When selecting a heat treatment furnace, it is essential to evaluate several critical factors to ensure the furnace meets the specific needs of the application. These factors include temperature range, material compatibility, furnace configuration, production volume, and safety requirements. The furnace must align with the material's heat treatment requirements, such as achieving the desired physiochemical properties. Additionally, operational efficiency, automation capabilities, and environmental considerations play a significant role in the selection process. By carefully assessing these parameters, users can choose a furnace that ensures optimal performance, safety, and cost-effectiveness.
Key Points Explained:
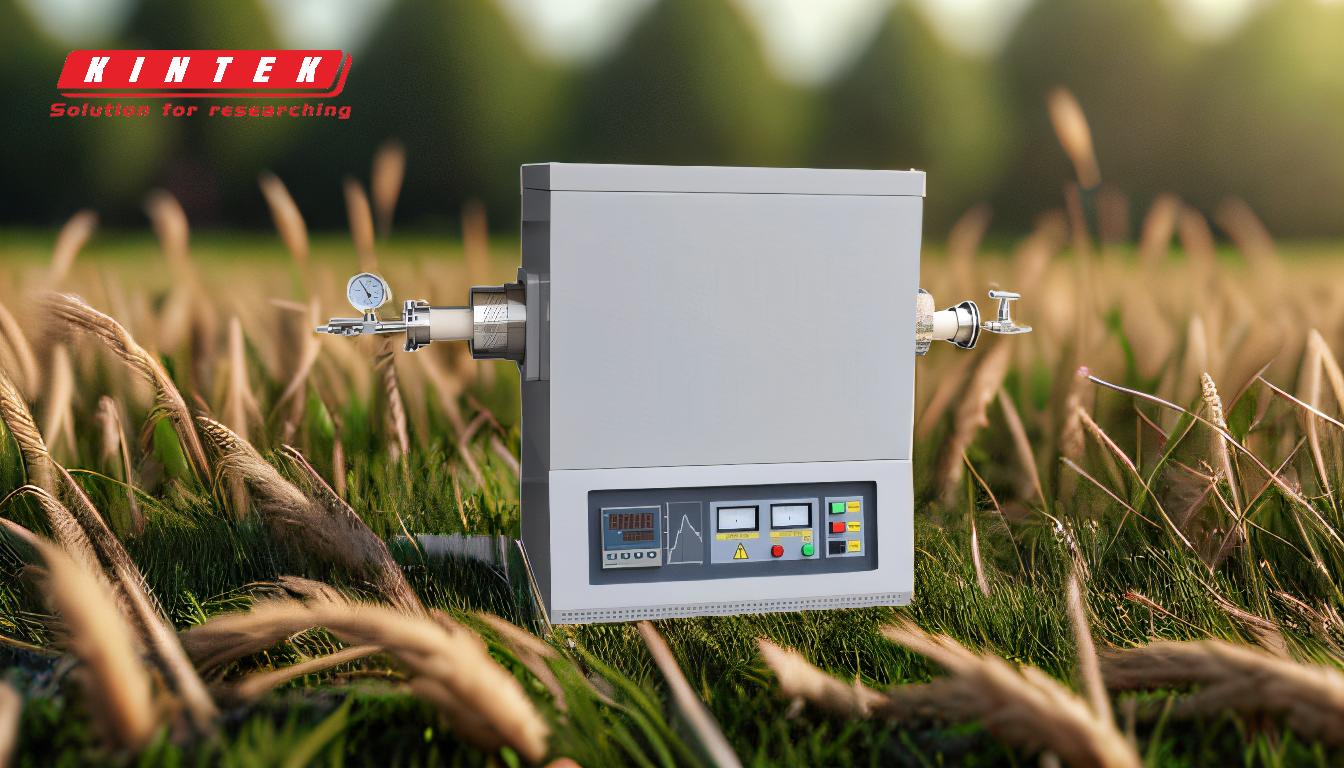
-
Temperature Range
- The heat treatment furnace must operate within the required temperature range for the specific application. This ensures the material undergoes the necessary transformations, such as hardening, annealing, or tempering.
- For example, high-temperature furnaces are needed for processes like sintering zirconia restorations, while lower temperatures may suffice for annealing metals.
-
Material Compatibility
- The furnace must be compatible with the materials being processed. This includes resistance to chemical reactions, thermal expansion, and wear.
- For instance, a furnace used for heat-treating ceramics must withstand high temperatures without degrading, while one for metals should prevent oxidation.
-
Furnace Configuration
- The configuration of the furnace (e.g., box, tube, or vacuum) should match the application requirements. Each type has unique advantages:
- Box furnaces are ideal for batch processing.
- Tube furnaces are suitable for continuous processes or controlled atmospheres.
- Vacuum furnaces are used when oxidation or contamination must be minimized.
- The configuration of the furnace (e.g., box, tube, or vacuum) should match the application requirements. Each type has unique advantages:
-
Production Volume
- The furnace's capacity must align with the production volume. High-volume operations may require larger or automated furnaces, while smaller-scale labs can use compact models.
- Automation capabilities, such as pre-programmed cycles, can enhance efficiency for repetitive tasks.
-
Safety and Environmental Considerations
- Safety measures, such as proper ventilation and temperature control, are critical to prevent accidents.
- Environmental factors, like the need for inert gases or vacuum conditions, must also be considered to ensure compliance with safety and regulatory standards.
-
Operational Efficiency
- Factors such as heating time, energy consumption, and maintenance requirements impact the furnace's overall efficiency.
- Advanced features like programmable controls and energy-efficient designs can reduce operational costs and improve performance.
-
Specific Application Requirements
- The furnace must meet the unique needs of the application, such as uniform temperature distribution, precise control, or compatibility with process gases.
- For example, a furnace used in a laboratory setting may require precise temperature control and compatibility with inert gases, while an industrial furnace may prioritize durability and high throughput.
By carefully evaluating these factors, users can select a heat treatment furnace that ensures optimal results, operational efficiency, and safety.
Summary Table:
Factor | Description |
---|---|
Temperature Range | Must match the application's required range for processes like hardening or annealing. |
Material Compatibility | Ensure resistance to chemical reactions, thermal expansion, and wear. |
Furnace Configuration | Choose between box, tube, or vacuum furnaces based on application needs. |
Production Volume | Align furnace capacity with production scale; automation enhances efficiency. |
Safety & Environmental | Proper ventilation, inert gases, and compliance with safety standards are vital. |
Operational Efficiency | Consider heating time, energy use, and maintenance for cost-effectiveness. |
Application Requirements | Ensure uniform temperature, precise control, and compatibility with process gases. |
Need help selecting the right heat treatment furnace? Contact our experts today for personalized advice!