An induction furnace is a crucial piece of equipment in metal melting and casting processes, designed to efficiently heat and melt metals using electromagnetic induction. Its primary components include a power supply, an induction coil (or ring), and a crucible made of refractory materials. The power supply generates alternating current, which flows through the induction coil, creating a magnetic field. This magnetic field induces eddy currents in the metal charge within the crucible, generating heat and melting the metal. The crucible, made of heat-resistant materials, holds the metal charge and ensures the process is contained and efficient. Below, we explore the key components and their functions in detail.
Key Points Explained:
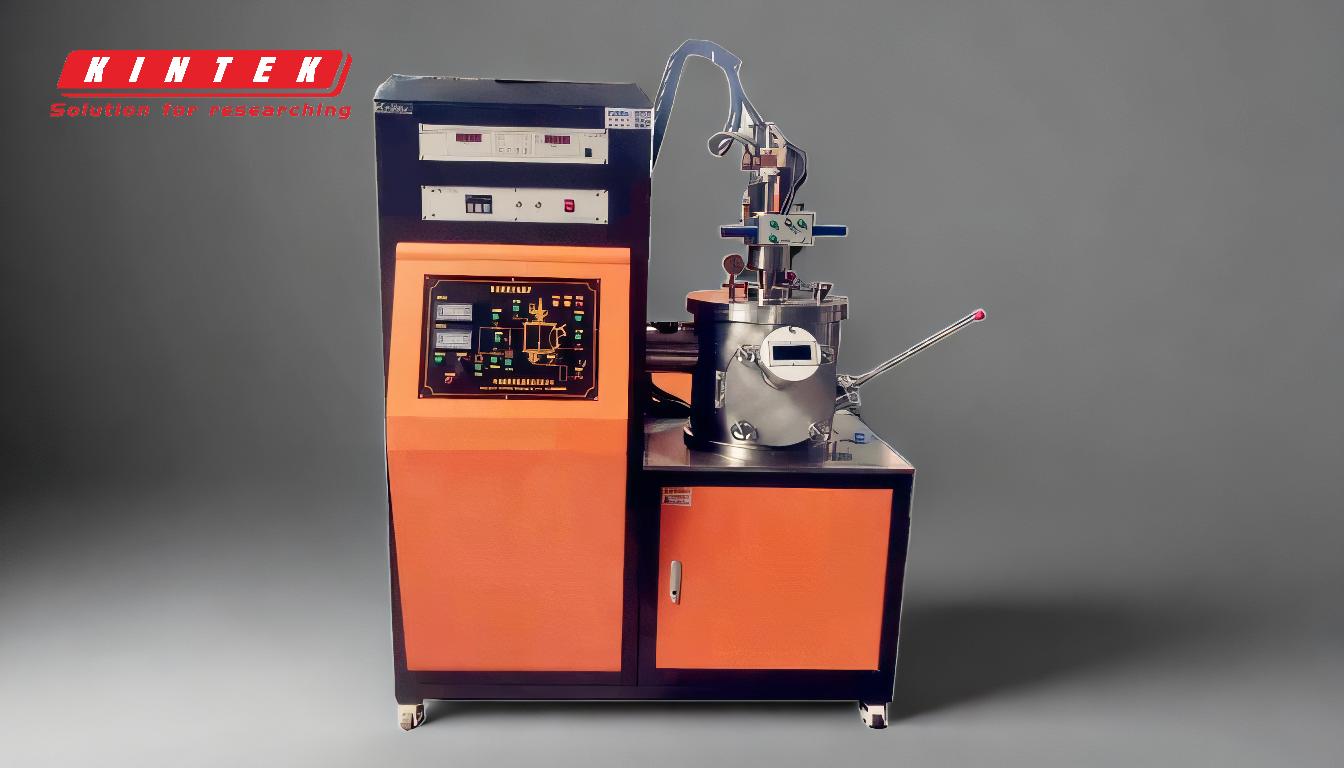
-
Power Supply
- The power supply is the heart of the induction furnace, providing the alternating current (AC) required for the induction process.
- It converts electrical energy from the grid or another source into the appropriate frequency and voltage for the induction coil.
- The power supply ensures precise control over the heating process, allowing for consistent and efficient melting of metals.
- Modern induction furnaces often use solid-state inverters for improved energy efficiency and control.
-
Induction Coil (or Induction Ring)
- The induction coil is a critical component that generates the electromagnetic field necessary for heating the metal.
- It is typically made of copper tubing or other conductive materials and is designed to withstand high temperatures and electrical currents.
- When alternating current flows through the coil, it creates a fluctuating magnetic field.
- This magnetic field induces eddy currents in the metal charge within the crucible, generating heat through resistance.
- The design and configuration of the coil are optimized for the specific type of metal being melted and the furnace's capacity.
-
Crucible
- The crucible is the container that holds the metal charge during the melting process.
- It is constructed from refractory materials, such as ceramics or graphite, which can withstand extreme temperatures and resist chemical reactions with molten metals.
- The crucible is placed inside the induction coil, where it is exposed to the electromagnetic field.
- The metal charge within the crucible acts as the secondary winding of a transformer, completing the induction heating circuit.
- Crucibles are available in various sizes and shapes to accommodate different furnace designs and metal types.
-
Metal Charge (Secondary Winding)
- The metal charge refers to the material being melted, such as iron, steel, aluminum, or other alloys.
- When placed inside the crucible, the metal charge interacts with the magnetic field generated by the induction coil.
- Eddy currents induced in the metal charge generate heat, causing the metal to melt.
- The metal charge effectively acts as the secondary winding of a transformer, completing the electrical circuit and enabling the induction process.
-
Refractory Lining
- The refractory lining surrounds the crucible and provides thermal insulation, protecting the furnace structure from extreme heat.
- It is made from materials like alumina, silica, or magnesia, which have high melting points and excellent thermal resistance.
- The lining also helps contain the molten metal, preventing leaks and ensuring safety during operation.
- Regular maintenance and replacement of the refractory lining are necessary to maintain furnace efficiency and safety.
-
Cooling System
- Induction furnaces often include a cooling system to manage the heat generated during operation.
- The induction coil, in particular, requires cooling to prevent overheating and maintain its structural integrity.
- Cooling systems typically use water or air to dissipate heat and maintain optimal operating temperatures.
- Proper cooling is essential for the longevity of the furnace components and consistent performance.
-
Control System
- Modern induction furnaces are equipped with advanced control systems for precise operation.
- These systems monitor and regulate parameters such as temperature, power input, and melting time.
- Automation features enable consistent and repeatable results, reducing human error and improving efficiency.
- Control systems also enhance safety by providing real-time alerts and shutdown mechanisms in case of malfunctions.
In summary, the induction furnace is a sophisticated system composed of several interconnected components, each playing a vital role in the melting process. Understanding these parts and their functions is essential for selecting, operating, and maintaining induction furnaces effectively. Whether for industrial metal casting or small-scale foundry work, the induction furnace remains a reliable and efficient solution for metal melting.
Summary Table:
Component | Function |
---|---|
Power Supply | Converts electrical energy into AC for precise heating control. |
Induction Coil | Generates a magnetic field to induce eddy currents and heat the metal. |
Crucible | Holds the metal charge, made of heat-resistant refractory materials. |
Metal Charge | Acts as the secondary winding, generating heat through eddy currents. |
Refractory Lining | Provides thermal insulation and contains molten metal safely. |
Cooling System | Prevents overheating of components using water or air cooling. |
Control System | Monitors and regulates temperature, power input, and melting time. |
Discover how an induction furnace can optimize your metal melting process—contact our experts today!