Annealing is a critical heat treatment process used to alter the physical and sometimes chemical properties of a material, typically metals, to increase ductility and reduce hardness. The process involves heating the material to a specific temperature, holding it there for a certain period, and then cooling it slowly. Precautions during annealing are essential to ensure the desired material properties are achieved without causing damage. Key precautions include controlling the heating rate to prevent thermal shock, maintaining the correct annealing temperature to avoid over-softening or insufficient softening, and ensuring a slow and controlled cooling rate to prevent the reintroduction of stresses. Additionally, understanding the material's specific requirements and the stages of annealing—recovery, recrystallization, and grain growth—is crucial for effective annealing.
Key Points Explained:
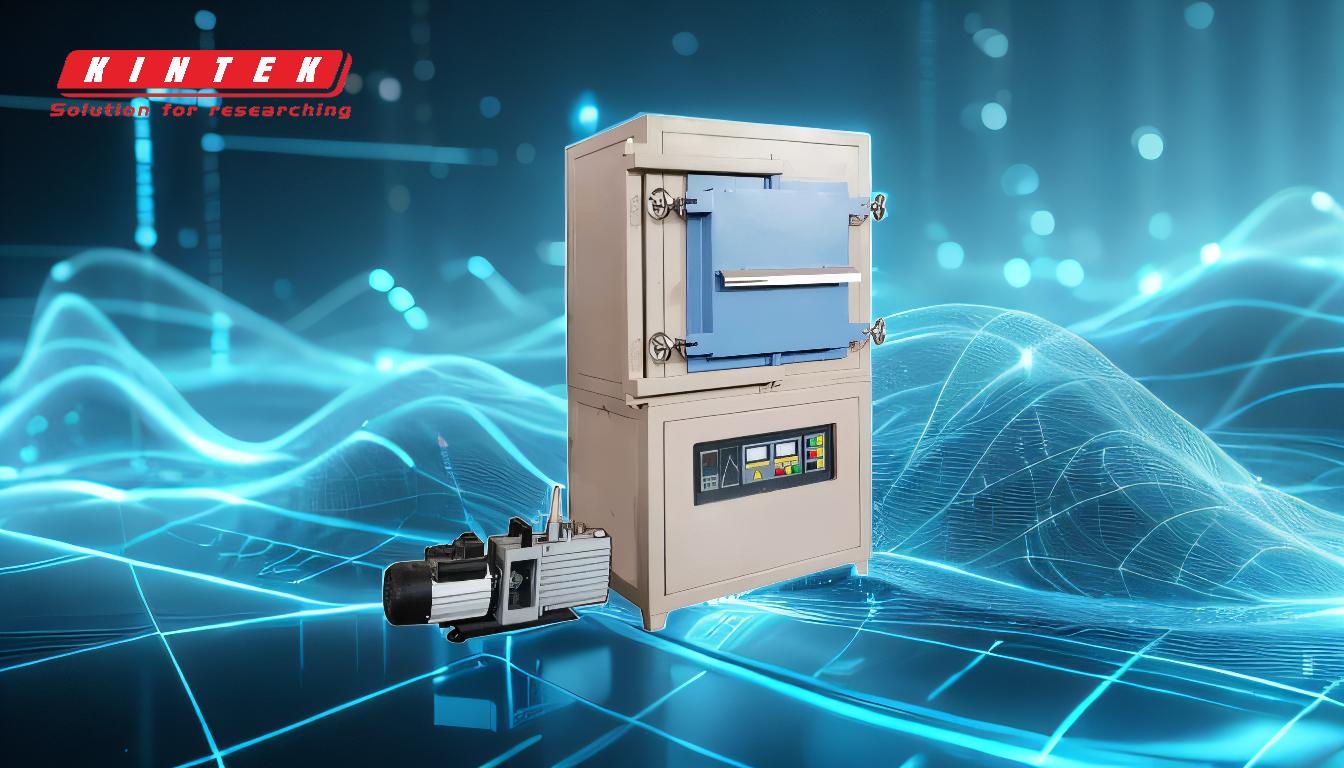
-
Controlled Heating Rate:
- Why it's important: Rapid heating can cause thermal shock, leading to cracks or warping in the material. This is particularly critical for ceramics and brittle metals.
- How to manage: Increase the temperature slowly and evenly. Use a furnace with precise temperature control to ensure uniform heating throughout the material.
-
Maintaining Correct Annealing Temperature:
- Why it's important: The annealing temperature must be high enough to allow the crystalline structure to become fluid but not so high as to cause melting or excessive grain growth.
- How to manage: Refer to material-specific annealing temperature guidelines. Use calibrated thermocouples and temperature controllers to maintain the correct temperature throughout the process.
-
Slow and Controlled Cooling:
- Why it's important: Rapid cooling can reintroduce internal stresses, defeating the purpose of annealing. Slow cooling allows the material to achieve a more ductile and stress-free state.
- How to manage: Cool the material in the furnace or a controlled environment. Avoid exposing the material to drafts or sudden temperature changes during cooling.
-
Understanding the Stages of Annealing:
- Recovery: This initial stage involves the relief of internal stresses without changing the grain structure. The material is heated to a temperature where atomic mobility is sufficient to allow dislocations to move and rearrange.
- Recrystallization: At this stage, new strain-free grains nucleate and grow to replace the deformed grains. This occurs at a higher temperature than the recovery stage.
- Grain Growth: If the material is held at the annealing temperature for too long, grains can grow larger, which may reduce the material's strength. It's important to control the duration of the annealing process to prevent excessive grain growth.
-
Material-Specific Considerations:
- Why it's important: Different materials have different annealing requirements. For example, steel requires a different annealing process compared to aluminum or copper.
- How to manage: Consult material datasheets or metallurgical guidelines for specific annealing temperatures, times, and cooling rates. Tailor the annealing process to the material being treated.
-
Atmosphere Control:
- Why it's important: Some materials are sensitive to oxidation or contamination during annealing. An uncontrolled atmosphere can lead to surface degradation or unwanted chemical reactions.
- How to manage: Use a controlled atmosphere furnace, such as one with an inert gas (e.g., nitrogen or argon), to protect the material from oxidation and contamination.
-
Monitoring and Documentation:
- Why it's important: Consistent results require precise monitoring and documentation of the annealing process. Variations in temperature, time, or cooling rate can lead to inconsistent material properties.
- How to manage: Use data logging equipment to record temperature profiles and cooling rates. Maintain detailed records for each annealing cycle to ensure repeatability and quality control.
By adhering to these precautions, the annealing process can be effectively managed to achieve the desired material properties, ensuring the final product meets the required specifications for strength, ductility, and overall performance.
Summary Table:
Precaution | Why It's Important | How to Manage |
---|---|---|
Controlled Heating Rate | Prevents thermal shock, cracks, and warping in materials. | Increase temperature slowly and evenly; use a furnace with precise temperature control. |
Correct Annealing Temperature | Avoids over-softening, insufficient softening, or excessive grain growth. | Refer to material-specific guidelines; use calibrated thermocouples and temperature controllers. |
Slow and Controlled Cooling | Prevents reintroduction of internal stresses, ensuring ductility and stress-free state. | Cool material in the furnace or a controlled environment; avoid drafts or sudden temperature changes. |
Stages of Annealing | Ensures proper recovery, recrystallization, and controlled grain growth. | Understand and control each stage: recovery, recrystallization, and grain growth. |
Material-Specific Considerations | Different materials require tailored annealing processes. | Consult material datasheets or metallurgical guidelines for specific requirements. |
Atmosphere Control | Protects materials from oxidation or contamination. | Use a controlled atmosphere furnace with inert gases like nitrogen or argon. |
Monitoring and Documentation | Ensures consistent results and repeatability. | Use data logging equipment to record temperature profiles and maintain detailed records. |
Achieve precise annealing results for your materials—contact our experts today for tailored solutions!