Furnaces used in metals vary widely depending on the specific application, temperature requirements, and industrial processes. These include sintering, melting, and high-temperature testing. Common types include rotary drum furnaces, roller hearth kilns, pusher slab kilns, and lift bottom kilns for sintering. For melting, electric arc furnaces and induction melting furnaces are prevalent. High-temperature applications often utilize tube furnaces, vacuum furnaces, box furnaces, and muffle furnaces. Additionally, continuous or pusher furnaces are favored in production environments for their efficiency, while gas, electric, and oil models are widely used across industries. Each type is designed to meet specific operational needs, ensuring temperature uniformity and process efficiency.
Key Points Explained:
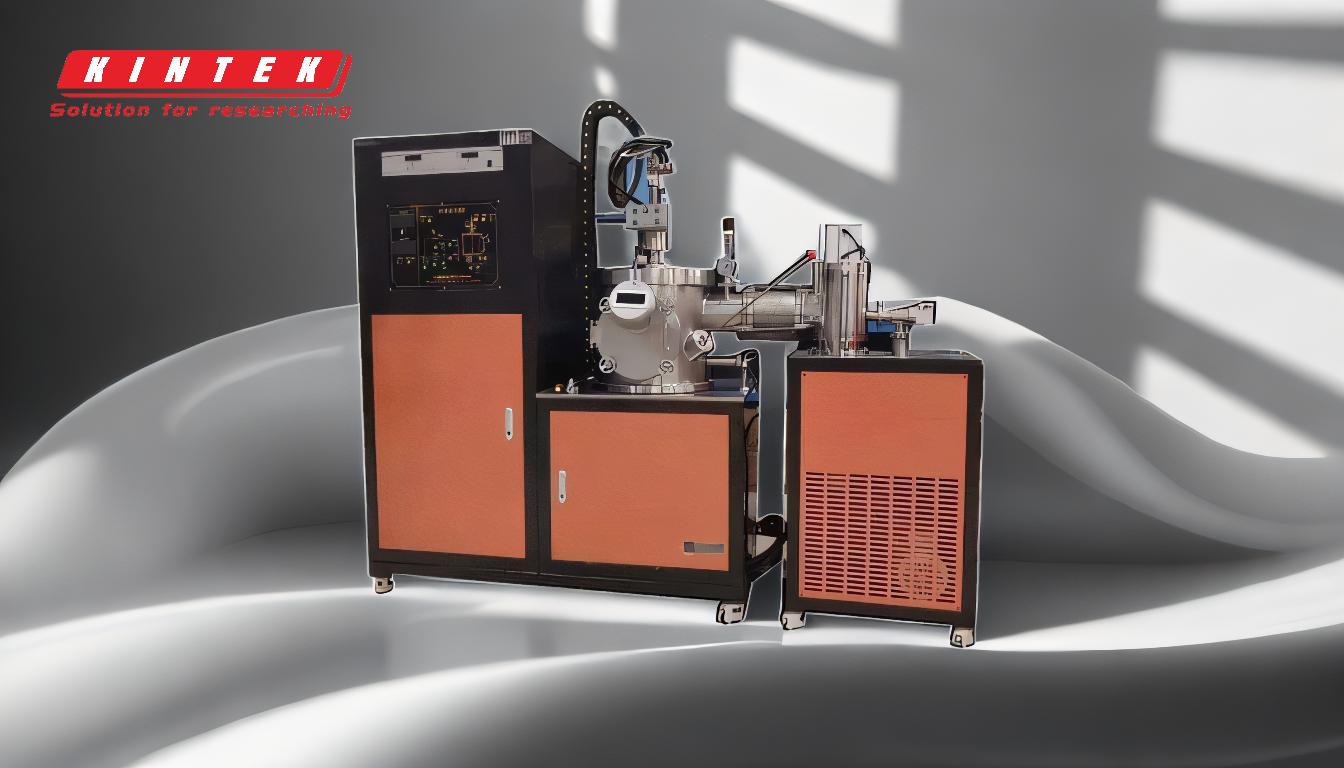
-
Sintering Furnaces:
- Rotary Drum Furnaces: Used for continuous processing of materials, ideal for uniform heating and sintering.
- Roller Hearth Kilns: Suitable for high-throughput sintering processes, often used in industrial settings.
- Pusher Slab Kilns: Designed for batch processing, these kilns are efficient for sintering large volumes of materials.
- Lift Bottom Kilns: Provide precise temperature control, making them suitable for specialized sintering applications.
-
Melting Furnaces:
- Electric Arc Furnaces: Utilize an electric arc to generate extreme heat, commonly used for melting scrap metal and producing steel.
- Induction Melting Furnaces: Use electromagnetic induction to heat and melt metals, offering precise temperature control and energy efficiency.
-
High-Temperature Furnaces:
- Tube Furnaces: Ideal for processes requiring high temperatures and controlled atmospheres, such as fusion and testing.
- Vacuum Furnaces: Used for processes that require a vacuum environment, such as sintering and heat treatment of metals.
- Box Furnaces: Versatile furnaces suitable for a wide range of high-temperature applications, including melting and sintering.
- Muffle Furnaces: Designed for processes requiring isolation of the material from combustion gases, ensuring contamination-free heating.
-
Continuous Furnaces:
- Pusher Furnaces: Common in production environments for their high throughput and efficiency in continuous processing.
- Belt Furnaces: Used for lower temperature processes but not suitable for the high end of the sintering temperature range.
-
General Industrial Furnaces:
- Gas Furnaces: Widely used for their cost-effectiveness and ability to reach high temperatures.
- Electric Furnaces: Offer precise temperature control and are environmentally friendly, commonly used in laboratories and small-scale industrial applications.
- Oil Furnaces: Provide high heat output, often used in large-scale industrial processes.
Each type of furnace is designed to meet specific operational needs, ensuring temperature uniformity, process efficiency, and material integrity. The choice of furnace depends on the specific application, temperature requirements, and production scale.
Summary Table:
Furnace Type | Key Applications | Features |
---|---|---|
Sintering Furnaces | Rotary Drum, Roller Hearth, Pusher Slab, Lift Bottom Kilns | Uniform heating, high throughput, precise temperature control |
Melting Furnaces | Electric Arc, Induction Melting Furnaces | Extreme heat, energy efficiency, precise temperature control |
High-Temperature | Tube, Vacuum, Box, Muffle Furnaces | Controlled atmospheres, contamination-free heating, high-temperature range |
Continuous Furnaces | Pusher, Belt Furnaces | High throughput, efficiency in continuous processing |
General Industrial | Gas, Electric, Oil Furnaces | Cost-effective, precise control, high heat output |
Need help selecting the right furnace for your metal processing needs? Contact our experts today for personalized advice!