Spark plasma sintering (SPS) is an advanced sintering technique that utilizes pulsed direct current (DC) and uniaxial pressure to achieve rapid densification of powder materials. The process typically involves three or four stages, depending on the classification. The primary stages include gas removal and vacuum creation, application of pressure, resistance heating (plasma and joule heating), and cooling. These stages work together to facilitate rapid heating, particle bonding, and densification at lower temperatures compared to conventional sintering methods. The process is highly efficient, allowing for the production of dense and homogeneous bulk materials with minimal grain growth.
Key Points Explained:
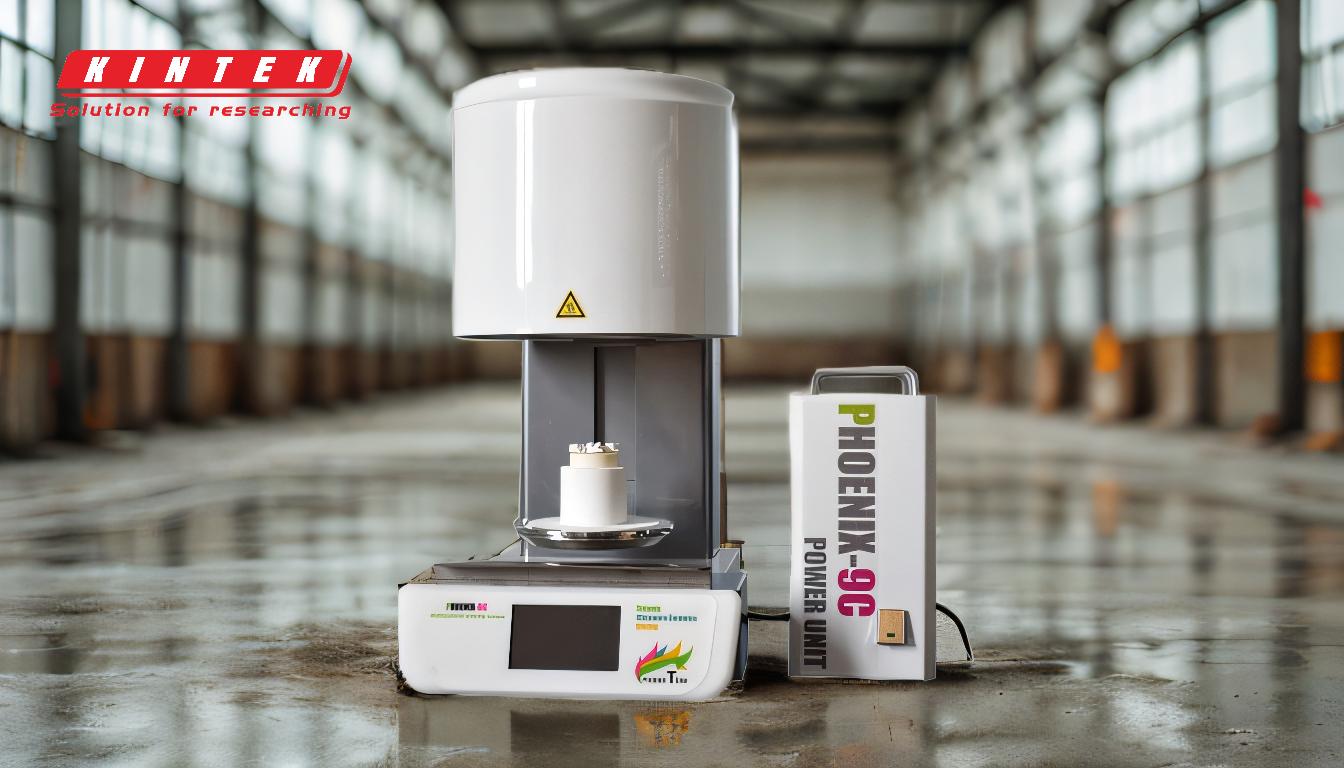
-
Gas Removal and Vacuum Creation
- This initial stage involves removing gases and creating a vacuum within the sintering chamber.
- Purpose: Eliminates oxygen and other gases that could oxidize the powder or interfere with the sintering process.
- Process: The chamber is evacuated to a low atmospheric pressure, ensuring a controlled environment for sintering.
- Importance: Prevents contamination and ensures the purity of the final product.
-
Application of Pressure
- Uniaxial pressure is applied to the powder within the die.
- Purpose: Compacts the powder particles, reducing gaps between them and promoting particle-to-particle contact.
- Process: A hydraulic or mechanical system applies pressure through punches, ensuring uniform compaction.
- Importance: Enhances densification by facilitating particle rearrangement and plastic deformation.
-
Resistance Heating (Plasma and Joule Heating)
- This stage involves the application of pulsed DC current, which generates heat through plasma and joule heating mechanisms.
-
Plasma Heating:
- Pulsed DC creates localized high temperatures and plasma discharges between particles.
- Effect: Melts particle surfaces, promoting surface diffusion and bonding.
-
Joule Heating:
- Electrical current flows through the conductive die and, if applicable, the sample itself.
- Effect: Generates internal heat, enabling rapid and uniform heating of the material.
- Importance: Allows for rapid sintering at lower temperatures, minimizing grain growth and preserving material properties.
-
Cooling Stage
- After sintering, the material is cooled under controlled conditions.
- Purpose: Solidifies the sintered material and stabilizes its microstructure.
- Process: Cooling rates can be adjusted to achieve desired material properties.
- Importance: Prevents thermal stress and ensures the final product has the desired density and mechanical properties.
-
Key Advantages of SPS
- Rapid Heating and Cooling: Enables shorter processing times compared to conventional sintering.
- Lower Sintering Temperatures: Reduces energy consumption and minimizes thermal damage to the material.
- Enhanced Densification: Produces materials with high density and minimal porosity.
- Grain Size Control: Prevents excessive grain growth, preserving fine-grained microstructures.
-
Applications of SPS
- Advanced Ceramics: Used for sintering ceramics with high strength and thermal stability.
- Metals and Alloys: Produces dense metallic components with tailored properties.
- Composites: Enables the fabrication of composite materials with uniform dispersion of phases.
- Nanomaterials: Preserves nanostructures due to low sintering temperatures and short processing times.
By understanding these stages, equipment and consumable purchasers can better evaluate the requirements for SPS systems, including die materials (e.g., graphite), heating elements, and vacuum systems. This knowledge also aids in selecting appropriate powders and optimizing process parameters for specific applications.
Summary Table:
Stage | Purpose | Process | Importance |
---|---|---|---|
Gas Removal & Vacuum Creation | Eliminates gases to prevent oxidation and contamination. | Chamber evacuated to low atmospheric pressure. | Ensures a controlled environment and purity of the final product. |
Application of Pressure | Compacts powder particles for better contact and densification. | Hydraulic or mechanical system applies uniform pressure through punches. | Enhances particle rearrangement and plastic deformation. |
Resistance Heating | Generates heat via plasma and joule heating for rapid sintering. | Pulsed DC creates localized high temperatures and internal heat through the conductive die. | Enables rapid sintering at lower temperatures, preserving material properties. |
Cooling Stage | Solidifies the material and stabilizes its microstructure. | Controlled cooling rates to achieve desired properties. | Prevents thermal stress and ensures optimal density and mechanical properties. |
Key Advantages | Rapid heating/cooling, lower sintering temperatures, enhanced densification. | Shorter processing times, energy efficiency, and minimal grain growth. | Produces dense, homogeneous materials with fine-grained microstructures. |
Applications | Advanced ceramics, metals/alloys, composites, nanomaterials. | Fabricates high-strength ceramics, dense metals, uniform composites, and preserved nanostructures. | Tailored material properties for diverse industrial and research applications. |
Ready to explore how Spark Plasma Sintering can revolutionize your material processing? Contact our experts today for tailored solutions!