Inert gases play a crucial role in heat treatment furnaces, primarily to prevent oxidation, decarburization, and other unwanted chemical reactions during the heating process. The most commonly used inert gases are argon (Ar), helium (He), and nitrogen (N2). These gases are often used individually or in combinations like Ar/He, Ar/He/N2, and N2/He, depending on the specific requirements of the heat treatment process. They are particularly effective for treating non-ferrous metals such as copper, brass, and aluminum. Additionally, inert gases like nitrogen and argon are used to create controlled atmospheres that remove unwanted materials, ensuring the quality and safety of the heat-treated components.
Key Points Explained:
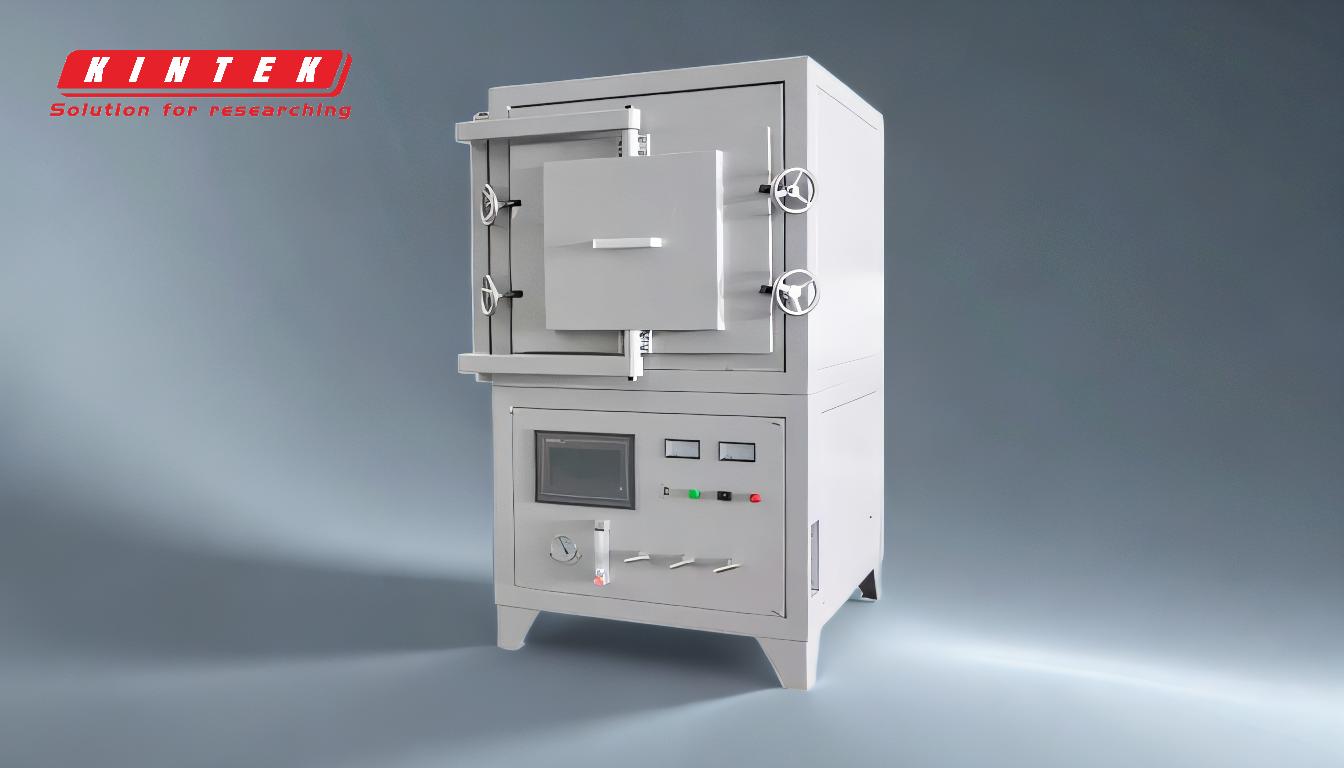
-
Common Inert Gases in Heat Treatment Furnaces:
- Argon (Ar): Argon is widely used due to its inert nature, which prevents oxidation and other chemical reactions. It is particularly effective in improving annealing processes and is often used in combination with other gases like helium and nitrogen.
- Helium (He): Helium is another inert gas used in heat treatment. It has high thermal conductivity, which can enhance heat transfer within the furnace. It is often used in combination with argon to optimize the heat treatment process.
- Nitrogen (N2): Nitrogen is commonly used due to its availability and cost-effectiveness. It is effective in creating a controlled atmosphere that prevents oxidation and decarburization. Nitrogen is also used in augmenting the annealing process.
-
Combinations of Inert Gases:
- Ar/He: This combination leverages the inert properties of argon and the high thermal conductivity of helium, making it suitable for processes requiring precise temperature control.
- Ar/He/N2: This combination provides a balanced atmosphere that prevents oxidation while enhancing heat transfer and cost-effectiveness.
- N2/He: This mix is often used for its cost-effectiveness and ability to maintain a stable, inert environment.
-
Applications in Non-Ferrous Metals:
- Inert gases are particularly effective in heat treating non-ferrous metals like copper, brass, and aluminum. These metals are prone to oxidation and other chemical reactions at high temperatures, and inert gases help maintain their integrity and quality during the heat treatment process.
-
Role in Controlled Atmospheres:
- Inert gases like nitrogen and argon are used to create controlled atmospheres within the furnace. This involves purging the furnace of unwanted materials such as oxygen, water, and flammables, which can degrade the quality of the heat-treated components.
- This controlled atmosphere not only improves the quality of the heat treatment but also acts as a safety measure by reducing the risk of fire or explosion.
-
Preventing Oxidation and Decarburization:
- One of the primary functions of inert gases is to prevent oxidation and decarburization, which can degrade the quality of the metal being treated. By maintaining an inert atmosphere, these gases ensure that the metal retains its desired properties and finishes.
-
Safety Considerations:
- Using inert gases like nitrogen and argon helps in purging the furnace of flammable gases and oxygen, thereby reducing the risk of fire or explosion. This makes the heat treatment process safer and more reliable.
In summary, inert gases such as argon, helium, and nitrogen are essential in heat treatment furnaces for maintaining a controlled atmosphere, preventing oxidation and decarburization, and ensuring the safety and quality of the heat-treated components. Their use is particularly critical when dealing with non-ferrous metals, where maintaining the integrity of the metal is paramount.
Summary Table:
Inert Gas | Key Properties | Common Uses |
---|---|---|
Argon (Ar) | Inert, prevents oxidation | Annealing, combination with He/N2 |
Helium (He) | High thermal conductivity | Heat transfer optimization, used with Ar |
Nitrogen (N2) | Cost-effective, prevents oxidation | Controlled atmospheres, annealing |
Combinations | Benefits | Applications |
Ar/He | Precise temperature control | Heat treatment of non-ferrous metals |
Ar/He/N2 | Balanced atmosphere, cost-effective | Oxidation prevention, heat transfer |
N2/He | Stable, inert environment | Cost-effective heat treatment |
Learn how inert gases can optimize your heat treatment process—contact our experts today!