Sintering is a thermal process used to densify powder materials by heating them below their melting point, enabling atomic diffusion and particle bonding. This process is widely used in manufacturing ceramics, metals, and plastics, and involves various techniques depending on the application and material properties. The primary methods of sintering include Conventional Sintering, Spark Plasma Sintering (SPS), and Microwave Sintering, each offering unique advantages in terms of efficiency, material properties, and application suitability.
Key Points Explained:
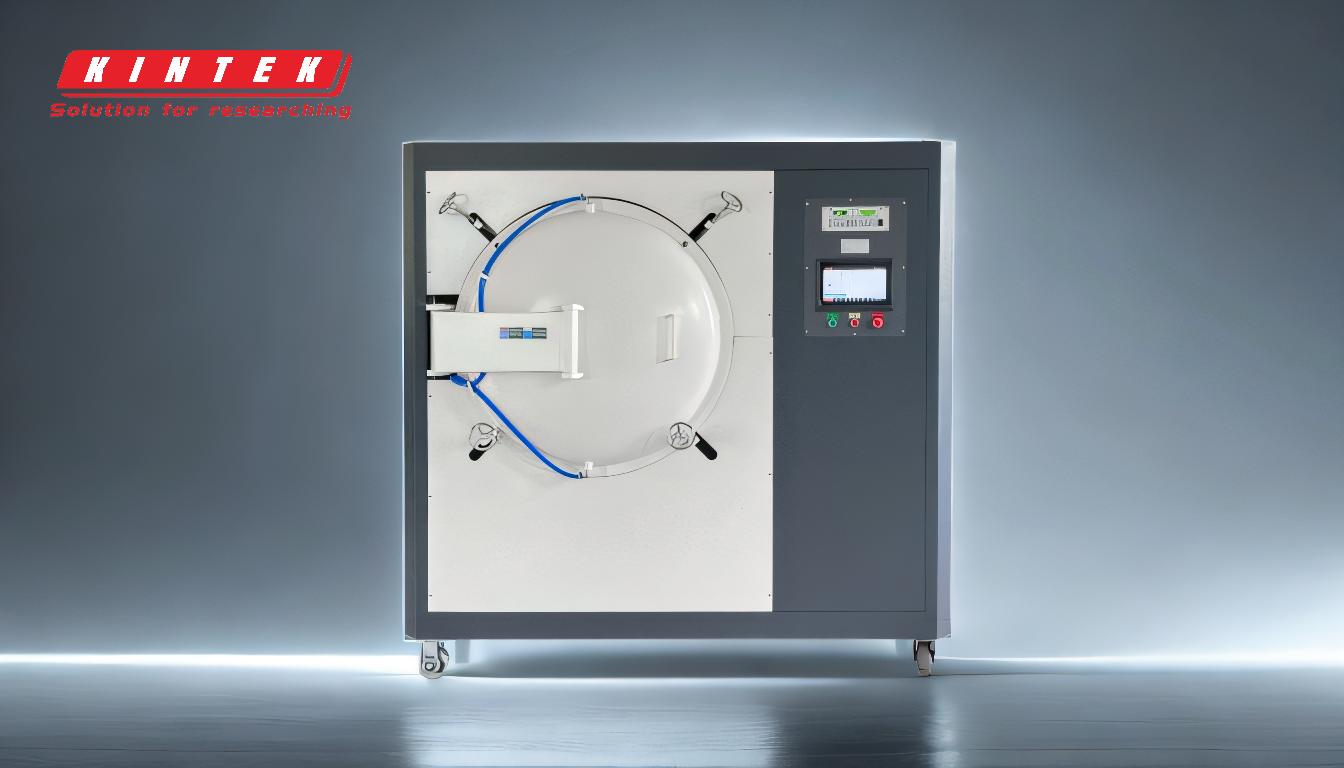
-
Conventional Sintering:
- Process Overview: Conventional sintering is the most traditional method, involving heating powdered materials in a furnace at temperatures below their melting point. The heat facilitates atomic diffusion, causing particles to bond and form a solid mass.
- Stages: The process typically occurs in stages, including initial particle bonding, densification, and grain growth, which enhance the material's structural integrity and strength.
- Applications: This method is widely used for ceramics and metals, particularly in industries requiring high-density components like automotive parts, cutting tools, and electrical insulators.
- Advantages: It is cost-effective, well-understood, and suitable for large-scale production.
- Limitations: It can be time-consuming and may require additional post-processing to achieve desired properties.
-
Spark Plasma Sintering (SPS):
- Process Overview: SPS is an advanced sintering technique that uses pulsed direct current (DC) to generate rapid heating and pressure simultaneously. This method allows for faster densification and bonding of particles.
- Mechanism: The pulsed current creates localized plasma at particle contacts, enhancing atomic diffusion and reducing sintering time significantly compared to conventional methods.
- Applications: SPS is ideal for producing high-performance materials like nanostructured ceramics, composites, and advanced alloys used in aerospace, biomedical, and energy sectors.
- Advantages: It offers faster processing times, lower energy consumption, and the ability to produce materials with fine microstructures and enhanced mechanical properties.
- Limitations: The equipment is expensive, and the process requires precise control of parameters like temperature and pressure.
-
Microwave Sintering:
- Process Overview: Microwave sintering uses electromagnetic waves to heat the material volumetrically, allowing for uniform heating and faster processing compared to conventional methods.
- Mechanism: The microwaves interact with the material's dielectric properties, causing internal heating and rapid atomic diffusion, which leads to densification.
- Applications: This method is particularly effective for ceramics and composite materials, including those used in electronics, telecommunications, and medical devices.
- Advantages: It reduces processing time, minimizes energy consumption, and produces materials with uniform microstructures and improved properties.
- Limitations: It requires materials that can absorb microwaves effectively, and the process may need optimization for specific applications.
-
Other Sintering Methods:
- Hot Isostatic Pressing (HIP): Combines high temperature and pressure in an inert gas environment to achieve full densification of materials, commonly used for aerospace and medical components.
- Pressureless Sintering: Relies solely on heat without external pressure, suitable for materials that densify easily, such as certain ceramics.
- Liquid Phase Sintering: Involves a small amount of liquid phase to enhance particle bonding, often used for materials like tungsten carbide.
Each sintering method has its unique advantages and limitations, making them suitable for specific applications and materials. Understanding these methods helps in selecting the appropriate technique based on the desired material properties, production scale, and cost considerations.
Summary Table:
Sintering Method | Key Features | Applications | Advantages | Limitations |
---|---|---|---|---|
Conventional Sintering | Heating below melting point, atomic diffusion, particle bonding | Ceramics, metals (automotive, cutting tools, electrical insulators) | Cost-effective, large-scale production | Time-consuming, may require post-processing |
Spark Plasma Sintering | Pulsed DC for rapid heating and pressure, localized plasma | Nanostructured ceramics, composites, advanced alloys (aerospace, biomedical) | Faster processing, fine microstructures, enhanced mechanical properties | Expensive equipment, precise parameter control needed |
Microwave Sintering | Electromagnetic waves for volumetric heating, uniform heating | Ceramics, composites (electronics, telecommunications, medical devices) | Reduced processing time, uniform microstructures, lower energy consumption | Requires microwave-absorbing materials, process optimization needed |
Other Methods | Includes Hot Isostatic Pressing (HIP), Pressureless Sintering, Liquid Phase Sintering | Aerospace, medical components, tungsten carbide | Varies by method | Varies by method |
Need help selecting the right sintering method for your materials? Contact our experts today!