Sintering design involves optimizing various parameters to achieve desired material properties. Key factors include temperature, pressure, particle size, and atmosphere, which influence densification, porosity, and mechanical properties. The choice of sintering technique depends on material characteristics and desired outcomes, such as strength, conductivity, or fatigue resistance. Additionally, furnace configuration, including temperature range, gas flow, and loading strategy, plays a critical role in ensuring efficient and effective sintering. By carefully controlling these variables, manufacturers can tailor the sintering process to meet specific product requirements, balancing performance, cost, and production efficiency.
Key Points Explained:
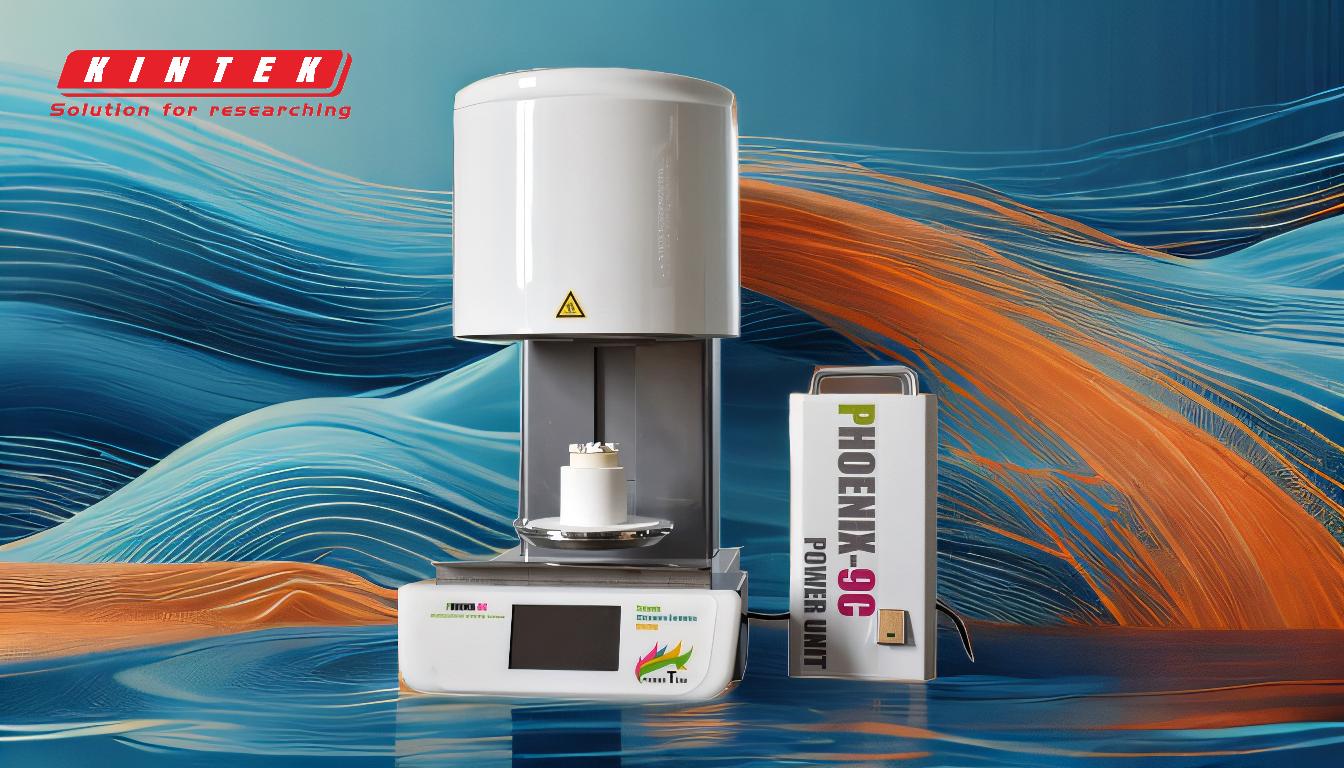
-
Sintering Parameters and Their Influence:
- Temperature: Determines sintering kinetics and material properties. Higher temperatures generally increase compaction and densification but must be balanced to avoid excessive grain growth or melting.
- Pressure: Enhances particle rearrangement and reduces porosity, leading to improved mechanical properties. Applied pressure can also reduce sintering time.
- Particle Size: Smaller particles increase the binding area, improving properties like strength and conductivity. Finer powders promote better densification but require careful control of sintering conditions.
- Atmosphere: The choice of atmosphere (e.g., air, vacuum, or inert gases like argon/nitrogen) affects oxidation, contamination, and sintering behavior. For example, inert atmospheres are often used to prevent oxidation in metal sintering.
-
Material-Specific Considerations:
- Ceramics: Pure oxide ceramics require longer sintering times and higher temperatures due to solid-state diffusion. Pressure-assisted sintering can help reduce porosity and improve densification.
- Metals and Alloys: Sintering conditions must account for melting points, alloy composition, and phase transformations. Liquid-phase sintering can enhance densification but requires precise control of the liquid phase volume.
- Powder Characteristics: The initial porosity of the green compact, particle size distribution, and composition significantly influence the final sintered product.
-
Sintering Techniques:
- Pressureless Sintering: Suitable for materials that densify well without external pressure. It relies on temperature and atmosphere control.
- Pressure-Assisted Sintering: Includes techniques like hot pressing and spark plasma sintering (SPS), which apply pressure to enhance densification and reduce sintering time.
- Liquid-Phase Sintering: Involves the formation of a liquid phase to aid densification. It is commonly used for materials with low melting points or complex compositions.
- Field-Assisted Sintering: Techniques like SPS use electrical currents to generate heat and pressure simultaneously, enabling rapid sintering at lower temperatures.
-
Furnace Design and Operation:
- Temperature Range: The furnace must operate within the required temperature range for the material being sintered. High-temperature sintering can enhance mechanical properties but increases operating costs.
- Gas Flow and Atmosphere Control: Uniform gas flow distribution ensures consistent sintering conditions and prevents contamination. The choice of atmosphere depends on material requirements.
- Loading Strategy: Proper loading of parts ensures uniform heating and minimizes thermal gradients, which can lead to warping or uneven densification.
- Efficiency and Cost: Factors like the mass of the hot zone, peak power levels, and cooling rates impact energy consumption and operating costs.
-
Performance Optimization:
- Densification: Achieving high density is critical for mechanical strength and durability. This requires careful control of temperature, pressure, and sintering time.
- Porosity Control: Initial porosity of the green compact and sintering conditions determine the final porosity. Lower porosity improves mechanical properties but may require longer sintering times or higher pressures.
- Grain Size Management: Controlling grain growth during sintering is essential for maintaining material properties. Excessive grain growth can reduce strength and toughness.
-
Practical Considerations for Purchasers:
- Material Selection: Choose powders with appropriate particle size, composition, and purity for the desired application.
- Equipment Compatibility: Ensure the sintering furnace and accessories (e.g., dies, molds) are compatible with the material and process requirements.
- Cost-Benefit Analysis: Balance the benefits of advanced sintering techniques (e.g., SPS) against their higher costs and complexity.
- Quality Control: Implement robust quality control measures to monitor sintering parameters and ensure consistent product performance.
By understanding and applying these guidelines, manufacturers and purchasers can optimize sintering processes to achieve high-performance materials tailored to specific applications.
Summary Table:
Key Sintering Parameters | Influence |
---|---|
Temperature | Determines sintering kinetics and material properties. |
Pressure | Enhances particle rearrangement and reduces porosity. |
Particle Size | Smaller particles improve strength and conductivity. |
Atmosphere | Affects oxidation, contamination, and sintering behavior. |
Sintering Techniques | Pressureless, pressure-assisted, liquid-phase, and field-assisted sintering. |
Furnace Design | Temperature range, gas flow, and loading strategy are critical for efficiency. |
Performance Optimization | Focus on densification, porosity control, and grain size management. |
Optimize your sintering process today—contact our experts for tailored solutions!