Physical Vapor Deposition (PVD) is a versatile and widely used thin-film coating technique that involves four key processes: evaporation, transportation, reaction, and deposition. These processes work together to create high-quality, durable coatings on various substrates. PVD is particularly valued for its ability to produce thin films with precise thicknesses and compositions, making it essential in industries such as electronics, optics, and aerospace. The process begins with the evaporation of a target material, followed by the transportation of vaporized atoms to the substrate, potential chemical reactions to form desired compounds, and finally, the deposition of the material onto the substrate.
Key Points Explained:
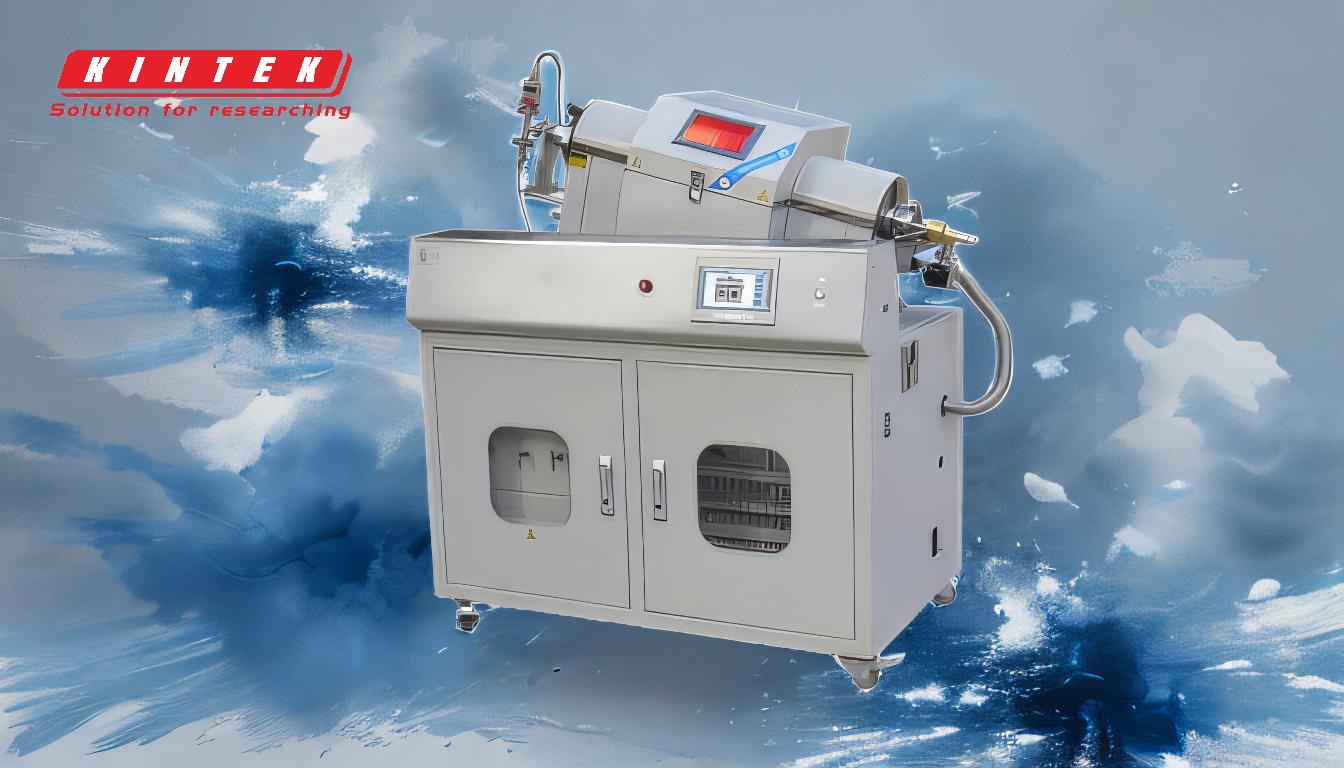
-
Evaporation
- The first step in the PVD process involves the evaporation of the target material. This is achieved by bombarding the target with a high-energy source, such as an electron beam or thermal energy, to dislodge atoms from the material.
- The target material can be a metal, alloy, or compound, and the energy source ensures that the atoms are released into the vapor phase.
- This step is critical because it determines the composition and quality of the vapor that will later form the thin film.
-
Transportation
- Once the target material is vaporized, the atoms or molecules are transported through a vacuum or low-pressure environment to the substrate.
- The transportation process is influenced by factors such as pressure, temperature, and the distance between the target and the substrate.
- Proper transportation ensures that the vaporized particles reach the substrate uniformly, which is essential for achieving consistent film thickness and quality.
-
Reaction
- During the transportation phase, the vaporized atoms may react with gases introduced into the chamber, such as oxygen or nitrogen, to form compounds like oxides or nitrides.
- This step is optional and depends on the desired properties of the final coating. For example, reactive PVD processes are used to create hard, wear-resistant coatings like titanium nitride (TiN).
- The reaction step adds versatility to the PVD process, allowing for the creation of a wide range of coating materials with tailored properties.
-
Deposition
- The final step involves the condensation of the vaporized atoms or molecules onto the substrate, forming a thin film.
- The deposition process is influenced by factors such as substrate temperature, surface energy, and the angle of incidence of the vapor stream.
- This step determines the adhesion, uniformity, and overall quality of the coating, making it a critical aspect of the PVD process.
PVD is often compared to microwave plasma chemical vapor deposition, another thin-film deposition technique. While PVD relies on physical processes like evaporation and sputtering, CVD involves chemical reactions to form coatings. Both methods have their unique advantages and are chosen based on the specific requirements of the application.
In summary, the four processes in PVD—evaporation, transportation, reaction, and deposition—work together to create high-performance thin films. Each step plays a crucial role in determining the final properties of the coating, making PVD a highly effective and widely used technique in modern manufacturing and materials science.
Summary Table:
Process | Description |
---|---|
Evaporation | Target material is vaporized using high-energy sources like electron beams. |
Transportation | Vaporized atoms are transported through a vacuum to the substrate. |
Reaction | Atoms may react with gases to form compounds like oxides or nitrides. |
Deposition | Vaporized atoms condense onto the substrate, forming a thin film. |
Learn how PVD can enhance your manufacturing process—contact our experts today!