Thin film growth is a complex process influenced by a variety of factors that can be categorized into three major steps: creation of deposition species, transportation of target material, and growth on the substrate. Each step involves specific parameters that can significantly affect the quality, uniformity, and functionality of the thin film. Understanding these factors is crucial for optimizing the thin film deposition process, whether for solar cells, electronic devices, or other applications.
Key Points Explained:
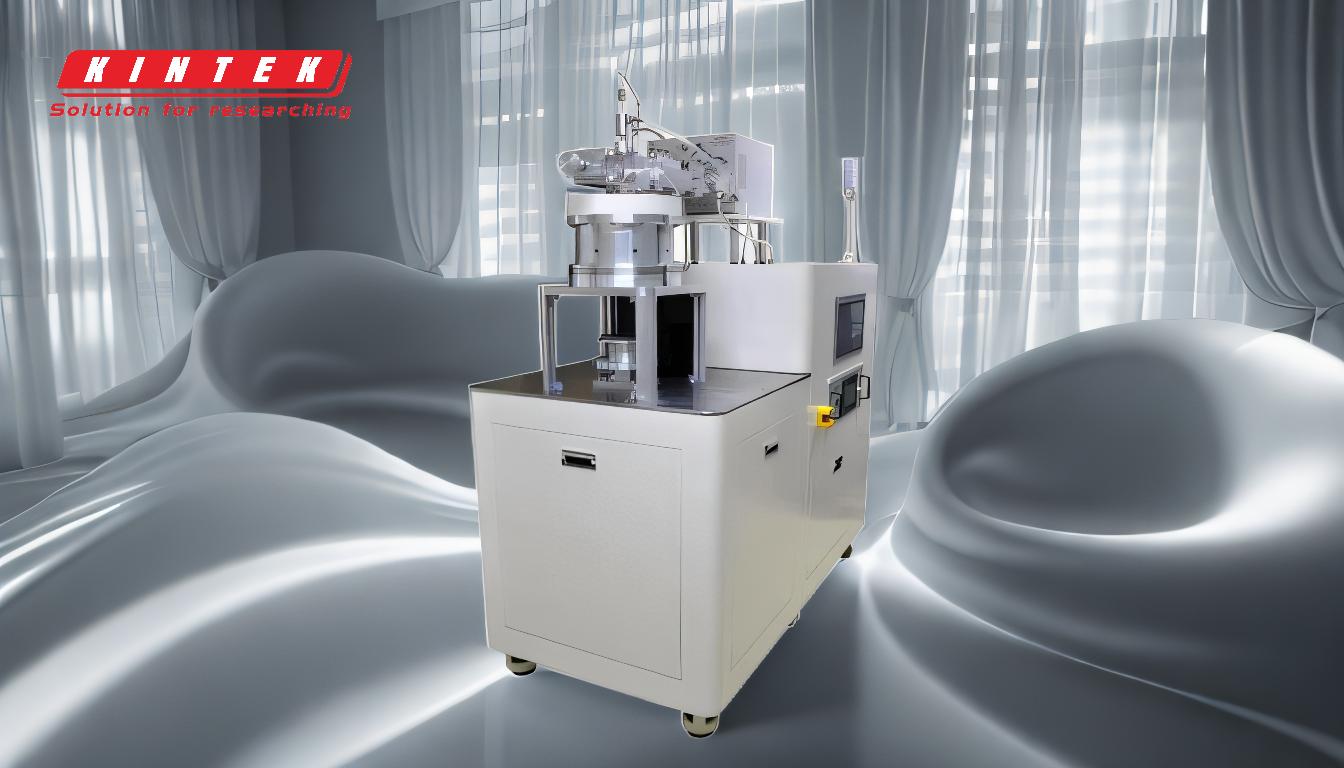
-
Creation of Deposition Species:
- Substrate Preparation: The substrate must be clean and free of contaminants to ensure proper adhesion and growth of the thin film. Surface treatments such as cleaning, etching, or applying adhesion layers can significantly impact the film's quality.
- Target Material: The composition, purity, and physical properties of the target material are critical. Impurities or inconsistencies in the target material can lead to defects in the thin film.
-
Transportation of Target Material:
- Deposition Technique: The method used to transport the target material to the substrate (e.g., sputtering, chemical vapor deposition, or physical vapor deposition) plays a significant role. Each technique has its own set of parameters, such as pressure, temperature, and energy levels, which must be carefully controlled.
- Energy Levels: The energy of the particles being deposited can range from tens to thousands of electron volts. Higher energy levels can lead to better adhesion and denser films but may also cause damage to the substrate or film if not properly controlled.
-
Growth on the Substrate:
- Nucleation and Growth: The initial stages of film growth involve nucleation, where small clusters of atoms form on the substrate. The rate and uniformity of nucleation are influenced by factors such as substrate temperature, surface energy, and the presence of nucleation sites.
- Surface Diffusion: Once nucleation occurs, surface diffusion allows adatoms to move across the substrate surface, leading to the growth of the film. The rate of surface diffusion is influenced by temperature and the nature of the substrate surface.
- Adsorption and Desorption: These processes involve the attachment and detachment of atoms or molecules to and from the substrate surface. Proper control of these processes is essential for achieving a uniform and defect-free thin film.
-
Thickness Control:
- Duration of Deposition: The time the substrate is exposed to the deposition process directly affects the thickness of the film. Longer deposition times result in thicker films, but this must be balanced against the risk of introducing defects or stresses in the film.
- Mass of Materials: The mass of the target material and the energy of the particles also influence the thickness. Heavier particles or higher energy levels can lead to faster deposition rates.
-
Layer Structure in Thin Film Solar Cells:
- Substrate: The choice of substrate (hard or flexible) affects the mechanical and thermal properties of the thin film.
- Transparent Conductive Oxide (TCO) Layer: This layer is crucial for allowing light to pass through while providing electrical conductivity.
- Semiconductor Layers: The n-type and p-type semiconductor layers are responsible for the photovoltaic effect, converting light into electrical energy.
- Metal Contact and Absorbent Layer: These layers are essential for collecting and conducting the generated electrical current.
By carefully controlling these factors, it is possible to optimize the thin film growth process, resulting in high-quality films with desired properties for specific applications.
Summary Table:
Step | Key Factors |
---|---|
Creation of Deposition Species | - Substrate preparation (cleaning, etching, adhesion layers) |
- Target material (composition, purity, physical properties) | |
Transportation of Target Material | - Deposition technique (sputtering, CVD, PVD) |
- Energy levels (particle energy for adhesion and density) | |
Growth on the Substrate | - Nucleation and growth (temperature, surface energy, nucleation sites) |
- Surface diffusion (temperature, substrate nature) | |
- Adsorption and desorption (control for uniformity and defect-free films) | |
Thickness Control | - Duration of deposition (time exposure affects thickness) |
- Mass of materials (heavier particles or higher energy levels) | |
Layer Structure (Solar Cells) | - Substrate (hard or flexible) |
- TCO layer (transparency and conductivity) | |
- Semiconductor layers (n-type, p-type for photovoltaic effect) | |
- Metal contact and absorbent layer (current collection and conduction) |
Ready to optimize your thin film growth process? Contact our experts today for tailored solutions!