Heat treatment processes for steel are essential for modifying its mechanical properties to suit specific applications. These processes involve controlled heating and cooling to achieve desired characteristics such as hardness, toughness, ductility, and strength. The most common heat treatment processes include annealing, quenching, tempering, normalizing, case hardening, and martensitic transformation. Each process serves a unique purpose, such as softening the metal, increasing hardness, or improving durability. By understanding these processes, manufacturers can tailor steel to meet precise requirements for various industrial applications.
Key Points Explained:
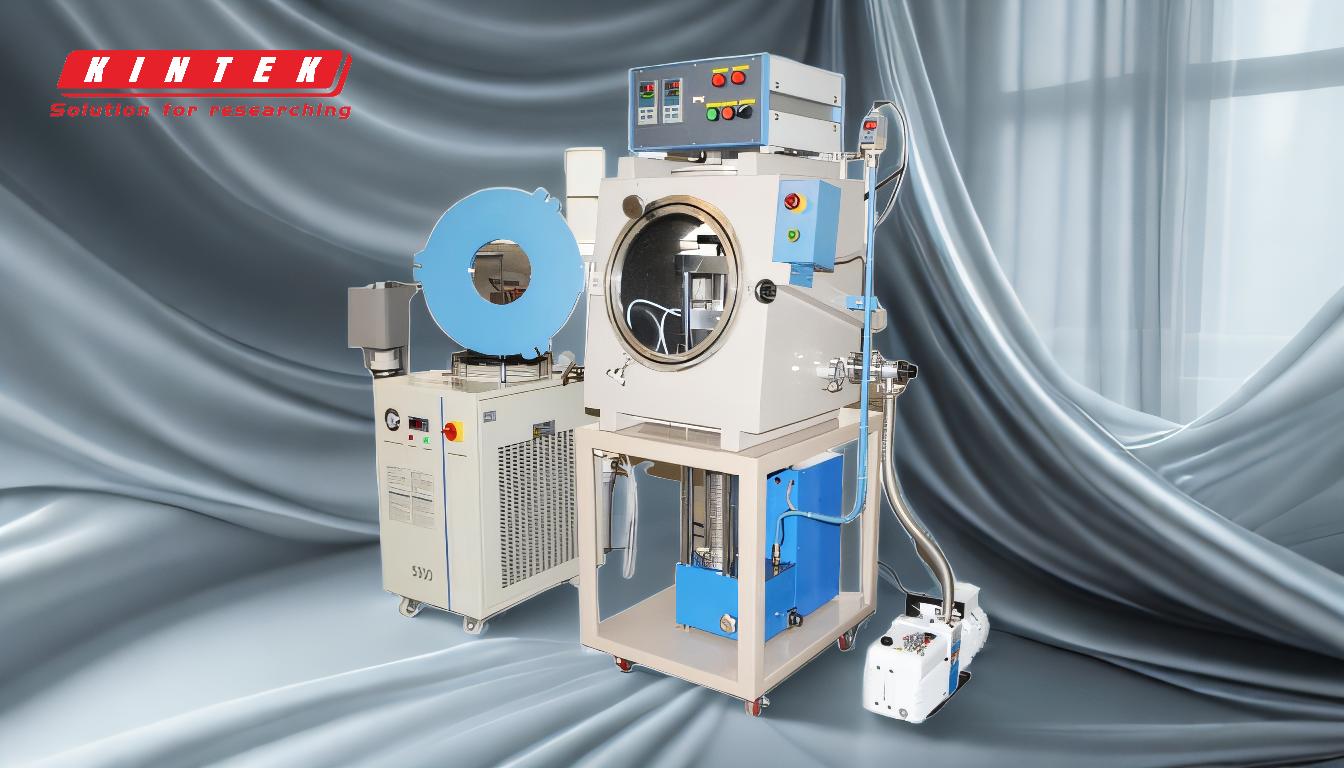
-
Annealing:
- Purpose: Annealing is used to soften steel, improve machinability, and reduce internal stresses. It involves heating the steel to a specific temperature and then slowly cooling it.
- Process: The steel is heated to a temperature above its recrystallization point but below its melting point, held at that temperature for a period, and then cooled in the furnace or air.
- Outcome: This process results in a more ductile and less brittle material, making it easier to work with in subsequent manufacturing steps.
-
Quenching:
- Purpose: Quenching is used to increase the hardness and strength of steel. It involves rapid cooling from a high temperature.
- Process: The steel is heated to a temperature above its critical point and then rapidly cooled, usually in water, oil, or air.
- Outcome: This rapid cooling transforms the microstructure of the steel, typically resulting in a harder but more brittle material.
-
Tempering:
- Purpose: Tempering is used to reduce the brittleness induced by quenching while maintaining the hardness and strength.
- Process: The steel is reheated to a temperature below its critical point after quenching and then cooled at a controlled rate.
- Outcome: This process improves toughness and ductility, making the steel less prone to cracking under stress.
-
Normalizing:
- Purpose: Normalizing is used to refine the grain structure of the steel, improve machinability, and achieve a more uniform microstructure.
- Process: The steel is heated to a temperature above its critical point and then cooled in still air.
- Outcome: This results in a more uniform and fine-grained structure, enhancing the mechanical properties of the steel.
-
Case Hardening:
- Purpose: Case hardening is used to increase the surface hardness of the steel while maintaining a tough core.
- Process: The steel is exposed to a carbon-rich environment at high temperatures, allowing carbon to diffuse into the surface layer. This is often followed by quenching.
- Outcome: The surface becomes hard and wear-resistant, while the core remains tough and ductile.
-
Martensitic Transformation:
- Purpose: This process is used to achieve high hardness and strength through the formation of martensite, a hard and brittle phase of steel.
- Process: The steel is heated to a high temperature and then rapidly cooled, typically through quenching, to form martensite.
- Outcome: The resulting material is very hard and strong but may require tempering to reduce brittleness.
-
Carburizing:
- Purpose: Carburizing is used to increase the carbon content on the surface of low-carbon steel, enhancing surface hardness.
- Process: The steel is heated in a carbon-rich environment, allowing carbon atoms to diffuse into the surface.
- Outcome: The surface becomes harder and more wear-resistant, while the core remains soft and tough.
-
Precipitation Hardening:
- Purpose: This process is used to increase the strength of certain alloys by forming fine particles within the metal matrix.
- Process: The steel is heated to a temperature that allows the formation of precipitates and then cooled to room temperature.
- Outcome: The precipitates impede dislocation movement, increasing the strength and hardness of the steel.
By understanding these heat treatment processes, manufacturers can select the appropriate method to achieve the desired properties in steel for specific applications. Each process offers unique benefits and can be tailored to meet the exact requirements of the final product.
Summary Table:
Process | Purpose | Key Steps | Outcome |
---|---|---|---|
Annealing | Soften steel, improve machinability, reduce internal stresses | Heat above recrystallization, hold, slow cool in furnace/air | More ductile, less brittle material |
Quenching | Increase hardness and strength | Heat above critical point, rapid cool in water/oil/air | Harder but more brittle material |
Tempering | Reduce brittleness, maintain hardness and strength | Reheat below critical point after quenching, controlled cooling | Improved toughness and ductility |
Normalizing | Refine grain structure, improve machinability | Heat above critical point, cool in still air | Uniform, fine-grained structure |
Case Hardening | Increase surface hardness, maintain tough core | Expose to carbon-rich environment, heat, followed by quenching | Hard, wear-resistant surface with tough core |
Martensitic Transform | Achieve high hardness and strength | Heat to high temperature, rapid cool (quenching) | Very hard and strong material, may require tempering |
Carburizing | Increase surface carbon content, enhance hardness | Heat in carbon-rich environment, allow carbon diffusion | Harder, wear-resistant surface with soft core |
Precipitation Hardening | Increase strength of alloys via fine particle formation | Heat to form precipitates, cool to room temperature | Increased strength and hardness |
Optimize your steel properties with the right heat treatment—contact our experts today for tailored solutions!