary, while vacuum hardening furnaces offer significant benefits in terms of product quality and process control, their disadvantages in terms of cost, heating rates, production volume, and operational complexity must be carefully weighed against the specific needs and constraints of the application. For more detailed information on vacuum hardening furnaces, you can refer to vacuum hardening furnace.
Summary Table:
Disadvantages of Vacuum Hardening | Details |
---|---|
High Initial Investment Costs | Significant upfront costs for advanced technology and infrastructure. |
Slower Heating Rates | Extended processing times compared to other furnace types. |
Batch Processing Limitations | Limited production volume, less suitable for high-volume manufacturing. |
Uniform Heating Challenges | Difficulties in achieving consistent heating for large or complex parts. |
Energy Consumption | Higher energy use due to heating fixtures and racks. |
Maintenance and Operational Complexity | Requires skilled operators and regular maintenance. |
Limited Refining Capacity | Charge materials must be free of oxides and contamination. |
Need help deciding if vacuum hardening is right for your application? Contact our experts today for personalized advice!