A heat treatment furnace is a critical piece of equipment in various industrial processes, designed to alter the physical and sometimes chemical properties of materials through controlled heating and cooling. To ensure optimal performance and reliability, a heat treatment furnace must meet specific requirements. These requirements include compliance with industry standards, precise temperature control, robust construction, and advanced automation capabilities. Below, we delve into the four key requirements of a heat treatment furnace in detail.
Key Points Explained:
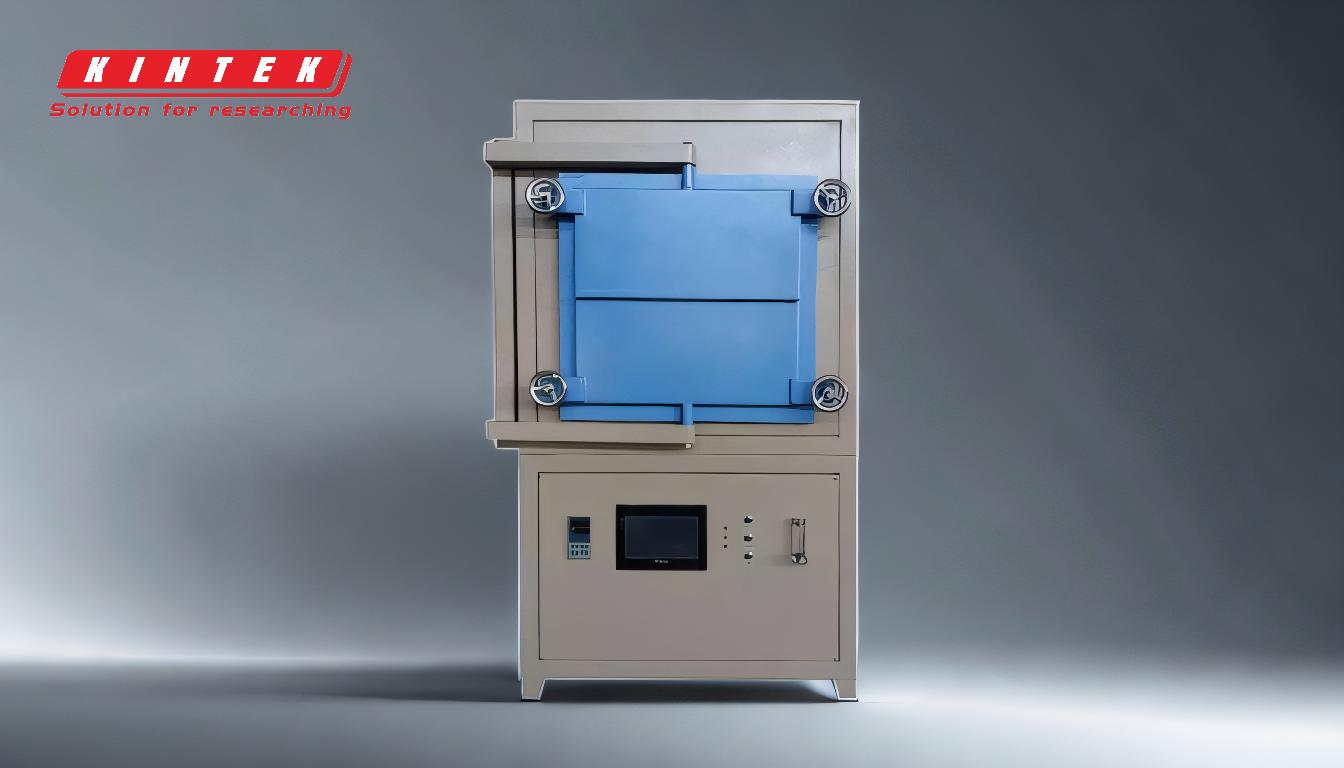
-
Compliance with Industry Standards
A heat treatment furnace must adhere to recognized industry standards such as GB, ASTM, AISI, DIN, BS, JIS, and KS. These standards ensure that the furnace is designed, manufactured, and operated in a manner that guarantees safety, reliability, and consistency in heat treatment processes. Compliance with these standards also ensures that the furnace can handle a wide range of materials and applications, making it versatile and suitable for various industries. -
Precise Temperature Control
Temperature control is one of the most critical aspects of a heat treatment furnace. The furnace must be capable of maintaining precise and uniform temperatures throughout the heating and cooling cycles. This is achieved through advanced control systems, such as thyristor-controlled modular temperature systems. These systems allow for programmable temperature settings, multi-section power limiting, and PID parameter self-tuning, ensuring that the furnace can adapt to different materials and treatment requirements. Precise temperature control is essential for achieving the desired material properties, such as hardness, toughness, and ductility. -
Robust Construction and Durability
The furnace must be constructed from high-quality materials that can withstand the extreme temperatures and harsh conditions typically encountered during heat treatment processes. The design should include features such as heat-resistant linings, durable heating elements, and sturdy structural components. Additionally, the furnace should be designed for easy maintenance and repair, with a simple structure that allows for quick access to critical components. Robust construction ensures the longevity of the furnace and minimizes downtime due to equipment failure. -
Advanced Automation and Remote Control Capabilities
Modern heat treatment furnaces are equipped with advanced automation systems that allow for full automatic control from room temperature to the set temperature. These systems often include programmable multi-section temperature profiles, real-time tracking, and history recording. Remote control capabilities enable operators to monitor and adjust the furnace settings from a distance, improving efficiency and safety. The ability to interconnect with software and computers further enhances the furnace's functionality, allowing for data analysis, output reporting, and integration with other industrial systems.
By meeting these four requirements, a heat treatment furnace can deliver consistent, high-quality results, ensuring that materials are treated to the desired specifications. These features not only enhance the performance of the furnace but also contribute to the overall efficiency and productivity of the heat treatment process.
Summary Table:
Requirement | Key Features |
---|---|
Compliance with Industry Standards | Adheres to GB, ASTM, AISI, DIN, BS, JIS, and KS standards for safety and reliability. |
Precise Temperature Control | Advanced control systems for uniform heating, PID self-tuning, and programmable settings. |
Robust Construction and Durability | Heat-resistant linings, durable heating elements, and easy maintenance design. |
Advanced Automation Capabilities | Programmable temperature profiles, remote control, and software integration. |
Ensure your heat treatment furnace meets the highest standards—contact our experts today for tailored solutions!