Fluidized bed reactors (FBRs) are widely used in industries such as petroleum, chemical, and biomass processing due to their advantages like uniform particle mixing, temperature gradients, and continuous operation. However, they also come with significant limitations that can impact their efficiency, scalability, and operational costs. Key limitations include increased reactor vessel size, higher pumping requirements and pressure drop, particle entrainment, erosion of internal components, and challenges in scaling up heat transfer. Additionally, there is a lack of comprehensive understanding of material behavior in FBRs, which can lead to unpredictable operational issues. These limitations must be carefully considered when designing and operating FBRs to ensure optimal performance and longevity.
Key Points Explained:
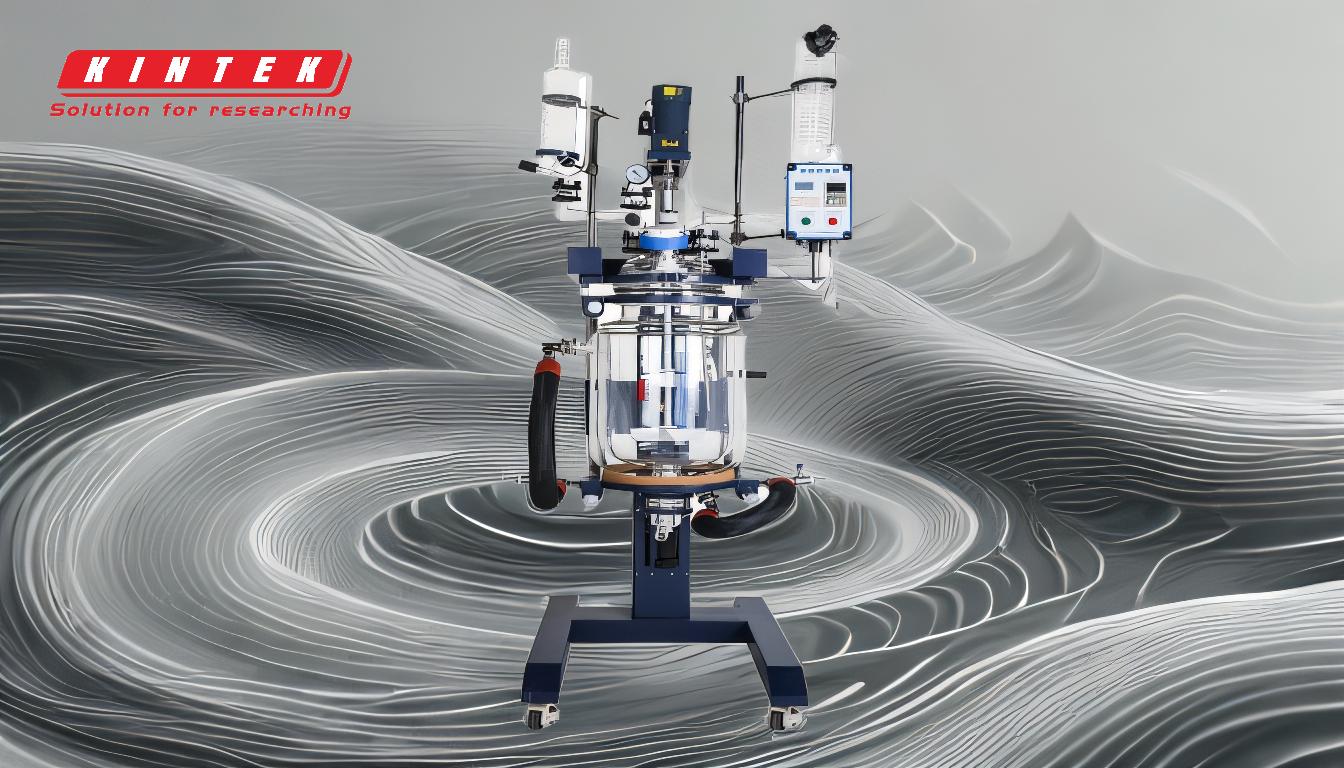
-
Increased Reactor Vessel Size:
- Fluidized bed reactors require larger vessels compared to other reactor types. This is because the fluidization process necessitates sufficient space for the solid particles to behave like a fluid. The larger size increases capital costs and space requirements, making FBRs less suitable for applications with limited space or budget constraints.
-
Higher Pumping Requirements and Pressure Drop:
- FBRs require significant energy input to maintain the fluidization state, leading to higher pumping requirements. The pressure drop across the bed can also be substantial, increasing operational costs. This is particularly challenging in large-scale operations where energy efficiency is critical.
-
Particle Entrainment:
- In FBRs, fine particles can be carried out of the reactor by the fluidizing gas, a phenomenon known as particle entrainment. This can lead to loss of valuable catalyst or reactant materials and may require additional equipment like cyclones or filters to capture and recycle the entrained particles, adding to the complexity and cost of the system.
-
Erosion of Internal Components:
- The constant movement of solid particles in a fluidized bed can cause erosion of internal components such as reactor walls, heat exchangers, and distributor plates. This erosion can lead to frequent maintenance and replacement of parts, increasing operational downtime and costs.
-
Pressure Loss Scenarios:
- FBRs are susceptible to pressure loss scenarios, which can disrupt the fluidization process and reduce reactor efficiency. Pressure losses can occur due to blockages, uneven distribution of fluidizing gas, or changes in particle size and density. Managing these pressure losses is crucial for maintaining stable operation.
-
Challenges in Scaling Up Heat Transfer:
- While FBRs offer excellent heat transfer characteristics at small scales, scaling up heat transfer in large reactors is challenging. The design must carefully consider the heat transfer method, whether it involves a heat carrier cycle or direct heat exchange. Inadequate heat transfer can lead to hot or cold spots, reducing reaction efficiency and potentially causing safety issues.
-
Lack of Current Understanding of Material Behavior:
- The behavior of materials in a fluidized bed is complex and not fully understood, particularly at large scales. This lack of understanding can lead to unpredictable operational issues, such as changes in fluidization quality, particle agglomeration, or unexpected chemical reactions. Ongoing research is needed to improve the predictability and control of FBR operations.
-
Operational Complexity:
- The continuous operation of FBRs, while advantageous for production efficiency, also introduces operational complexity. Maintaining steady-state conditions requires precise control of parameters such as gas flow rate, temperature, and particle size distribution. Any deviations can lead to process instability, requiring skilled operators and advanced control systems.
-
Environmental and Safety Concerns:
- The handling of fine particles and high-velocity gases in FBRs can pose environmental and safety risks. Dust emissions, potential for explosions, and the release of hazardous gases are concerns that need to be addressed through proper design, operation, and safety measures.
In summary, while fluidized bed reactors offer significant advantages in terms of mixing, temperature control, and continuous operation, their limitations—such as increased vessel size, higher energy requirements, particle entrainment, erosion, and challenges in scaling up heat transfer—must be carefully managed. Understanding these limitations is crucial for optimizing the design and operation of FBRs in various industrial applications.
Summary Table:
Limitation | Description |
---|---|
Increased Reactor Vessel Size | Larger vessels required, increasing capital costs and space requirements. |
Higher Pumping Requirements | Significant energy input needed, leading to higher operational costs. |
Particle Entrainment | Fine particles carried out, requiring additional equipment for recovery. |
Erosion of Internal Components | Constant particle movement causes wear, increasing maintenance costs. |
Pressure Loss Scenarios | Disrupts fluidization, requiring careful management to maintain efficiency. |
Challenges in Scaling Heat Transfer | Difficult to scale up, leading to potential hot or cold spots. |
Lack of Material Behavior Understanding | Unpredictable operational issues due to complex material behavior. |
Operational Complexity | Requires precise control of parameters, increasing operational demands. |
Environmental and Safety Concerns | Risks include dust emissions, explosions, and hazardous gas releases. |
Need help optimizing your fluidized bed reactor? Contact our experts today for tailored solutions!