Graphite is a versatile material widely used in various industrial applications, including furnace chambers, due to its unique properties such as low density, high thermal conductivity, and excellent emissivity. The manufacturing process of graphite involves several critical steps, each contributing to the material's final quality and performance. Below is a detailed explanation of the steps involved in graphite manufacturing, with a focus on its application in furnace chambers.
Key Points Explained:
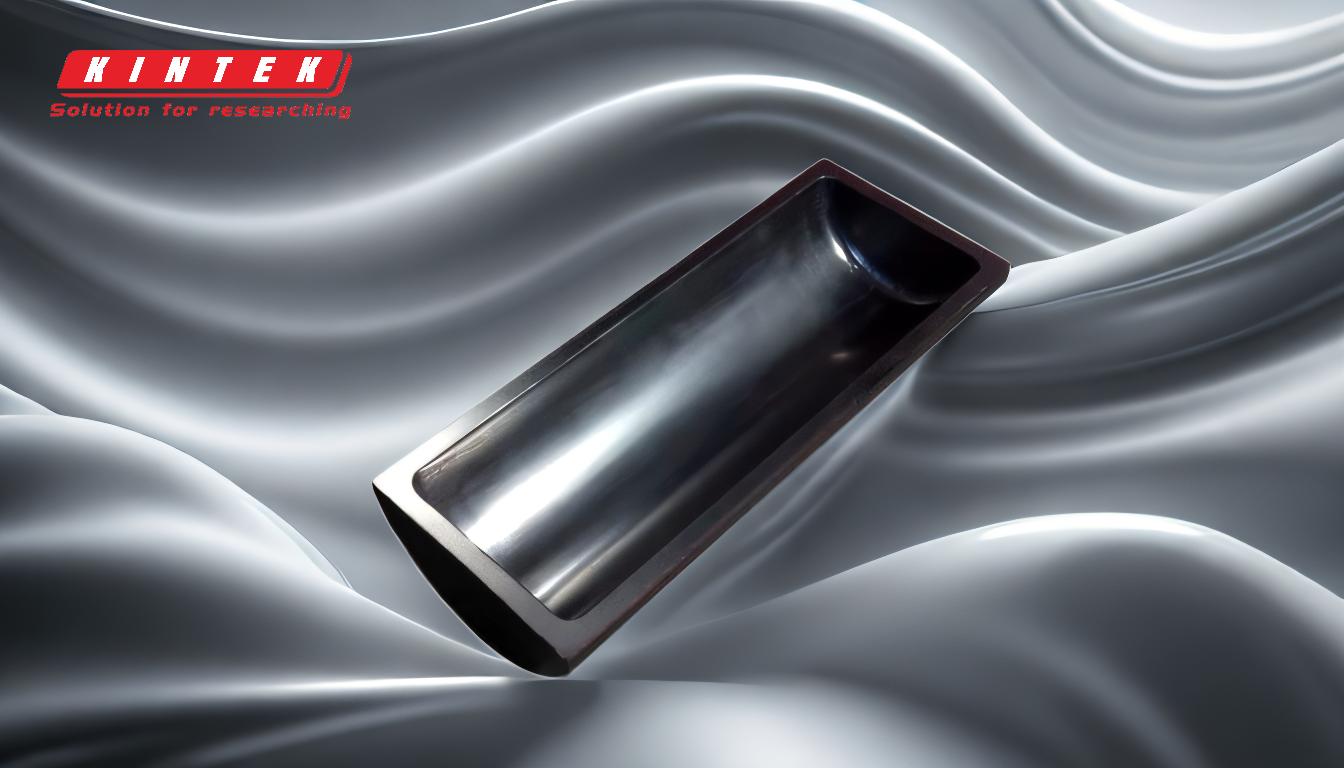
-
Raw Material Selection:
- The first step in graphite manufacturing is selecting high-quality raw materials. Typically, petroleum coke or coal tar pitch is used as the primary carbon source. These materials are chosen for their high carbon content and purity, which are essential for producing high-performance graphite.
-
Calcination:
- The selected raw materials undergo calcination, a process where they are heated to high temperatures (around 1200°C to 1400°C) in the absence of oxygen. This step removes volatile components and moisture, resulting in a more stable and pure carbon material. Calcination is crucial for ensuring the structural integrity and thermal stability of the final graphite product.
-
Mixing and Forming:
- After calcination, the carbon material is mixed with a binder, usually coal tar pitch, to form a homogeneous mixture. This mixture is then shaped into the desired form using various techniques such as extrusion, molding, or isostatic pressing. The forming process is critical for achieving the required density and mechanical strength of the graphite.
-
Baking:
- The formed carbon shapes are baked in a graphite furnace at temperatures ranging from 800°C to 1000°C. Baking helps to carbonize the binder, transforming it into a solid carbon matrix that binds the carbon particles together. This step is essential for developing the initial structural properties of the graphite.
-
Impregnation:
- To enhance the density and mechanical properties, the baked carbon shapes are often impregnated with additional carbonaceous materials. This involves soaking the shapes in a liquid pitch or resin and then re-baking them. Impregnation can be repeated multiple times to achieve the desired properties.
-
Graphitization:
- The final and most critical step is graphitization, where the carbon shapes are heated to extremely high temperatures (up to 3000°C) in an inert atmosphere. This process transforms the amorphous carbon into crystalline graphite, significantly improving its thermal and electrical conductivity, as well as its mechanical strength. Graphitization is what gives graphite its unique properties, making it ideal for use in furnace chambers.
-
Machining and Finishing:
- After graphitization, the graphite blocks are machined to the precise dimensions required for their specific applications. This includes cutting, drilling, and surface finishing to ensure a perfect fit and optimal performance in furnace chambers.
-
Quality Control and Testing:
- The final step involves rigorous quality control and testing to ensure the graphite meets the required specifications. This includes testing for density, porosity, thermal conductivity, and mechanical strength. Only after passing these tests is the graphite deemed ready for use in furnace chambers.
By following these steps, manufacturers can produce high-quality graphite that is well-suited for use in furnace chambers, offering excellent thermal performance, durability, and ease of repair. The unique properties of graphite, such as its low density and high emissivity, make it an ideal material for creating efficient and long-lasting furnace chambers.
Summary Table:
Step | Description |
---|---|
Raw Material Selection | High-quality petroleum coke or coal tar pitch is chosen for high carbon content. |
Calcination | Heating raw materials to 1200°C–1400°C to remove volatiles and moisture. |
Mixing and Forming | Carbon material is mixed with a binder and shaped using extrusion or molding. |
Baking | Shapes are baked at 800°C–1000°C to carbonize the binder. |
Impregnation | Shapes are soaked in pitch/resin and re-baked to enhance density. |
Graphitization | Heated to 3000°C to transform amorphous carbon into crystalline graphite. |
Machining and Finishing | Blocks are cut, drilled, and finished to precise dimensions. |
Quality Control | Rigorous testing for density, porosity, thermal conductivity, and strength. |
Need high-quality graphite for your furnace chambers? Contact our experts today to learn more!