Roll bending is a widely used metal forming process that involves passing a metal sheet or plate through a series of rollers to achieve a curved shape. While it is versatile and efficient, it does have certain limitations that can affect its applicability and effectiveness. These limitations include material constraints, geometric restrictions, equipment limitations, and challenges related to precision and surface finish. Understanding these limitations is crucial for selecting the appropriate bending method for a given application and ensuring the desired outcome.
Key Points Explained:
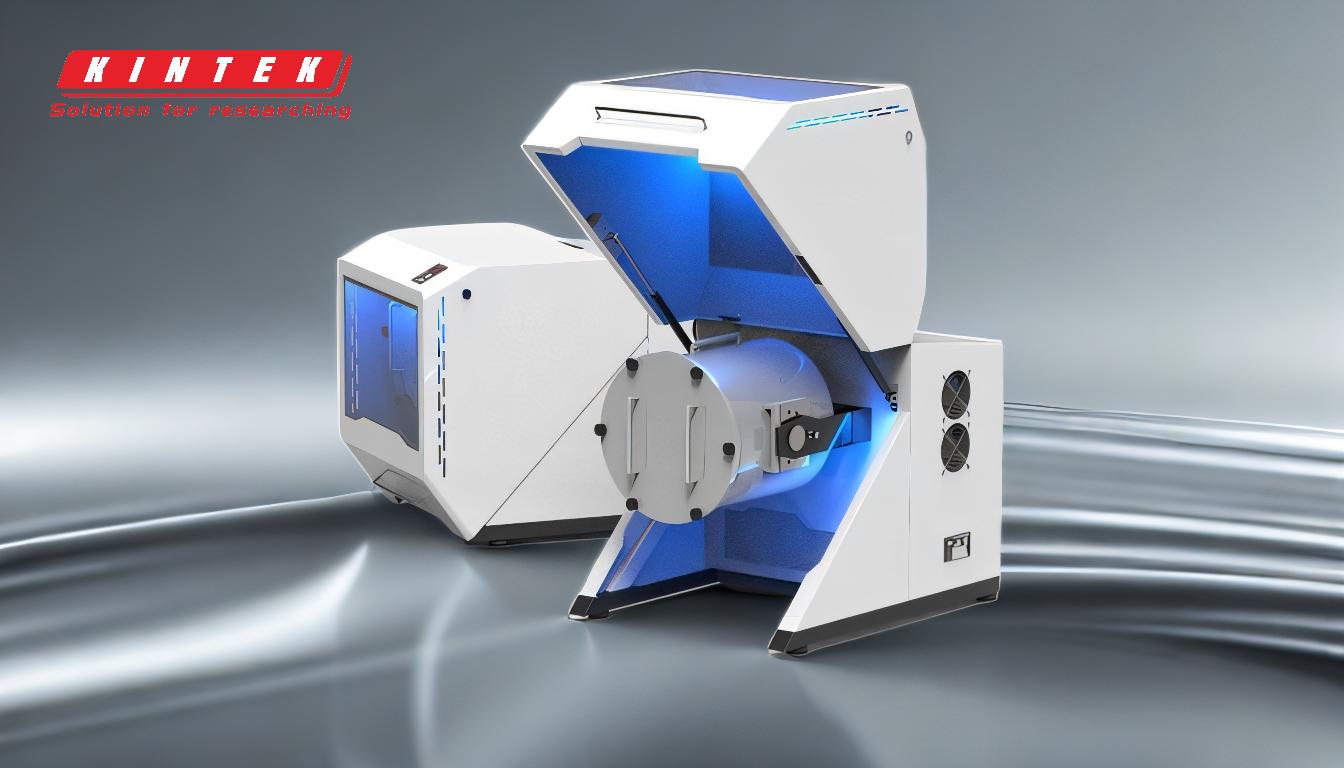
-
Material Constraints:
- Thickness and Hardness: Roll bending is more effective for materials with moderate thickness and hardness. Extremely thick or hard materials may require excessive force, leading to equipment strain or failure. Conversely, very thin materials can deform or wrinkle under the pressure of the rollers.
- Material Type: Not all materials are suitable for roll bending. Brittle materials, such as cast iron, may crack or fracture during the process. Ductile materials like mild steel, aluminum, and stainless steel are more amenable to roll bending.
-
Geometric Restrictions:
- Minimum Bend Radius: There is a limit to how tight a curve can be achieved with roll bending. The minimum bend radius depends on the material's thickness and properties. Exceeding this limit can cause cracking or deformation.
- Shape Complexity: Roll bending is primarily suited for creating simple curves or cylinders. Complex shapes with multiple curves or intricate designs may require alternative forming methods, such as press braking or stamping.
-
Equipment Limitations:
- Roller Size and Capacity: The size and capacity of the rollers determine the maximum thickness and width of the material that can be bent. Large or heavy-duty rollers are needed for thicker or wider materials, which may not be available in all facilities.
- Machine Flexibility: Some roll bending machines are designed for specific tasks and may not be easily adjustable for different materials or shapes. This lack of flexibility can limit the range of applications.
-
Precision and Surface Finish:
- Tolerance Control: Achieving precise tolerances with roll bending can be challenging, especially for complex shapes or tight curves. Variations in material properties, roller alignment, and machine settings can affect the final dimensions.
- Surface Damage: The contact between the rollers and the material can sometimes cause surface marks or scratches. This is particularly problematic for materials that require a high-quality surface finish, such as decorative panels or precision components.
-
Operational Challenges:
- Setup Time: Setting up the rollers and adjusting the machine for a specific job can be time-consuming, especially for custom or one-off projects. This can increase production time and costs.
- Skill Requirement: Operating a roll bending machine requires skill and experience. Inexperienced operators may struggle to achieve the desired results, leading to material waste or rework.
-
Economic Considerations:
- Cost of Equipment: High-quality roll bending machines can be expensive, making them a significant investment for small or medium-sized businesses. The cost of maintenance and repairs should also be considered.
- Material Waste: The process can generate scrap material, especially when fine-tuning the setup or making adjustments. This can increase material costs and reduce overall efficiency.
In summary, while roll bending is a versatile and widely used metal forming process, it is not without its limitations. Material constraints, geometric restrictions, equipment limitations, and challenges related to precision and surface finish can all impact the effectiveness of roll bending. Understanding these limitations is essential for selecting the appropriate bending method and ensuring the desired outcome. By carefully considering these factors, manufacturers can optimize their processes and achieve high-quality results.
Summary Table:
Category | Limitations |
---|---|
Material Constraints | - Thickness and hardness limitations - Unsuitable for brittle materials |
Geometric Restrictions | - Minimum bend radius - Limited to simple curves or cylinders |
Equipment Limitations | - Roller size and capacity - Limited machine flexibility |
Precision & Finish | - Tolerance control challenges - Potential surface damage |
Operational Challenges | - Time-consuming setup - Requires skilled operators |
Economic Considerations | - High equipment costs - Material waste during setup |
Need help overcoming roll bending limitations? Contact our experts today for tailored solutions!