Coating methods on carbide inserts are crucial for enhancing their performance, durability, and resistance to wear, corrosion, and high temperatures. These methods are widely used in industries such as manufacturing, aerospace, and electronics to improve the lifespan and efficiency of cutting tools. The primary coating methods include chemical vapor deposition (CVD), physical vapor deposition (PVD), and thermal spraying, each offering unique advantages depending on the application. Below, we explore these methods in detail, focusing on their processes, benefits, and applications.
Key Points Explained:
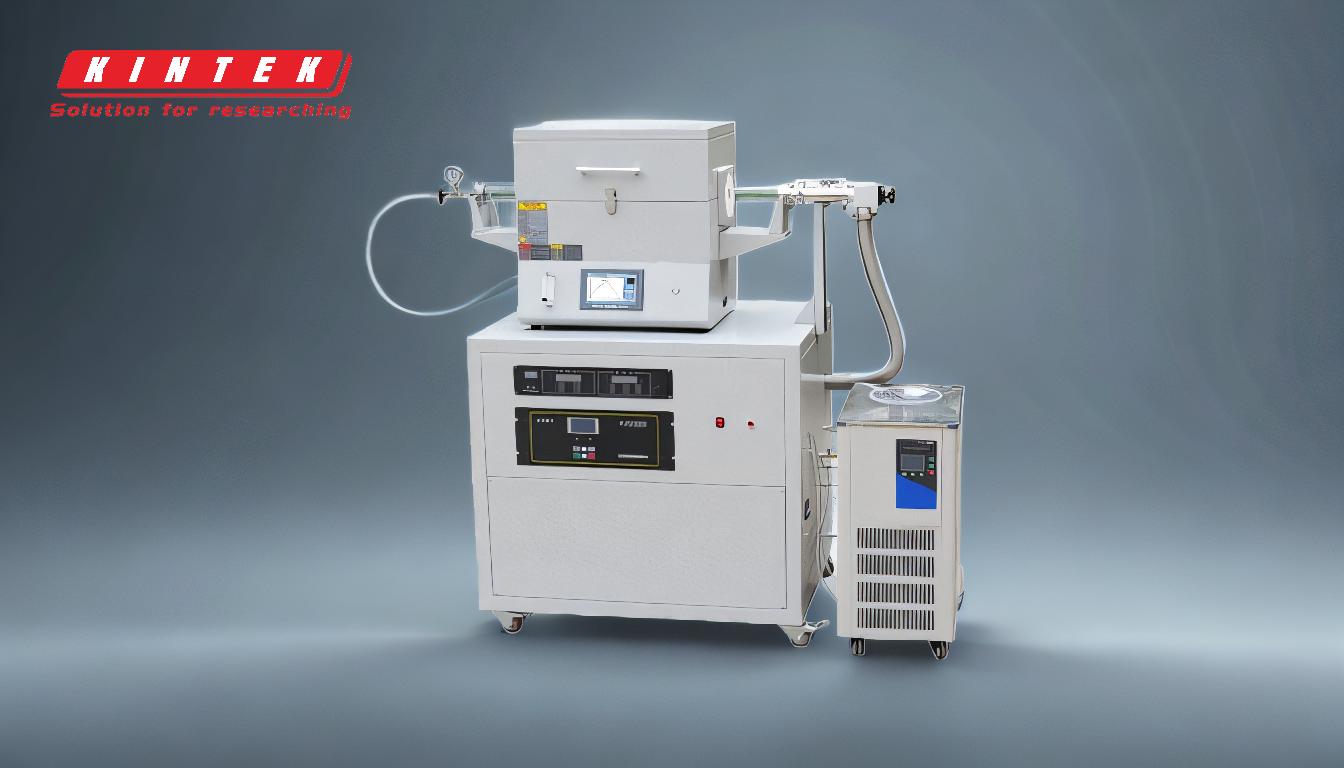
-
Chemical Vapor Deposition (CVD)
- Process: CVD involves the deposition of a thin film coating onto the carbide insert through a chemical reaction in a gaseous state. The substrate is exposed to volatile precursors, which react or decompose on the surface to form the desired coating.
-
Advantages:
- Produces uniform and high-quality coatings.
- Suitable for complex geometries due to excellent coverage.
- Enhances wear resistance, thermal stability, and chemical inertness.
- Applications: Commonly used for titanium carbide (TiC), titanium nitride (TiN), and aluminum oxide (Al₂O₃) coatings. These coatings are ideal for high-speed cutting tools and inserts used in machining hard materials.
-
Physical Vapor Deposition (PVD)
- Process: PVD involves the physical transfer of material from a solid source to the carbide insert in a vacuum environment. Techniques include sputtering, evaporation, and ion plating.
-
Advantages:
- Produces thin, dense, and adherent coatings.
- Operates at lower temperatures compared to CVD, reducing the risk of substrate deformation.
- Improves surface hardness and reduces friction.
- Applications: Widely used for titanium nitride (TiN), titanium aluminum nitride (TiAlN), and chromium nitride (CrN) coatings. These coatings are ideal for precision tools and inserts requiring high wear resistance and low friction.
-
Thermal Spraying
- Process: Thermal spraying involves heating coating materials (in powder or wire form) to a molten or semi-molten state and projecting them onto the carbide insert using a high-velocity gas stream.
-
Advantages:
- Provides thick coatings for enhanced protection.
- Suitable for large-scale applications and repairs.
- Offers excellent resistance to wear, corrosion, and thermal shock.
- Applications: Commonly used for tungsten carbide (WC) and chromium carbide (CrC) coatings. These coatings are ideal for inserts used in high-temperature and abrasive environments, such as in the aerospace and energy sectors.
-
Other Coating Methods
- Electroplating: A process where a thin layer of metal (e.g., nickel or zinc) is deposited onto the carbide insert through an electrochemical reaction. This method is often used for corrosion protection and electrical conductivity.
- Plasma-Assisted CVD (PACVD): Combines the principles of CVD with plasma to enhance coating adhesion and uniformity at lower temperatures.
- Laser Cladding: A high-precision method where a laser is used to melt and fuse coating material onto the carbide insert, providing localized protection and repair.
-
Selection Criteria for Coating Methods
- Substrate Material: The type of carbide insert and its composition influence the choice of coating method.
- Operating Conditions: Factors such as temperature, pressure, and exposure to corrosive or abrasive environments determine the most suitable coating.
- Cost and Scalability: CVD and PVD are more expensive but offer high precision, while thermal spraying is cost-effective for large-scale applications.
- Coating Thickness and Adhesion: Thicker coatings are better for wear resistance, while thinner coatings are ideal for precision tools.
By understanding these coating methods and their applications, equipment and consumable purchasers can make informed decisions to optimize the performance and longevity of carbide inserts in their operations.
Summary Table:
Coating Method | Process | Advantages | Applications |
---|---|---|---|
CVD | Chemical reaction in gaseous state to deposit thin film coatings. | Uniform, high-quality coatings; excellent coverage for complex geometries. | High-speed cutting tools, machining hard materials (TiC, TiN, Al₂O₃ coatings). |
PVD | Physical transfer of material in a vacuum (sputtering, evaporation, etc.). | Thin, dense, adherent coatings; lower temperature operation; reduces friction. | Precision tools, inserts requiring high wear resistance (TiN, TiAlN, CrN). |
Thermal Spraying | Molten/semi-molten coating materials projected onto inserts. | Thick coatings; large-scale applications; wear, corrosion, and thermal shock resistance. | High-temperature, abrasive environments (WC, CrC coatings). |
Need the right coating method for your carbide inserts? Contact our experts today for tailored solutions!