Pyrolysis is a thermochemical process that decomposes organic materials at high temperatures in the absence of oxygen, resulting in the breakdown of chemical bonds and the formation of new products such as bio-oil, biochar, and gases. The properties of pyrolysis vary significantly depending on the operating conditions, including temperature, heating rate, residence time, and feedstock size. These conditions influence the yield and composition of the products. For instance, flash pyrolysis operates at very high temperatures (800–1000°C) and heating rates (>1000°C/s), producing high bio-oil yields (~75%). In contrast, slow pyrolysis occurs at lower temperatures (around 500°C) and slower heating rates (0.1–2°C/s), favoring the production of biochar and tar. Fast pyrolysis, with moderate temperatures (400–600°C) and short residence times (0.5–10 s), primarily yields bio-oil and biogas. Understanding these properties is crucial for optimizing pyrolysis processes for specific applications, such as energy production or waste management.
Key Points Explained:
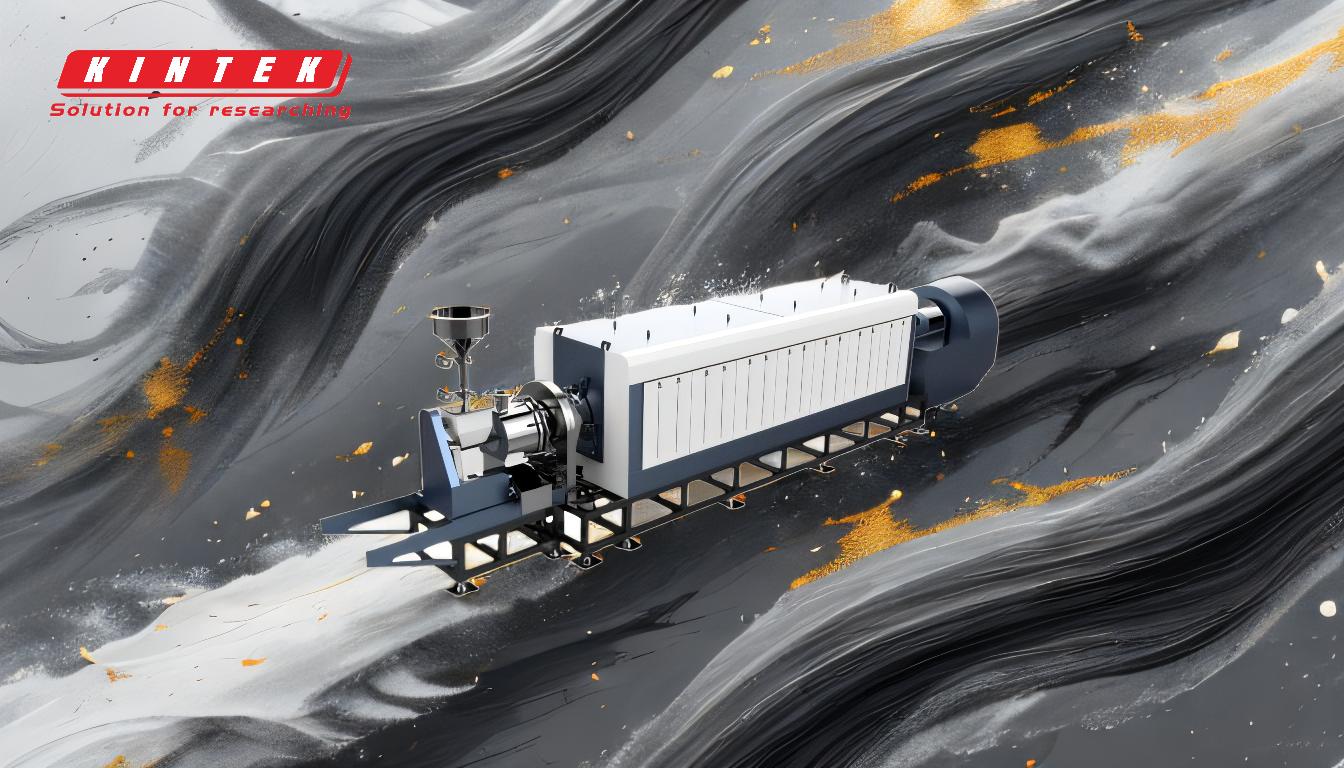
-
Definition and Mechanism of Pyrolysis:
- Pyrolysis is a thermochemical decomposition process that occurs at elevated temperatures (typically above 430°C) in the absence of oxygen.
- It breaks down organic materials into smaller molecules, resulting in products like bio-oil, biochar, and gases.
- The process is irreversible and involves simultaneous physical and chemical changes.
-
Operating Conditions and Their Impact:
- Temperature: Varies depending on the type of pyrolysis. Flash pyrolysis operates at 800–1000°C, while slow pyrolysis occurs at around 500°C.
- Heating Rate: Flash pyrolysis has extremely high heating rates (>1000°C/s), whereas slow pyrolysis has low rates (0.1–2°C/s).
- Residence Time: Flash pyrolysis has short residence times (<5 s), while slow pyrolysis can have residence times ranging from minutes to days.
- Feedstock Size: Smaller feedstock sizes (<0.2 mm) are typically used in flash pyrolysis to ensure rapid and uniform heating.
-
Types of Pyrolysis:
-
Flash Pyrolysis:
- High temperatures (800–1000°C) and heating rates (>1000°C/s).
- Short vapor residence times (<5 s).
- Produces high bio-oil yields (~75%), with smaller amounts of biochar (~12%) and gases (~13%).
-
Fast Pyrolysis:
- Moderate temperatures (400–600°C) and heating rates (10–200°C/s).
- Short residence times (0.5–10 s).
- Yields bio-oil (50–70 wt%) and biogas.
-
Slow Pyrolysis:
- Low temperatures (around 500°C) and slow heating rates (0.1–2°C/s).
- Long residence times (minutes to days).
- Produces biochar and tar as major products.
-
Flash Pyrolysis:
-
Product Yields and Composition:
- Bio-oil: A liquid product rich in organic compounds, primarily produced in flash and fast pyrolysis.
- Biochar: A solid residue rich in carbon, mainly produced in slow pyrolysis.
- Gases: Includes combustible gases like methane and hydrogen, produced in varying amounts across all pyrolysis types.
-
Applications and Significance:
- Pyrolysis is used for converting biomass and waste materials into valuable energy products.
- It is an environmentally friendly method for waste management, reducing landfill use and greenhouse gas emissions.
- The process can be tailored to maximize specific products (e.g., bio-oil for fuel or biochar for soil amendment) by adjusting operating conditions.
-
Comparison of Pyrolysis Types:
- Flash vs. Fast Pyrolysis: Flash pyrolysis operates at higher temperatures and heating rates, resulting in higher bio-oil yields compared to fast pyrolysis.
- Slow vs. Fast Pyrolysis: Slow pyrolysis emphasizes biochar production due to long residence times, while fast pyrolysis focuses on bio-oil and biogas.
By understanding these properties, stakeholders can select the appropriate pyrolysis method and conditions to achieve desired outcomes, whether for energy generation, waste reduction, or material recovery.
Summary Table:
Type of Pyrolysis | Temperature Range | Heating Rate | Residence Time | Primary Products |
---|---|---|---|---|
Flash Pyrolysis | 800–1000°C | >1000°C/s | <5 s | Bio-oil (~75%) |
Fast Pyrolysis | 400–600°C | 10–200°C/s | 0.5–10 s | Bio-oil (50–70 wt%) |
Slow Pyrolysis | ~500°C | 0.1–2°C/s | Minutes to days | Biochar and tar |
Ready to optimize your pyrolysis process? Contact our experts today for tailored solutions!