The sieving method, while widely used for particle size analysis, is subject to several sources of error that can affect the accuracy and reliability of the results. These errors can arise from various factors, including environmental conditions, equipment issues, sample preparation, and human error. Understanding these sources of error is crucial for ensuring accurate measurements and improving the reliability of the sieving process.
Key Points Explained:
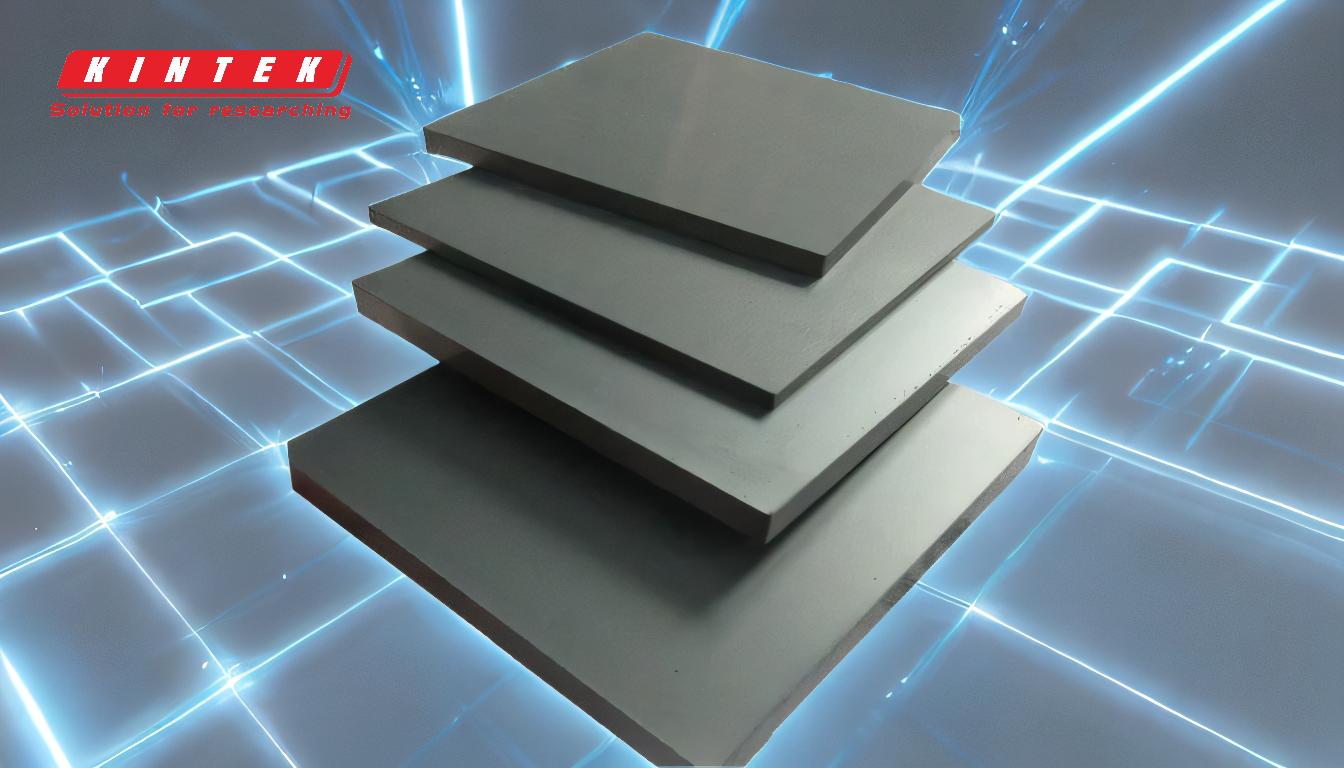
-
Environmental Conditions:
- Relative Humidity: Changes in relative humidity can significantly impact the sieving process. For instance, extremely dry conditions can cause fine powders to adhere to the sieve components and each other due to strong electrostatic charges. This can lead to inaccurate particle size distribution results as some particles may not pass through the sieve as they should.
- Temperature: Fluctuations in temperature can also affect the sieving process. Materials may expand or contract with temperature changes, potentially altering their size and the way they interact with the sieve.
-
Equipment Issues:
- Sieve Wear and Tear: Over time, sieves can become worn or damaged, leading to changes in the size of the openings. This can result in inaccurate particle size measurements.
- Sieve Clogging: Particles can become lodged in the sieve openings, reducing the effective size of the openings and preventing other particles from passing through. This can lead to an overestimation of the particle size.
- Sieve Calibration: If sieves are not properly calibrated, the measurements will be inaccurate. Regular calibration is essential to ensure that the sieve openings are the correct size.
-
Sample Preparation:
- Sample Size: Using too much or too little sample can affect the accuracy of the sieving process. An excessive sample size can lead to overloading the sieve, while too little sample may not provide a representative measurement.
- Sample Moisture Content: The moisture content of the sample can also impact the sieving process. Wet or damp samples may clump together, making it difficult for particles to pass through the sieve openings.
- Sample Agglomeration: Particles may agglomerate or stick together, especially in the presence of moisture or electrostatic charges. This can lead to inaccurate particle size distribution results.
-
Human Error:
- Inconsistent Sieving Technique: The way the sieve is handled during the sieving process can introduce errors. Inconsistent shaking or tapping can lead to variations in the results.
- Incorrect Sieve Stacking: The order in which sieves are stacked can affect the outcome. If sieves are not stacked in the correct order (from largest to smallest opening), particles may not be properly separated.
- Measurement Errors: Errors can occur when measuring the weight of the material retained on each sieve. Inaccurate weighing can lead to incorrect particle size distribution calculations.
-
Material Characteristics:
- Particle Shape: The shape of the particles can affect how they pass through the sieve openings. Irregularly shaped particles may not pass through the sieve as easily as spherical particles, leading to inaccurate results.
- Particle Density: Differences in particle density can also impact the sieving process. Denser particles may settle differently on the sieve, affecting the distribution of particle sizes.
-
Duration of Sieving:
- Insufficient Sieving Time: If the sieving process is not carried out for a sufficient amount of time, some particles may not have the opportunity to pass through the sieve openings. This can lead to an underestimation of the finer particle sizes.
- Excessive Sieving Time: Conversely, excessive sieving time can cause particles to break down or abrade, leading to an overestimation of the finer particle sizes.
By understanding and mitigating these sources of error, it is possible to improve the accuracy and reliability of the sieving method. Regular calibration of equipment, careful sample preparation, and consistent sieving techniques are essential steps in minimizing these errors.
Summary Table:
Source of Error | Key Factors |
---|---|
Environmental Conditions | Relative humidity, temperature fluctuations |
Equipment Issues | Sieve wear and tear, clogging, calibration errors |
Sample Preparation | Sample size, moisture content, agglomeration |
Human Error | Inconsistent technique, incorrect stacking, measurement errors |
Material Characteristics | Particle shape, density |
Duration of Sieving | Insufficient or excessive sieving time |
Ensure accurate particle size analysis—contact our experts today for guidance on minimizing sieving errors!