Hydraulic systems are critical components in many industrial and mobile applications, but they are prone to failure due to various factors. The most common causes of hydraulic system failure include contamination, overheating, fluid degradation, improper maintenance, and component wear. Contamination, such as dirt, water, or metal particles, can damage internal components and reduce system efficiency. Overheating can lead to fluid breakdown and seal failure, while improper fluid selection or degradation can cause viscosity issues and internal corrosion. Lack of regular maintenance, such as filter changes or fluid analysis, can exacerbate these problems. Additionally, wear and tear on components like pumps, valves, and hoses over time can lead to leaks or complete system failure. Addressing these issues through proper design, maintenance, and monitoring is essential to ensure the longevity and reliability of hydraulic systems.
Key Points Explained:
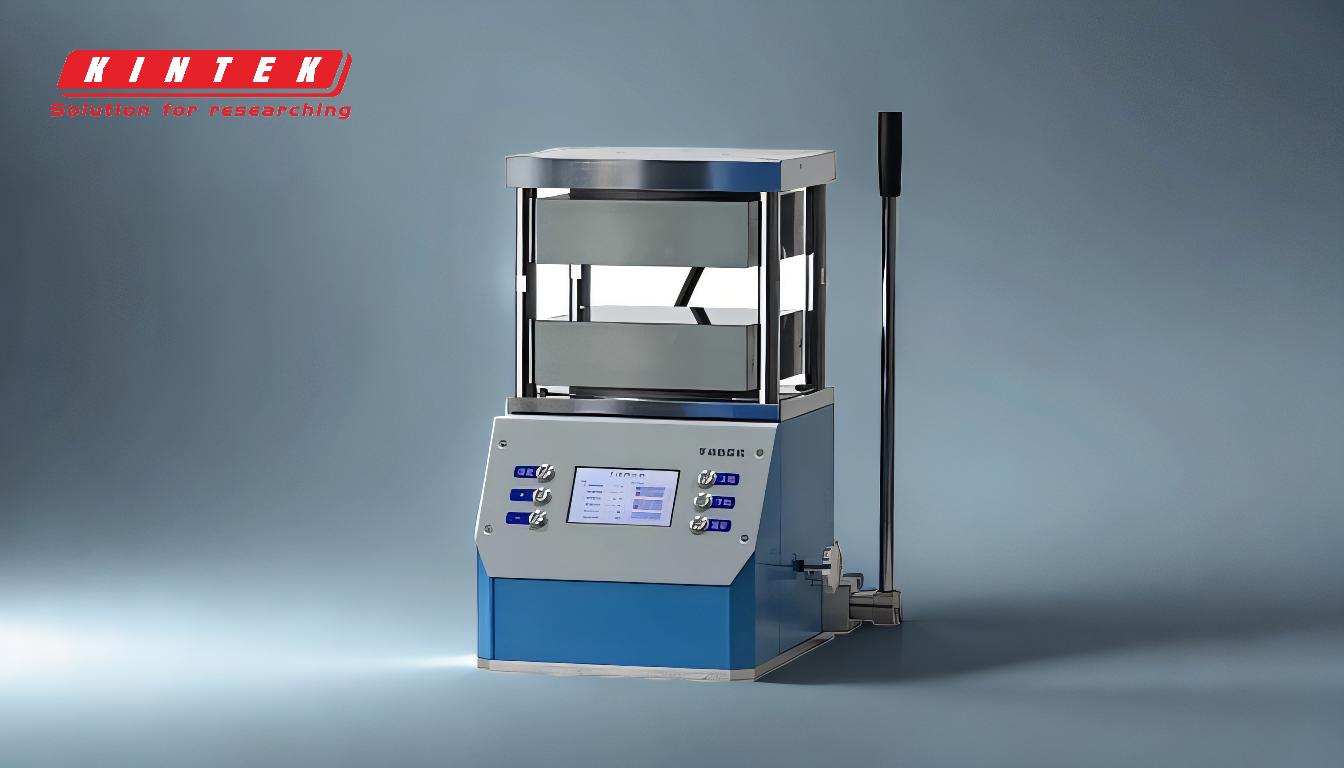
-
Contamination
- Contamination is one of the leading causes of hydraulic system failure.
- Types of contaminants include dirt, water, metal particles, and air.
- Effects: Contaminants can cause abrasion, corrosion, and blockages in sensitive components like pumps, valves, and cylinders.
- Prevention: Use high-quality filters, maintain proper sealing, and implement regular fluid analysis to detect contamination early.
-
Overheating
- Overheating occurs when the system operates beyond its designed temperature range.
- Causes: Poor cooling, excessive load, or inadequate fluid levels.
- Effects: Overheating can degrade hydraulic fluid, reduce viscosity, and damage seals and hoses.
- Prevention: Ensure proper cooling systems, monitor fluid temperature, and avoid overloading the system.
-
Fluid Degradation
- Hydraulic fluid can degrade due to oxidation, thermal breakdown, or contamination.
- Effects: Degraded fluid loses its lubricating properties, leading to increased friction and wear.
- Prevention: Use high-quality fluids, monitor fluid condition, and replace fluids at recommended intervals.
-
Improper Maintenance
- Lack of regular maintenance can lead to system failures.
- Common issues: Neglecting filter changes, ignoring fluid analysis, or failing to inspect components.
- Effects: Accumulated wear and contamination can cause sudden breakdowns.
- Prevention: Follow a strict maintenance schedule, including regular inspections, fluid changes, and component replacements.
-
Component Wear
- Over time, components like pumps, valves, and hoses wear out due to normal use or improper conditions.
- Effects: Worn components can lead to leaks, reduced efficiency, or complete system failure.
- Prevention: Use high-quality components, monitor system performance, and replace worn parts promptly.
-
Improper Fluid Selection
- Using the wrong type of hydraulic fluid can cause system issues.
- Effects: Incorrect viscosity or chemical composition can lead to poor lubrication, overheating, or seal damage.
- Prevention: Always use fluids recommended by the equipment manufacturer and ensure compatibility with system materials.
-
Air Entrapment
- Air can enter the hydraulic system through leaks or improper bleeding.
- Effects: Air bubbles can cause spongy operation, reduced efficiency, and damage to components due to cavitation.
- Prevention: Regularly check for leaks, bleed the system properly, and use de-aerating filters.
By understanding these common causes of hydraulic system failure, equipment and consumable purchasers can make informed decisions about system design, maintenance practices, and component selection. Proactive measures, such as regular maintenance and monitoring, can significantly reduce the risk of failure and extend the lifespan of hydraulic systems.
Summary Table:
Cause | Effects | Prevention |
---|---|---|
Contamination | Abrasion, corrosion, blockages in components | Use high-quality filters, maintain seals, perform regular fluid analysis |
Overheating | Fluid breakdown, seal failure, reduced viscosity | Ensure proper cooling, monitor fluid temperature, avoid overloading |
Fluid Degradation | Loss of lubrication, increased friction and wear | Use high-quality fluids, monitor condition, replace fluids regularly |
Improper Maintenance | Sudden breakdowns due to wear and contamination | Follow a strict maintenance schedule, inspect components, replace filters and fluids |
Component Wear | Leaks, reduced efficiency, system failure | Use high-quality components, monitor performance, replace worn parts promptly |
Improper Fluid Selection | Poor lubrication, overheating, seal damage | Use manufacturer-recommended fluids, ensure compatibility with system materials |
Air Entrapment | Spongy operation, reduced efficiency, cavitation damage | Check for leaks, bleed the system properly, use de-aerating filters |
Ensure your hydraulic systems operate at peak performance—contact our experts today for tailored solutions and maintenance tips!