Brazing, a process used to join metals using a filler metal, poses several health risks primarily due to exposure to hazardous fumes, gases, and particulates. These risks include respiratory issues, skin and eye irritation, and potential long-term effects from exposure to toxic substances like cadmium, zinc, and lead. Proper ventilation, personal protective equipment (PPE), and adherence to safety protocols are essential to mitigate these risks. Understanding the specific hazards associated with brazing materials and processes is crucial for ensuring workplace safety and minimizing health impacts.
Key Points Explained:
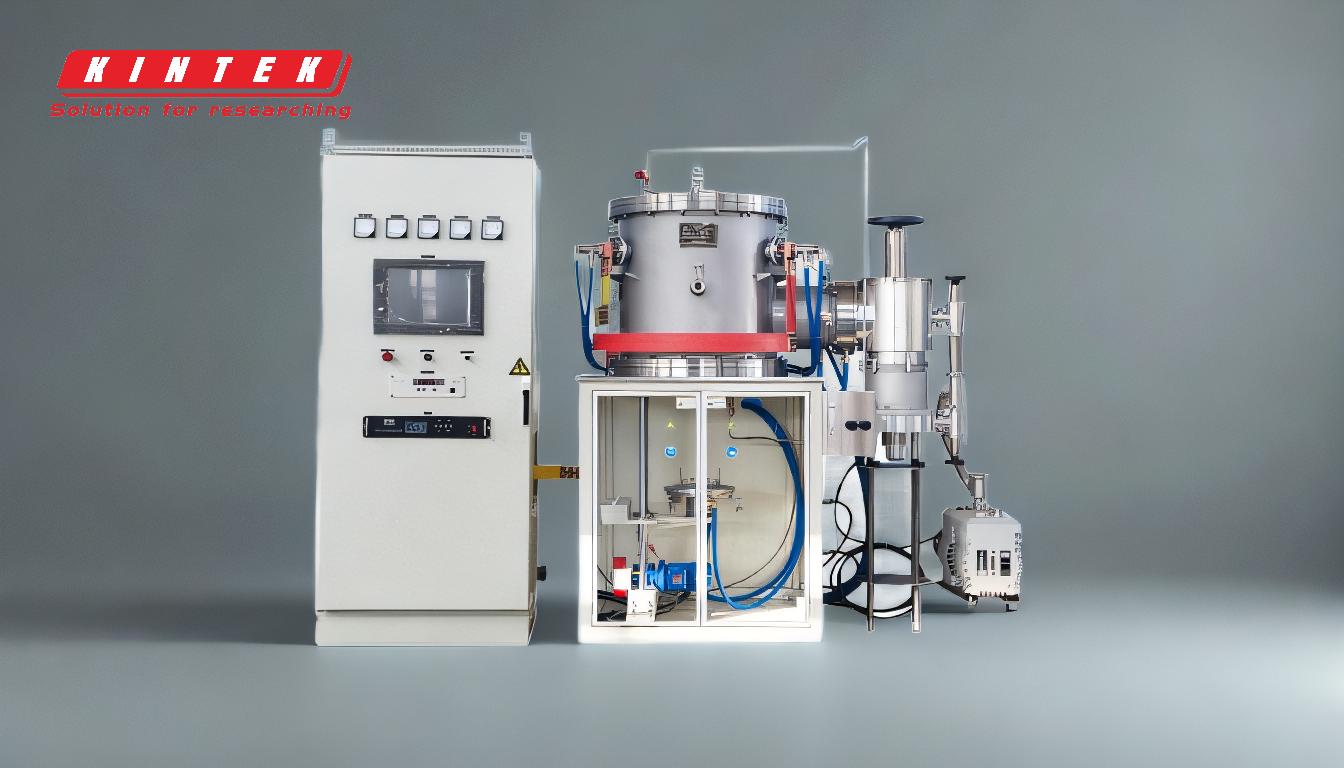
-
Exposure to Harmful Fumes and Gases
- During brazing, the heating of filler metals and base materials can release toxic fumes and gases, such as zinc oxide, cadmium oxide, and lead oxide.
- Inhalation of these fumes can lead to acute respiratory conditions like metal fume fever, characterized by flu-like symptoms such as fever, chills, and shortness of breath.
- Chronic exposure may result in more severe respiratory diseases, including lung damage or cancer, depending on the materials used.
-
Skin and Eye Irritation
- Direct contact with hot metals, fluxes, or filler materials can cause burns or skin irritation.
- Splashes of molten metal or flux can lead to eye injuries if proper eye protection is not worn.
- Fluxes, often containing corrosive chemicals, can cause dermatitis or chemical burns upon prolonged exposure.
-
Cadmium Exposure Risks
- Cadmium, a common component in some brazing alloys, is highly toxic and carcinogenic.
- Inhalation of cadmium fumes can cause severe lung and kidney damage, and long-term exposure is linked to lung cancer.
- Strict control measures, such as using cadmium-free alloys or ensuring adequate ventilation, are critical to reducing these risks.
-
Lead Exposure Concerns
- Lead, sometimes present in brazing alloys, poses significant health risks, particularly to the nervous system and kidneys.
- Even low-level exposure over time can lead to cognitive impairments, especially in children and pregnant women.
- Proper handling and disposal of lead-containing materials are essential to prevent contamination and exposure.
-
Importance of Ventilation and PPE
- Adequate ventilation systems, such as local exhaust ventilation (LEV), are necessary to remove fumes and gases from the workspace.
- Respiratory protection, such as NIOSH-approved respirators, should be used when ventilation is insufficient.
- Personal protective equipment, including gloves, safety goggles, and flame-resistant clothing, is vital to protect against burns and chemical exposure.
-
Flux-Related Hazards
- Fluxes used in brazing to prevent oxidation can release harmful fumes when heated.
- These fumes may contain fluorides, borates, or chlorides, which can irritate the respiratory tract and eyes.
- Proper storage, handling, and disposal of fluxes are necessary to minimize exposure risks.
-
Fire and Explosion Risks
- The use of open flames or high temperatures in brazing increases the risk of fire or explosions, especially in the presence of flammable materials.
- Ensuring a clean workspace, free of combustible materials, and having fire extinguishers readily available are essential safety measures.
-
Long-Term Health Monitoring
- Workers regularly involved in brazing should undergo regular health check-ups to monitor for signs of respiratory or other health issues.
- Employers should provide training on recognizing symptoms of exposure and implementing preventive measures.
By understanding these risks and implementing appropriate safety measures, the health hazards associated with brazing can be significantly reduced. Proper training, use of PPE, and adherence to safety protocols are essential for protecting workers in brazing operations.
Summary Table:
Hazard | Key Risks | Prevention Measures |
---|---|---|
Toxic Fumes & Gases | Respiratory issues, metal fume fever, lung damage, cancer | Use NIOSH-approved respirators, ensure proper ventilation (LEV) |
Skin & Eye Irritation | Burns, dermatitis, chemical burns, eye injuries | Wear gloves, safety goggles, and flame-resistant clothing |
Cadmium Exposure | Severe lung/kidney damage, lung cancer | Use cadmium-free alloys, ensure adequate ventilation |
Lead Exposure | Nervous system damage, cognitive impairments, kidney issues | Proper handling, disposal, and use of lead-free materials |
Flux-Related Hazards | Respiratory and eye irritation from fluorides, borates, chlorides | Proper storage, handling, and disposal of fluxes |
Fire & Explosion Risks | Fire or explosions from open flames and flammable materials | Keep workspace clean, remove combustibles, have fire extinguishers ready |
Long-Term Health Risks | Chronic respiratory diseases, cancer, kidney damage | Regular health check-ups, training on exposure symptoms and preventive measures |
Ensure your workplace is safe from brazing hazards—contact our safety experts today for guidance!