Pyrolysis is a thermal decomposition process that occurs in the absence of oxygen, leading to the breakdown of organic materials into gases, liquids, and solids. The physical properties of pyrolysis are influenced by factors such as temperature, heating rate, residence time, and the type of material being pyrolyzed. The process can be categorized into different types, such as slow, fast, and flash pyrolysis, each with distinct characteristics and product yields. The primary products include syngas (a mixture of hydrogen, carbon monoxide, and methane), bio-oil (a liquid mixture of water and volatile organic compounds), and bio-char (a carbon-rich solid). The specific composition and yield of these products depend on the process conditions and the feedstock used.
Key Points Explained:
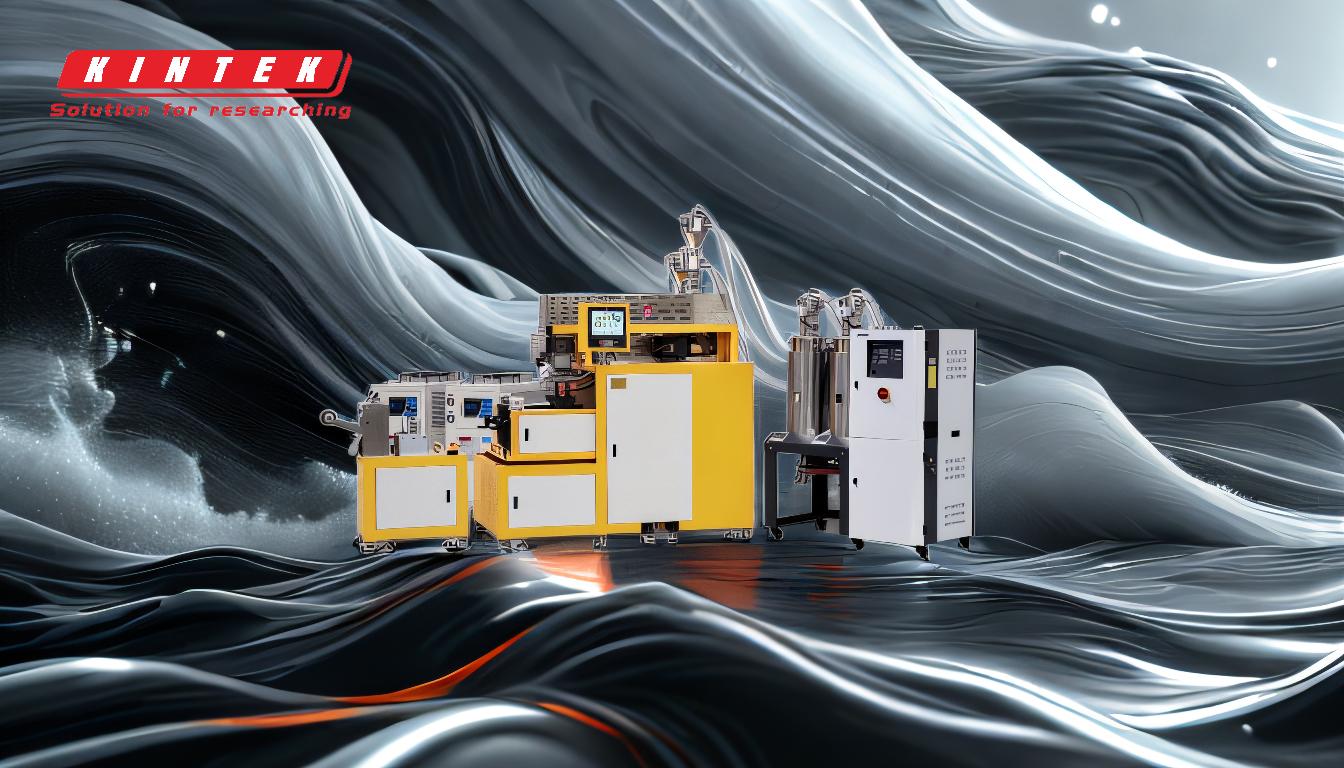
-
Temperature Range and Its Impact:
- Pyrolysis typically occurs at high temperatures ranging from 300°C to 900°C.
- The temperature significantly affects the yield and composition of the products:
- Lower temperatures (300-500°C) favor the production of bio-char.
- Moderate temperatures (400-600°C) are optimal for bio-oil production.
- Higher temperatures (above 600°C) increase the yield of syngas.
-
Heating Rate and Residence Time:
-
Slow Pyrolysis:
- Heating rates are low (0.1 to 2°C per second).
- Residence times are long, potentially several days.
- This process primarily produces bio-char and tar due to the extended exposure of gases to heat.
-
Fast Pyrolysis:
- Heating rates are high (10–200°C/s).
- Residence times are short (0.5–10 seconds).
- This process maximizes bio-oil yields, which can reach 50–70 wt% on a dry biomass basis.
-
Flash Pyrolysis:
- Even higher heating rates than fast pyrolysis.
- Results in very high bio-oil yields, up to 75–80 wt%.
-
Slow Pyrolysis:
-
Absence of Oxygen:
- Pyrolysis is conducted in an oxygen-free environment to prevent combustion.
- This ensures that the material decomposes rather than burns, leading to the formation of syngas, bio-oil, and bio-char.
-
Product Composition:
- Syngas: A mixture of hydrogen, carbon monoxide, and methane, which can be used as a fuel or chemical feedstock.
- Bio-oil: A liquid composed of water and volatile organic compounds, suitable for further refining into fuels or chemicals.
- Bio-char: A carbon-rich solid that can be used as a soil amendment or for carbon sequestration.
-
Stages of Pyrolysis:
- Dosing and Feeding: The raw material is introduced into the pyrolysis reactor.
- Transformation: The organic material undergoes thermal decomposition, breaking down into smaller molecules.
- Product Separation: The resulting products (syngas, bio-oil, and bio-char) are separated and collected.
-
Chemical Reactions:
- Pyrolysis involves the rupture of carbon–carbon bonds and the formation of carbon–oxygen bonds.
- Part of the biomass is reduced to carbon, while the remaining part is oxidized and hydrolyzed, forming various compounds.
-
Applications of Pyrolysis Products:
- Syngas: Used in power generation, as a fuel for engines, or as a feedstock for chemical synthesis.
- Bio-oil: Can be upgraded to transportation fuels or used directly in industrial boilers.
- Bio-char: Used in agriculture to improve soil health and as a means of carbon sequestration.
In summary, the physical properties of pyrolysis are defined by the process conditions, including temperature, heating rate, and residence time, which determine the yield and composition of the resulting products. These products have diverse applications, making pyrolysis a versatile and valuable process for converting biomass into useful materials and energy.
Summary Table:
Factor | Impact on Pyrolysis |
---|---|
Temperature | - 300-500°C: Favors bio-char production. - 400-600°C: Optimal for bio-oil. - Above 600°C: Increases syngas yield. |
Heating Rate | - Slow: Low rates (0.1-2°C/s), long residence time, produces bio-char. - Fast: High rates (10-200°C/s), short residence time, maximizes bio-oil. - Flash: Very high rates, highest bio-oil yield (75-80 wt%). |
Absence of Oxygen | Prevents combustion, ensures decomposition into syngas, bio-oil, and bio-char. |
Products | - Syngas: Fuel or chemical feedstock. - Bio-oil: Refined into fuels or chemicals. - Bio-char: Soil amendment or carbon sequestration. |
Ready to optimize your pyrolysis process? Contact our experts today for tailored solutions!