Physical vapor deposition (PVD) is a widely used technique in various industries for coating materials with thin films. It offers several advantages, such as high deposition rates, excellent film quality, and environmental friendliness. However, it also has drawbacks, including high costs, complexity, and the need for vacuum conditions. Understanding the pros and cons of PVD is essential for making informed decisions in applications ranging from manufacturing to research.
Key Points Explained:
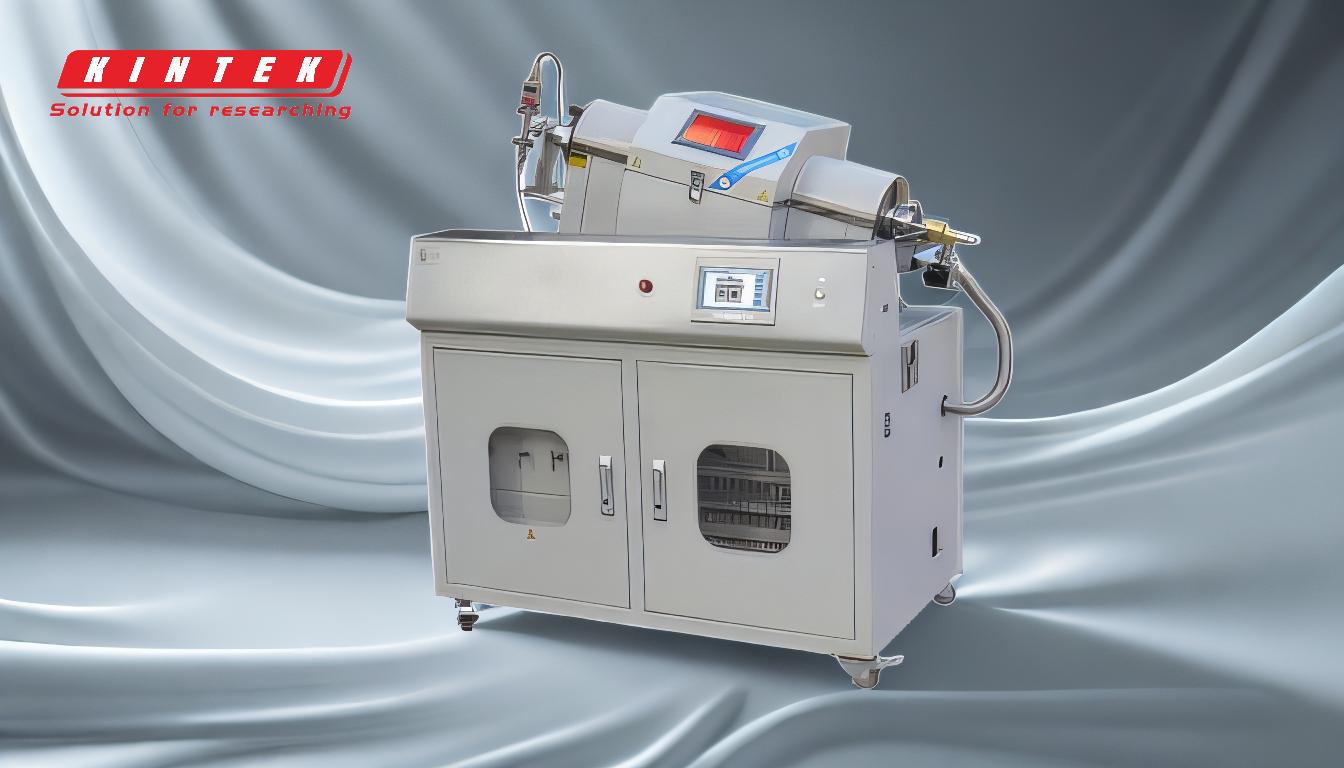
-
Advantages of PVD:
- High Deposition Rate and Sample Utilization: PVD methods, such as evaporation and sputtering, provide a high deposition rate and efficient use of materials. This makes them suitable for applications requiring rapid and precise coating.
- Superior Film Quality and Uniformity: Techniques like ion beam sputtering produce films with excellent quality and uniformity, which can lead to higher yields in manufacturing processes.
- Corrosion and Wear Resistance: PVD coatings enhance the chemical and wear resistance of products, making them more durable and extending their lifespan. They also offer a wide range of colors, adding aesthetic value.
- Environmentally Friendly: PVD is considered an environmentally sound process, as it does not involve harmful chemicals and produces minimal waste.
-
Disadvantages of PVD:
- High Cost and Complexity: PVD processes, particularly those requiring vacuum conditions, are more expensive and complex compared to other deposition methods like chemical vapor deposition (CVD). The need for specialized equipment and skilled operators adds to the overall cost.
- Time-Consuming: The requirement for vacuum conditions makes PVD more time-consuming, which can be a drawback in high-throughput manufacturing environments.
- Limited Substrate Compatibility: PVD is less suitable for temperature-sensitive materials, as the process can involve high temperatures that may damage such substrates.
-
Comparison with CVD:
- Selectivity and Conformality: CVD offers better selectivity and conformality, allowing for uniform coverage of rough surfaces and selective deposition on specific regions of the substrate. This makes CVD more versatile in certain applications.
- Thermal Constraints: CVD requires high temperatures (up to 900 °C), which limits its use with temperature-sensitive materials. PVD, on the other hand, can be used with a broader range of substrates, including those that cannot withstand high temperatures.
- Batch Processing: CVD can process larger batches of substrates, making it more efficient for high-volume production. PVD, while suitable for both large-scale and small batch production, may not match CVD's efficiency in batch processing.
-
Operational Considerations:
- Automation and Control: PVD coating machines are often computer-controlled, allowing operators to multitask and reducing production costs and turnaround time. This automation enhances the efficiency of the PVD process.
- Material Waste: CVD typically results in less material waste since only the heated area is coated. PVD, while efficient, may not match CVD in terms of material utilization, especially when selective heating is required.
In summary, PVD offers significant advantages in terms of film quality, environmental friendliness, and durability, making it a preferred choice for many industrial applications. However, its high cost, complexity, and time-consuming nature are notable drawbacks. When compared to CVD, PVD excels in certain areas but falls short in others, particularly in terms of selectivity and batch processing efficiency. Understanding these pros and cons is crucial for selecting the appropriate deposition method based on specific application requirements.
Summary Table:
Aspect | Pros | Cons |
---|---|---|
Deposition Rate | High deposition rate and efficient material utilization | High cost and complexity due to vacuum conditions |
Film Quality | Superior film quality and uniformity | Time-consuming process |
Durability | Enhanced corrosion and wear resistance | Limited compatibility with temperature-sensitive materials |
Environmental Impact | Environmentally friendly, minimal waste | |
Automation | Computer-controlled, reduces production costs and turnaround time | Material waste may be higher compared to CVD |
Need help choosing the right deposition method for your application? Contact our experts today for tailored solutions!