Additive manufacturing, commonly known as 3D printing, is a transformative approach to industrial production that enables the creation of lighter, stronger parts and systems. The process involves several key steps, from the initial design to the final product. Each step is crucial and requires careful attention to detail to ensure the quality and functionality of the printed object. The steps generally include designing the 3D model, preparing the model for printing, selecting the appropriate materials and printing technology, executing the print, and post-processing the printed object.
Key Points Explained:
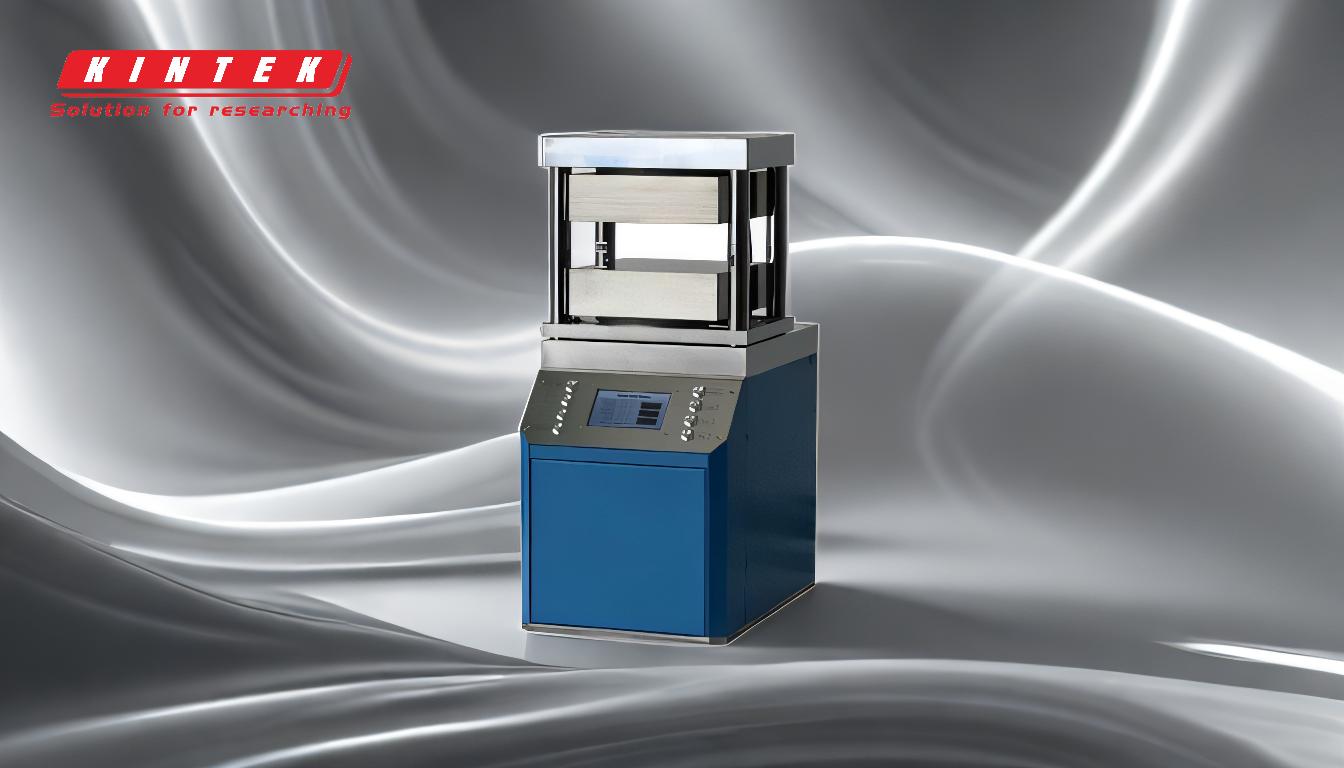
-
Designing the 3D Model:
- The first step in additive manufacturing is creating a digital 3D model of the object to be printed. This is typically done using Computer-Aided Design (CAD) software. The design must consider the physical properties and the intended use of the final product.
- The complexity of the design can vary widely, from simple shapes to complex geometries that would be difficult or impossible to achieve with traditional manufacturing methods.
-
Preparing the Model for Printing:
- Once the 3D model is created, it must be converted into a format that the 3D printer can understand. This usually involves slicing the model into thin, horizontal layers using specialized software.
- The slicing process also allows for the adjustment of various settings such as layer thickness, infill density, and support structures, which are crucial for the structural integrity of the final product.
-
Selecting Materials and Printing Technology:
- The choice of material and printing technology depends on the desired properties of the final product, such as strength, flexibility, thermal resistance, and aesthetic qualities.
- Common materials include plastics, resins, metals, and ceramics. Each material may require a different type of 3D printing technology, such as Fused Deposition Modeling (FDM), Stereolithography (SLA), or Selective Laser Sintering (SLS).
-
Executing the Print:
- With the model prepared and materials selected, the actual printing process begins. The 3D printer builds the object layer by layer, following the instructions from the sliced model.
- This step requires precise control over the printing environment, including temperature and humidity, to ensure the material properties are maintained throughout the process.
-
Post-Processing:
- After printing, the object often requires post-processing to improve its mechanical properties and surface finish. This can include removing support structures, sanding, painting, or applying heat treatments.
- Post-processing is crucial for achieving the desired final characteristics of the product and can significantly affect its performance and appearance.
Each of these steps is integral to the additive manufacturing process, and understanding them is essential for anyone involved in the production of 3D printed objects. By carefully managing each phase, manufacturers can optimize the quality and efficiency of their products, leveraging the unique capabilities of 3D printing technology.
Summary Table:
Step | Description |
---|---|
1. Designing the 3D Model | Create a digital 3D model using CAD software, considering physical properties. |
2. Preparing the Model | Slice the model into layers and adjust settings like infill density and supports. |
3. Selecting Materials | Choose materials (plastics, metals, etc.) and printing technology (FDM, SLA, SLS). |
4. Executing the Print | Build the object layer by layer with precise environmental control. |
5. Post-Processing | Improve properties and finish through sanding, painting, or heat treatments. |
Ready to optimize your 3D printing process? Contact our experts today for tailored solutions!