Graphene, a single layer of carbon atoms arranged in a hexagonal lattice, has garnered significant attention due to its exceptional electrical, thermal, and mechanical properties. Several methods have been developed to prepare graphene, each with its own advantages and limitations. The most common techniques include mechanical exfoliation, chemical vapor deposition (CVD), reduction of graphene oxide, and decomposition of silicon carbide. Among these, CVD stands out as the most promising method for producing large-area, high-quality graphene, while mechanical exfoliation is primarily used for fundamental research. Other methods like liquid-phase exfoliation and laser ablation are also employed, but they often face challenges related to scalability and quality. This answer explores these methods in detail, focusing on their processes, advantages, and limitations.
Key Points Explained:
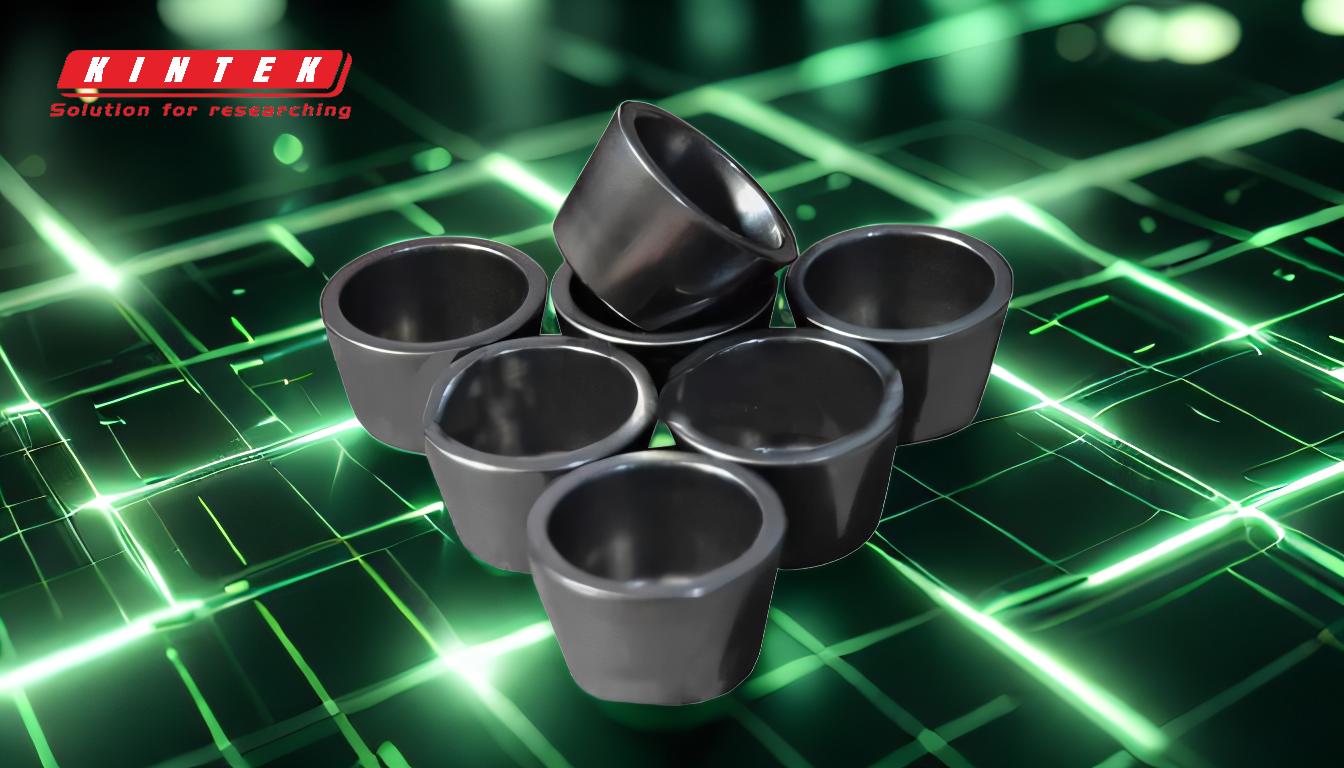
-
Mechanical Exfoliation
- Process: This method involves peeling off layers of graphene from graphite using adhesive tape or other mechanical means. It is a simple and cost-effective technique.
- Advantages: Produces high-quality graphene with minimal defects, making it ideal for fundamental research and small-scale applications.
- Limitations: Not scalable for mass production and yields only small flakes of graphene.
-
Chemical Vapor Deposition (CVD)
- Process: CVD involves the pyrolysis of a carbon-containing precursor (e.g., methane) on a substrate (e.g., copper or nickel) at high temperatures. The carbon atoms disassociate and form a graphene layer on the substrate.
- Advantages: Capable of producing large-area, high-quality graphene with good electrical properties. Suitable for industrial-scale production.
- Limitations: Requires precise control of temperature, pressure, and substrate conditions. The use of metal catalysts can introduce impurities.
-
Reduction of Graphene Oxide
- Process: Graphene oxide is first synthesized by oxidizing graphite, and then it is chemically or thermally reduced to produce graphene.
- Advantages: Relatively simple and scalable, making it suitable for mass production.
- Limitations: The resulting graphene often contains defects and residual oxygen groups, which degrade its electrical and mechanical properties.
-
Decomposition of Silicon Carbide (SiC)
- Process: Silicon carbide is heated to high temperatures, causing the silicon atoms to sublimate and leaving behind a graphene layer on the surface.
- Advantages: Produces high-quality graphene without the need for metal catalysts.
- Limitations: Expensive due to the high cost of SiC wafers and the energy-intensive process. Limited scalability for large-area production.
-
Liquid-Phase Exfoliation
- Process: Graphite is exfoliated in a liquid medium using sonication or shear forces to produce graphene flakes.
- Advantages: Scalable and cost-effective for producing graphene in large quantities.
- Limitations: Graphene produced this way often has low electrical quality and contains defects.
-
Laser Ablation and Arc-Discharge
- Process: These methods involve using high-energy lasers or electric arcs to vaporize carbon sources, which then condense to form graphene.
- Advantages: Can produce high-purity graphene with minimal contamination.
- Limitations: Complex and energy-intensive processes with limited scalability.
-
Substrate Treatment in CVD
- Process: Substrates like copper are chemically treated to reduce catalytic activity, increase grain size, and improve surface morphology, leading to better graphene growth.
- Advantages: Enhances the quality of CVD graphene by reducing defects and imperfections.
- Limitations: Adds complexity to the CVD process and may require additional post-processing steps.
In summary, the choice of graphene preparation method depends on the intended application. For high-quality, small-scale applications, mechanical exfoliation is ideal, while CVD is the best option for large-area, high-quality graphene suitable for industrial use. Reduction of graphene oxide and liquid-phase exfoliation offer scalable alternatives but often compromise on quality. Decomposition of SiC and laser ablation are niche methods with specific advantages and limitations. Understanding these methods allows for informed decision-making based on the desired graphene properties and application requirements.
Summary Table:
Method | Advantages | Limitations |
---|---|---|
Mechanical Exfoliation | High-quality graphene, minimal defects, ideal for research | Not scalable, yields small flakes |
Chemical Vapor Deposition (CVD) | Large-area, high-quality graphene, suitable for industrial use | Requires precise control, metal catalysts may introduce impurities |
Reduction of Graphene Oxide | Scalable, simple process for mass production | Graphene contains defects, residual oxygen groups degrade properties |
Decomposition of SiC | High-quality graphene, no metal catalysts required | Expensive, limited scalability, energy-intensive |
Liquid-Phase Exfoliation | Scalable, cost-effective for large quantities | Low electrical quality, defects in graphene |
Laser Ablation/Arc-Discharge | High-purity graphene, minimal contamination | Complex, energy-intensive, limited scalability |
Substrate Treatment in CVD | Enhances graphene quality, reduces defects | Adds complexity, may require additional post-processing |
Need help choosing the best graphene preparation method for your needs? Contact our experts today for personalized advice!