Electrochemical deposition (ECD) is a widely used technique for coating surfaces with thin films of metals or alloys. While it offers advantages such as cost-effectiveness, scalability, and the ability to deposit a wide range of materials, it also has several limitations. These include challenges related to uniformity, adhesion, material compatibility, environmental concerns, and process control. Understanding these limitations is crucial for optimizing the process and selecting appropriate applications.
Key Points Explained:
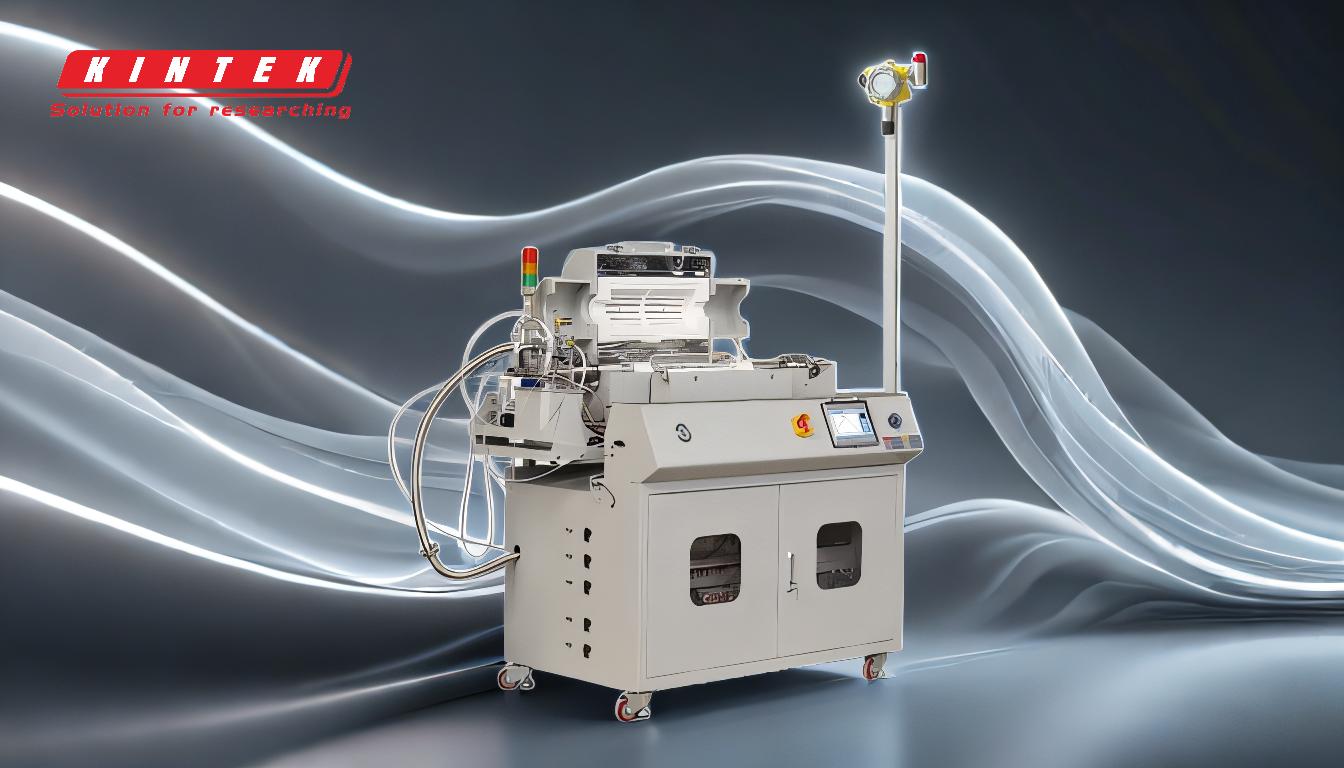
-
Non-Uniform Deposition:
- Explanation: One of the primary limitations of electrochemical deposition is the difficulty in achieving uniform thickness across complex geometries or large surfaces. This is due to variations in current density, which can lead to thicker deposits in areas with higher current density and thinner deposits in areas with lower current density.
- Implications: Non-uniform deposition can result in inconsistent material properties, such as varying electrical conductivity or mechanical strength, which can be problematic in applications requiring precise tolerances.
-
Adhesion Issues:
- Explanation: Poor adhesion between the deposited layer and the substrate can occur if the substrate is not properly cleaned or if the deposition conditions are not optimized. Contaminants, oxides, or surface roughness can all negatively impact adhesion.
- Implications: Weak adhesion can lead to delamination, peeling, or flaking of the deposited layer, compromising the integrity and functionality of the coating.
-
Material Compatibility:
- Explanation: Not all materials can be easily deposited using electrochemical methods. Some materials may require complex electrolytes or specific conditions that are difficult to maintain. Additionally, the choice of substrate material can limit the types of coatings that can be applied.
- Implications: This limitation restricts the versatility of electrochemical deposition and may necessitate the use of alternative coating techniques for certain materials.
-
Environmental and Safety Concerns:
- Explanation: The electrolytes used in electrochemical deposition often contain toxic or hazardous chemicals, such as heavy metals or cyanides. The disposal of waste electrolytes and the management of by-products can pose significant environmental and safety challenges.
- Implications: Compliance with environmental regulations and the implementation of safety measures can increase the cost and complexity of the deposition process.
-
Process Control and Reproducibility:
- Explanation: Achieving consistent results with electrochemical deposition requires precise control over numerous parameters, including current density, temperature, pH, and electrolyte composition. Small variations in these parameters can lead to significant differences in the quality of the deposited layer.
- Implications: The need for stringent process control can make electrochemical deposition more complex and less reproducible, particularly in large-scale or high-throughput applications.
-
Limitations in Coating Thickness:
- Explanation: Electrochemical deposition is generally more suitable for thin films rather than thick coatings. As the thickness of the deposit increases, issues such as internal stress, cracking, and porosity become more pronounced.
- Implications: This limitation makes electrochemical deposition less suitable for applications requiring thick, robust coatings, such as wear-resistant or corrosion-resistant layers.
-
Surface Preparation Requirements:
- Explanation: The success of electrochemical deposition is highly dependent on the quality of surface preparation. Any contamination, oxidation, or surface defects can negatively impact the deposition process and the quality of the final coating.
- Implications: Extensive surface preparation, including cleaning, polishing, and activation, is often required, which can add time and cost to the overall process.
-
Limited to Conductive Substrates:
- Explanation: Electrochemical deposition requires the substrate to be conductive, as the process relies on the flow of electrical current. Non-conductive materials, such as plastics or ceramics, cannot be directly coated using this method without additional steps, such as the application of a conductive layer.
- Implications: This limitation restricts the range of materials that can be coated using electrochemical deposition and may require additional processing steps for non-conductive substrates.
-
Stress and Cracking in Deposits:
- Explanation: Internal stress can develop in the deposited layer due to factors such as differences in thermal expansion coefficients between the substrate and the coating, or due to the deposition process itself. This stress can lead to cracking or delamination of the coating.
- Implications: Stress and cracking can compromise the mechanical integrity and durability of the coating, making it unsuitable for applications requiring high reliability.
-
Limited to Specific Alloys and Compositions:
- Explanation: While electrochemical deposition can be used to deposit a wide range of metals, creating specific alloys or composite materials can be challenging. The composition of the deposited material is often limited by the availability of suitable electrolytes and the ability to control the deposition process.
- Implications: This limitation can restrict the use of electrochemical deposition in applications requiring specific material properties, such as tailored hardness, corrosion resistance, or magnetic properties.
In conclusion, while electrochemical deposition is a versatile and widely used technique, it is not without its limitations. Understanding these limitations is essential for selecting the appropriate coating method and optimizing the deposition process for specific applications.
Summary Table:
Limitation | Explanation | Implications |
---|---|---|
Non-Uniform Deposition | Variations in current density lead to uneven coating thickness. | Inconsistent material properties, affecting precision applications. |
Adhesion Issues | Poor adhesion due to contaminants or improper surface preparation. | Delamination, peeling, or flaking of the coating. |
Material Compatibility | Limited by substrate and electrolyte requirements. | Restricts versatility and may require alternative methods. |
Environmental and Safety Concerns | Use of toxic chemicals and waste management challenges. | Increases cost and complexity of the process. |
Process Control and Reproducibility | Requires precise control of multiple parameters. | Makes the process complex and less reproducible. |
Limitations in Coating Thickness | More suitable for thin films; thick coatings face stress and porosity issues. | Less ideal for applications needing robust, thick coatings. |
Surface Preparation Requirements | Extensive cleaning, polishing, and activation needed. | Adds time and cost to the process. |
Limited to Conductive Substrates | Non-conductive materials require additional steps. | Restricts range of materials that can be coated. |
Stress and Cracking in Deposits | Internal stress leads to cracking or delamination. | Compromises mechanical integrity and durability. |
Limited to Specific Alloys | Difficulty in depositing specific alloys or composites. | Restricts use in applications requiring tailored material properties. |
Need help optimizing your electrochemical deposition process? Contact our experts today for tailored solutions!