Sintering, a process used to create solid materials from powders by applying heat, carries several risks that can affect both the quality of the final product and the safety of the environment and personnel involved. These risks include material defects such as warping and sagging, inconsistent results due to challenges in controlling process parameters, and health hazards from toxic fumes and nanoparticles. Additionally, environmental concerns arise from harmful emissions, prompting regulatory measures that can impact production rates. Proper handling, ventilation, and adherence to safety protocols are essential to mitigate these risks.
Key Points Explained:
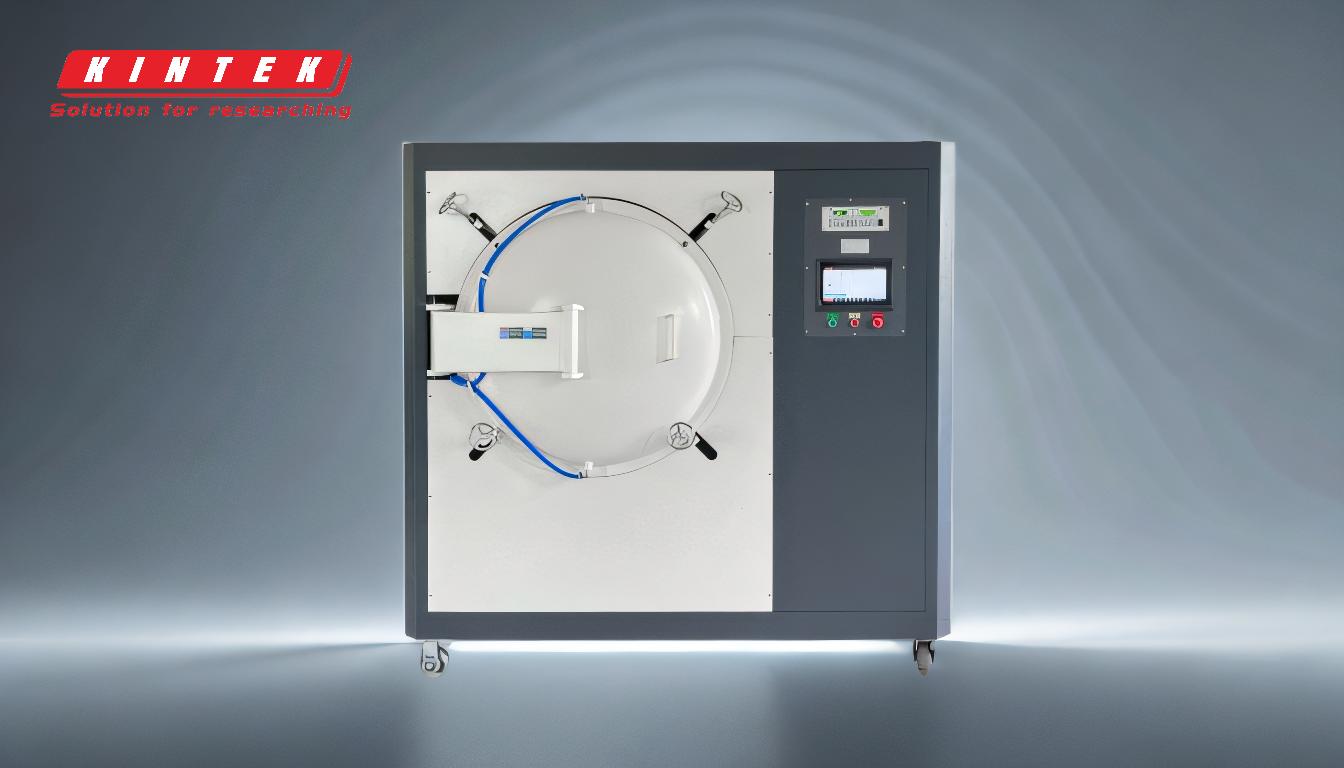
-
Material Defects:
- Warping and Sagging: During sintering, parts can warp due to gravity or friction, and sagging can occur, leading to defects in the final product. These issues can compromise the structural integrity and dimensional accuracy of the sintered parts.
- Inconsistent Results: Variability in sintering conditions, such as temperature and pressure, can result in inconsistent material properties and defects, affecting the performance and reliability of the final product.
-
Health Hazards:
- Toxic Fumes: The high temperatures involved in sintering can produce toxic and irritant fumes, which pose health risks to workers. Proper ventilation and safety equipment are necessary to protect personnel from inhalation of harmful substances.
- Nanoparticles: Metal and ceramic nanoparticles used in sintering can have medical consequences if inhaled or ingested. Handling these materials requires stringent safety measures to prevent exposure and potential health issues.
-
Environmental Concerns:
- Harmful Emissions: Sintering processes can release harmful emissions into the environment, contributing to air pollution. This has led to the implementation of governmental regulations and norms aimed at controlling and reducing these emissions.
- Regulatory Impact: Compliance with environmental regulations can affect the production rate and cost of sintered parts. Manufacturers may need to invest in cleaner technologies and processes to meet these standards, impacting overall productivity and profitability.
-
Process Control Challenges:
- Parameter Management: Achieving consistent results in sintering requires precise control over process parameters such as temperature, pressure, and time. Variations in these parameters can lead to defects and inconsistencies, necessitating advanced monitoring and control systems.
- Equipment Maintenance: Regular maintenance of sintering equipment is crucial to ensure consistent performance and prevent unexpected failures that could lead to production delays and quality issues.
By understanding and addressing these risks, manufacturers can improve the quality and safety of sintered products while minimizing environmental impact. Implementing robust safety protocols, investing in advanced control systems, and adhering to regulatory requirements are essential steps in mitigating the risks associated with sintering.
Summary Table:
Risk Category | Key Risks |
---|---|
Material Defects | - Warping and sagging affect structural integrity and dimensional accuracy. |
- Inconsistent results due to variability in temperature and pressure. | |
Health Hazards | - Toxic fumes from high temperatures pose inhalation risks. |
- Nanoparticles can cause medical issues if inhaled or ingested. | |
Environmental Concerns | - Harmful emissions contribute to air pollution. |
- Regulatory compliance impacts production rates and costs. | |
Process Control Challenges | - Precise control of temperature, pressure, and time is essential. |
- Regular equipment maintenance prevents production delays. |
Ensure your sintering process is safe and efficient—contact our experts today for tailored solutions!