Thin film deposition is a critical process in various industries, including electronics, optics, and coatings, where precise and controlled layering of materials is required. The methods used to deposit thin films can be broadly categorized into physical and chemical techniques. Physical methods, such as evaporation and sputtering, involve the physical transfer of material from a source to a substrate. Chemical methods, such as chemical vapor deposition (CVD) and atomic layer deposition (ALD), rely on chemical reactions to form thin films. Each method has its unique advantages, limitations, and applications, making it essential to choose the right technique based on the desired film properties and substrate requirements.
Key Points Explained:
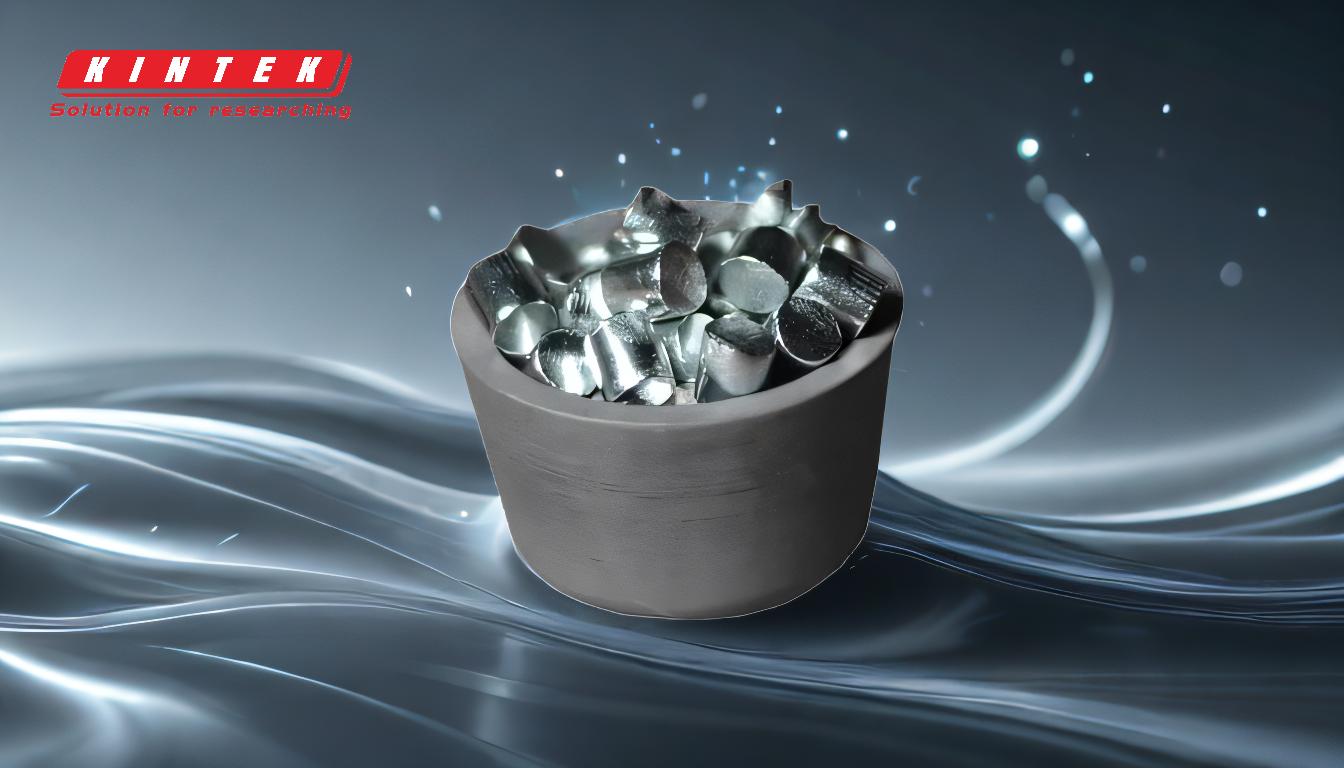
-
Physical Vapor Deposition (PVD)
- Definition: PVD involves the physical transfer of material from a source to a substrate, typically in a vacuum environment.
-
Common Techniques:
- Evaporation: The target material is heated until it vaporizes, and the vapor condenses on the substrate to form a thin film. This can be done using thermal evaporation, electron beam evaporation, or laser ablation.
- Sputtering: A target material is bombarded with high-energy ions, causing atoms to be ejected and deposited onto the substrate. Techniques include magnetron sputtering and ion beam sputtering.
- Advantages: High purity films, good adhesion, and compatibility with a wide range of materials.
- Applications: Used in microelectronics, optical coatings, and decorative finishes.
-
Chemical Vapor Deposition (CVD)
- Definition: CVD involves the use of chemical reactions to deposit a thin film on a substrate. Precursor gases react on the substrate surface to form the desired material.
-
Common Techniques:
- Thermal CVD: Uses heat to drive the chemical reactions.
- Plasma-Enhanced CVD (PECVD): Utilizes plasma to enhance the reaction at lower temperatures.
- Atomic Layer Deposition (ALD): Deposits films one atomic layer at a time, offering exceptional control over thickness and uniformity.
- Advantages: High-quality films with excellent conformality, suitable for complex geometries.
- Applications: Widely used in semiconductor manufacturing, protective coatings, and nanotechnology.
-
Chemical Solution Deposition (CSD)
- Definition: CSD involves depositing thin films from liquid precursors, often through processes like spin coating, dip coating, or spray pyrolysis.
-
Common Techniques:
- Spin Coating: A liquid precursor is spread onto a substrate, which is then spun at high speed to create a uniform thin film.
- Dip Coating: The substrate is dipped into a solution and withdrawn at a controlled speed to form a thin layer.
- Spray Pyrolysis: A solution is sprayed onto a heated substrate, where it decomposes to form a thin film.
- Advantages: Low-cost, simple equipment, and suitable for large-area deposition.
- Applications: Used in solar cells, sensors, and optical coatings.
-
Electrochemical Deposition (Electroplating)
- Definition: This method uses an electric current to reduce metal ions in a solution, depositing them onto a conductive substrate.
- Advantages: Cost-effective, capable of depositing thick films, and suitable for complex shapes.
- Applications: Commonly used in the automotive and electronics industries for coatings and connectors.
-
Molecular Beam Epitaxy (MBE)
- Definition: MBE is a highly controlled technique where beams of atoms or molecules are directed at a substrate under ultra-high vacuum conditions, allowing for the precise growth of crystalline films.
- Advantages: Extremely precise control over film composition and thickness, ideal for high-performance materials.
- Applications: Used in the fabrication of advanced semiconductor devices and quantum structures.
-
Pulsed Laser Deposition (PLD)
- Definition: PLD involves using a high-power laser to ablate material from a target, which is then deposited onto a substrate.
- Advantages: Ability to deposit complex materials with high stoichiometric accuracy.
- Applications: Used in research and development for materials like superconductors and complex oxides.
Each of these methods has its own set of parameters, such as temperature, pressure, and precursor materials, which can be tailored to achieve specific film properties like thickness, uniformity, and composition. The choice of deposition technique depends on factors such as the material being deposited, the substrate, the required film properties, and the scale of production.
Summary Table:
Method | Key Techniques | Advantages | Applications |
---|---|---|---|
Physical Vapor Deposition (PVD) | Evaporation, Sputtering | High purity films, good adhesion, wide material compatibility | Microelectronics, optical coatings, decorative finishes |
Chemical Vapor Deposition (CVD) | Thermal CVD, PECVD, ALD | High-quality films, excellent conformality, suitable for complex geometries | Semiconductor manufacturing, protective coatings, nanotechnology |
Chemical Solution Deposition (CSD) | Spin coating, Dip coating, Spray pyrolysis | Low-cost, simple equipment, suitable for large-area deposition | Solar cells, sensors, optical coatings |
Electrochemical Deposition | Electroplating | Cost-effective, thick films, suitable for complex shapes | Automotive and electronics industries |
Molecular Beam Epitaxy (MBE) | Ultra-high vacuum deposition | Precise control over film composition and thickness | Advanced semiconductor devices, quantum structures |
Pulsed Laser Deposition (PLD) | Laser ablation | High stoichiometric accuracy, complex material deposition | Research and development for superconductors, complex oxides |
Need help selecting the right thin film deposition method for your project? Contact our experts today!