Aluminum brazing is a critical process in joining aluminum components, and it involves several methods, each with its unique advantages and applications. The primary methods include vacuum brazing, brazing with non-corrosive flux in a protective atmosphere, and the use of specific filler-metal alloys. These methods are designed to overcome challenges such as oxide formation and the need for high-strength, corrosion-resistant joints. The choice of method depends on factors like the alloy composition, desired joint properties, and the operational environment. Below, we delve into the key aspects of these methods, focusing on their mechanisms, advantages, and critical considerations.
Key Points Explained:
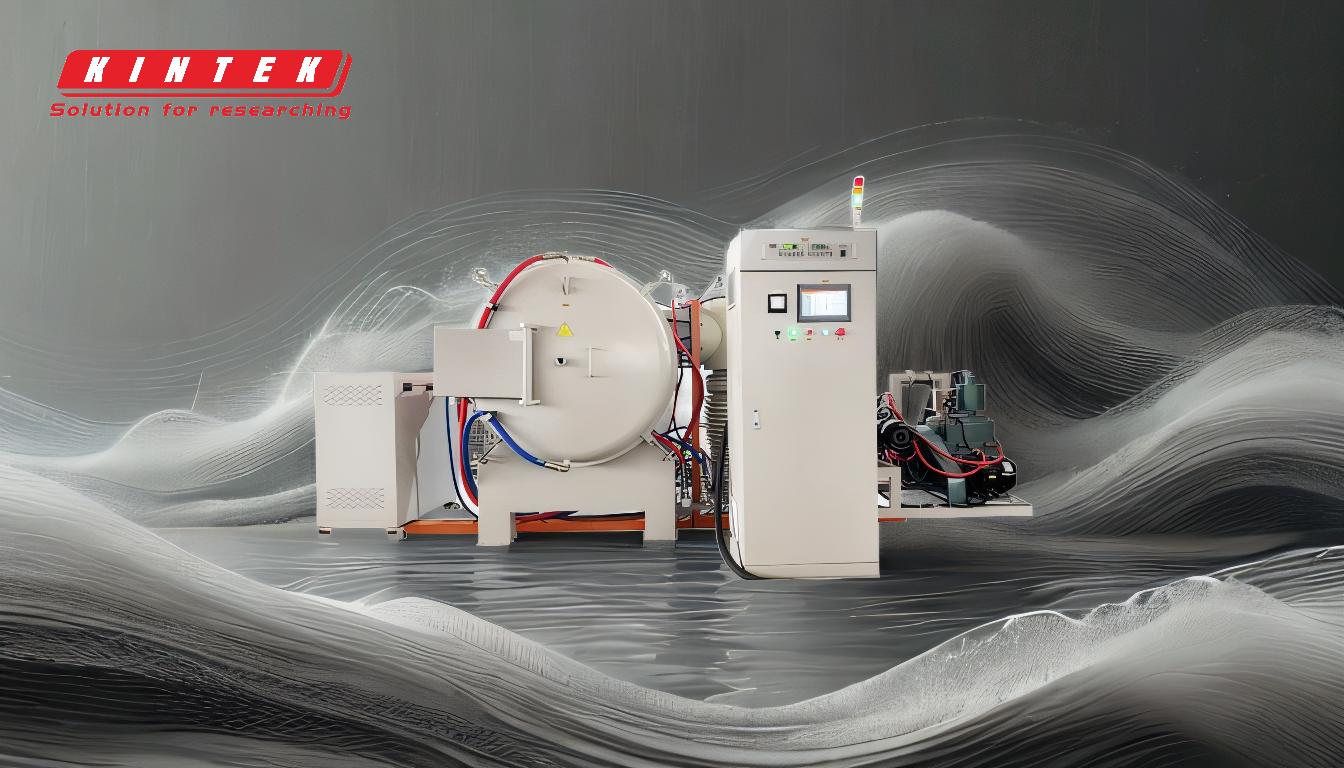
-
Filler-Metal Alloys in Aluminum Brazing:
- Composition and Characteristics: Filler-metal alloys used in aluminum brazing typically belong to the 4000 series, which includes aluminum-silicon eutectic compositions. These alloys have a low melting point and a narrow liquidus-solidus interval, making them ideal for brazing. The silicon content, usually around 12%, ensures good brazeability, strength, and corrosion resistance.
- Special Alloys: Alloys like 4004 and 4104, which contain high magnesium content, are particularly suited for vacuum brazing. Magnesium acts as an oxide-reducing agent, eliminating the need for flux in vacuum environments. This property is crucial for achieving clean, high-quality joints without the risk of flux contamination.
-
Vacuum Brazing with Magnesium Evaporation:
- Process Overview: Vacuum brazing is a fluxless method where magnesium in the filler metal evaporates at high temperatures, reducing surface oxides and facilitating the wetting of the base metal by the filler metal. This process is highly effective for producing strong, clean joints.
- Critical Parameters: Key factors include maintaining a high vacuum level (10^-5 mbar or better), precise temperature control (575-590°C), and uniform heating (±5.5°C). These conditions ensure optimal brazing outcomes, particularly for complex or sensitive components.
-
Brazing with Non-Corrosive Flux in a Protective Atmosphere:
- Advantages Over Corrosive Fluxes: This method uses non-corrosive fluxes in conjunction with a protective atmosphere (such as nitrogen or argon) to prevent oxidation during the brazing process. It avoids the drawbacks associated with corrosive fluxes, such as residue formation and potential corrosion of the joint.
- Applications: This technique is suitable for applications where vacuum brazing is impractical or where the use of flux is necessary to achieve proper wetting and joint formation.
-
Al-Si System in Brazing Alloys:
- Eutectic Composition: The Al-Si system, particularly with a silicon content of 11.7%, forms a eutectic alloy with a melting point of 577°C. This composition is widely used in brazing due to its excellent brazeability, strength, and compatibility with various aluminum alloys.
- Performance Benefits: The eutectic nature of the Al-Si system ensures consistent melting and solidification, leading to strong, durable joints. Additionally, the alloy’s properties enhance the toughness and bending strength of the brazed joint.
-
Operational Considerations:
- Furnace Requirements: Multiple-zone temperature-controlled furnaces are essential for maintaining precise temperature uniformity and achieving consistent brazing results. The furnace design must accommodate the specific configuration and fixturing of the parts being brazed.
- Cycle Times: The duration of the brazing cycle depends on factors such as furnace type, part geometry, and fixturing. Optimizing these parameters is crucial for efficient production and high-quality outcomes.
By understanding these methods and their underlying principles, manufacturers can select the most appropriate aluminum brazing technique for their specific needs, ensuring strong, reliable, and corrosion-resistant joints.
Summary Table:
Method | Key Features | Applications |
---|---|---|
Vacuum Brazing | Fluxless, uses magnesium evaporation for oxide reduction, clean and strong joints | Complex or sensitive components, high-quality requirements |
Non-Corrosive Flux Brazing | Uses non-corrosive flux in protective atmosphere, prevents oxidation | Applications where vacuum brazing is impractical or flux is necessary |
Filler-Metal Alloys (4000 Series) | Low melting point, narrow liquidus-solidus interval, excellent brazeability | General aluminum brazing, high-strength and corrosion-resistant joints |
Al-Si Eutectic Alloys | 11.7% silicon content, eutectic composition for consistent melting and strength | High-performance brazing, enhanced toughness and bending strength |
Ready to optimize your aluminum brazing process? Contact our experts today for tailored solutions!