Sintering is a critical process in materials science, driven by various forces and mechanisms that facilitate the bonding and densification of powder particles into a solid structure. The primary driving forces of sintering include surface energy reduction, diffusion mechanisms, and applied external pressures. These forces work together to eliminate porosity, enhance particle bonding, and improve material properties such as strength and durability. Key factors influencing sintering include temperature, heating rate, pressure, particle size, and composition, which collectively determine the kinetics and outcomes of the process. Understanding these driving forces and variables is essential for optimizing sintering processes to achieve desired material properties.
Key Points Explained:
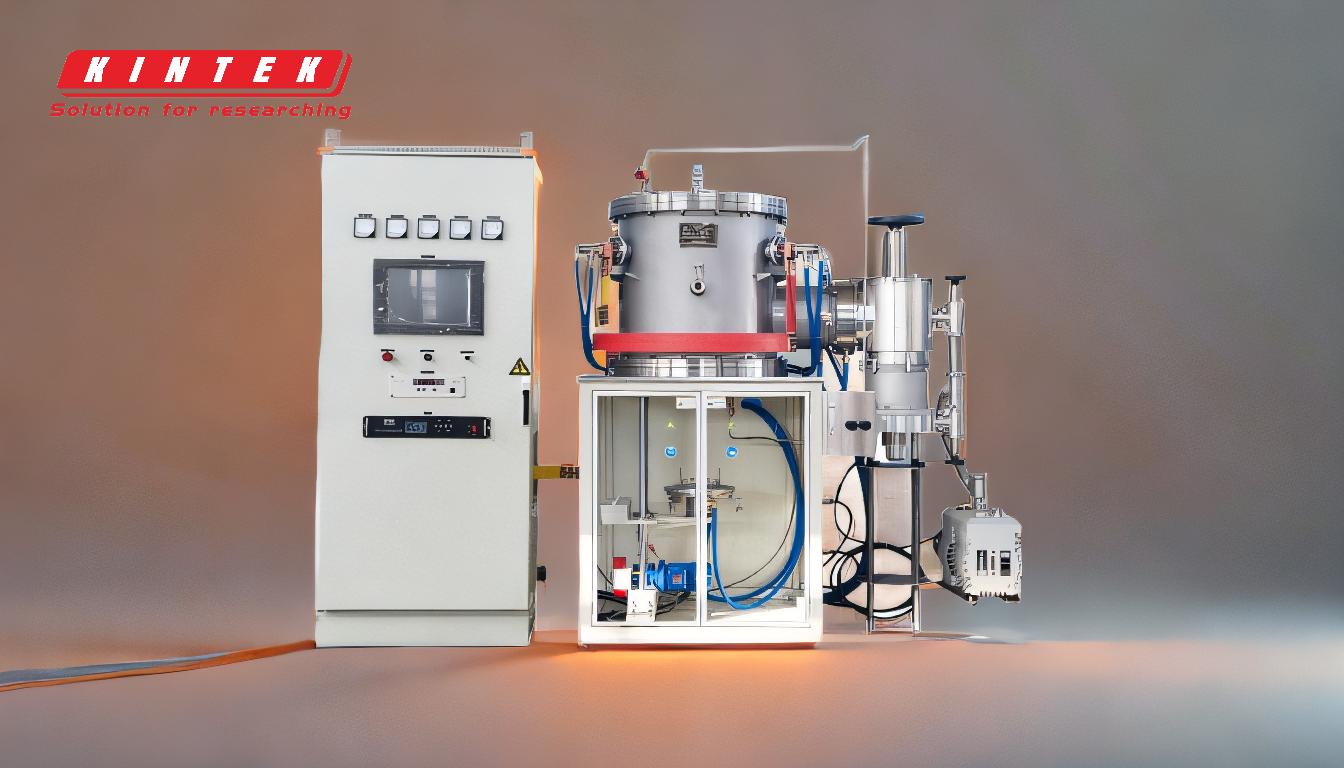
-
Surface Energy Reduction:
- Sintering is driven by the reduction of surface energy as particles bond together. Smaller particles have higher surface energy, which provides a strong driving force for sintering. As particles bond, the total surface area decreases, leading to a more stable and lower-energy state.
- This reduction in surface energy is a primary driving force behind the initial stages of sintering, where particles begin to form necks and bonds at contact points.
-
Diffusion Mechanisms:
- Sintering processes are fundamentally controlled by thermally activated solid-state diffusion mechanisms. These mechanisms include surface diffusion, grain boundary diffusion, and bulk diffusion.
- Surface Diffusion: Atoms migrate along the surface of particles, contributing to the initial stages of neck formation.
- Grain Boundary Diffusion: Atoms move along the boundaries between particles, facilitating densification and bonding.
- Bulk Diffusion: Atoms move through the lattice of the material, contributing to the overall densification process.
- These diffusion mechanisms are temperature-dependent, with higher temperatures accelerating the diffusion rates and thus the sintering process.
- Sintering processes are fundamentally controlled by thermally activated solid-state diffusion mechanisms. These mechanisms include surface diffusion, grain boundary diffusion, and bulk diffusion.
-
Applied Pressure:
- External pressure can be applied to enhance the sintering process, particularly in techniques like hot pressing or spark plasma sintering. Pressure helps in particle rearrangement and the elimination of porosity, leading to higher densification.
- The application of pressure can also reduce the sintering temperature required, making the process more energy-efficient.
-
Temperature and Heating Rate:
- Temperature is a critical factor in sintering, as it directly influences the kinetics of diffusion and the overall densification process. Higher temperatures generally increase the rate of sintering but must be carefully controlled to avoid undesirable grain growth or material degradation.
- The heating rate also plays a significant role, as it affects the uniformity of densification and the final material properties. Rapid heating can lead to uneven densification, while slower heating rates allow for more controlled and uniform sintering.
-
Particle Size and Composition:
- Smaller particles have a higher surface area-to-volume ratio, which enhances the driving force for sintering due to increased surface energy. This results in faster sintering kinetics and better densification.
- The composition of the powder particles also affects sintering behavior. Homogeneous compositions promote uniform sintering, while heterogeneous compositions may lead to uneven densification and the formation of defects.
-
Atmosphere and Cooling Rate:
- The sintering atmosphere (e.g., air, vacuum, or inert gases like argon/nitrogen) can influence the sintering process by affecting oxidation, reduction, or other chemical reactions at the particle surfaces.
- The cooling rate after sintering can impact the final microstructure and properties of the material. Controlled cooling can help in achieving desired mechanical properties, such as tensile strength, bending fatigue strength, and impact energy.
In summary, the driving forces of sintering are multifaceted, involving surface energy reduction, diffusion mechanisms, and external pressures. These forces are influenced by various factors such as temperature, heating rate, pressure, particle size, composition, atmosphere, and cooling rate. Understanding and optimizing these variables are crucial for achieving the desired material properties and performance in sintered products.
Summary Table:
Driving Forces | Key Mechanisms | Influencing Factors |
---|---|---|
Surface Energy Reduction | Bonding of particles to reduce surface energy; smaller particles enhance sintering | Particle size, composition |
Diffusion Mechanisms | Surface, grain boundary, and bulk diffusion; temperature-dependent | Temperature, heating rate |
Applied Pressure | Enhances densification; reduces sintering temperature | Pressure, sintering technique (e.g., hot pressing, spark plasma sintering) |
Temperature & Heating Rate | Controls diffusion kinetics; higher temperatures accelerate sintering | Temperature, heating rate |
Particle Size & Composition | Smaller particles increase surface energy; homogeneous compositions aid sintering | Particle size, composition |
Atmosphere & Cooling Rate | Influences oxidation/reduction; controlled cooling improves mechanical properties | Sintering atmosphere (air, vacuum, inert gases), cooling rate |
Optimize your sintering process for superior material properties—contact our experts today!