Thin film formation is a critical process in materials science and engineering, involving the deposition of thin layers of material onto a substrate. This process is essential for modifying surface properties and achieving desired characteristics such as conductivity, wear resistance, and corrosion protection. The steps in thin film formation can vary depending on the specific deposition technique used, but generally include material selection, substrate preparation, deposition, and post-deposition treatments. Each step is crucial for ensuring the quality and performance of the thin film.
Key Points Explained:
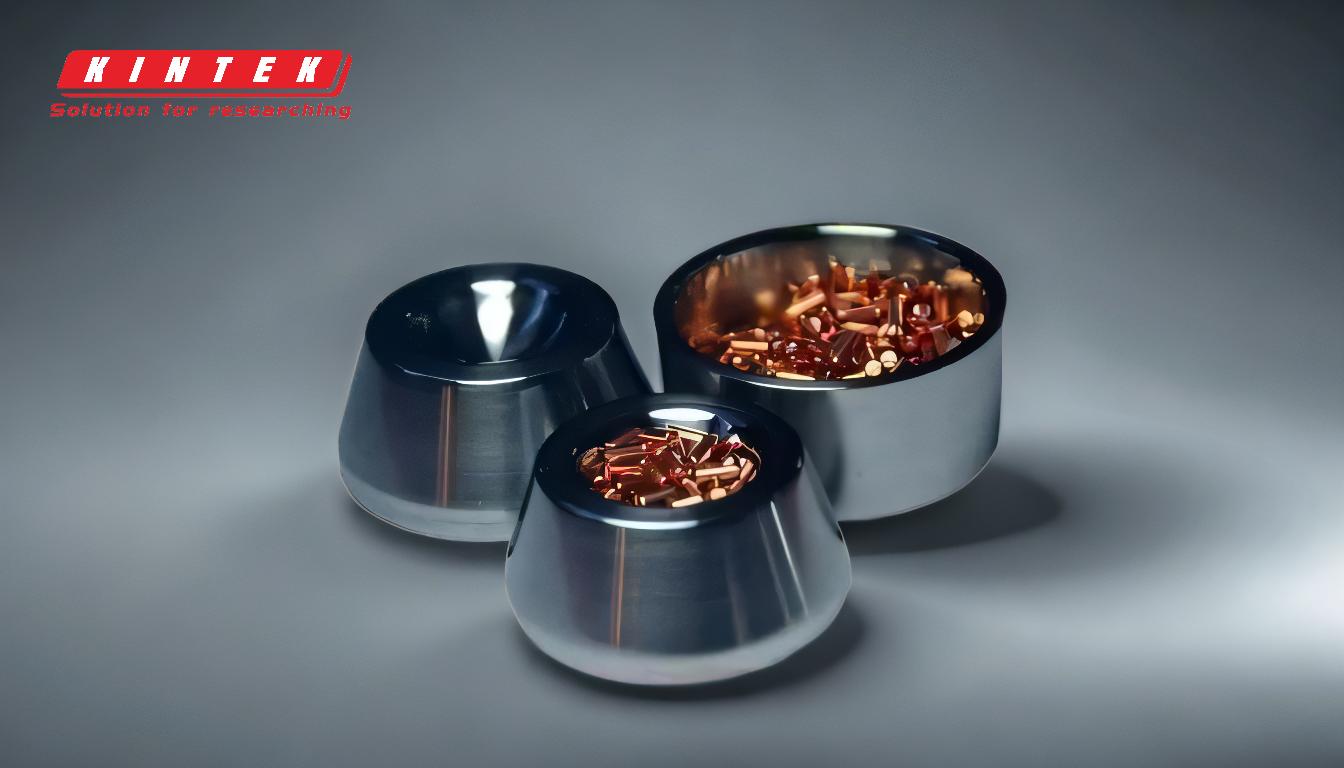
-
Material Selection:
- Purpose: Choosing the right material is fundamental to achieving the desired properties of the thin film.
- Process: The material, often referred to as the target, must be pure and suitable for the intended application. The selection depends on the required characteristics such as conductivity, hardness, or optical properties.
- Considerations: Factors like material compatibility with the substrate, deposition method, and final application requirements are critical.
-
Substrate Preparation:
- Purpose: Preparing the substrate ensures proper adhesion and uniformity of the thin film.
- Process: This involves cleaning the substrate to remove any contaminants and sometimes modifying the surface to enhance adhesion. Techniques include chemical cleaning, mechanical polishing, and surface activation.
- Considerations: The substrate's surface roughness, cleanliness, and chemical composition can significantly impact the film's quality.
-
Deposition:
- Purpose: The core step where the thin film is formed on the substrate.
-
Process: Various deposition techniques are used, including:
- Thermal Evaporation: Heating the target material until it vaporizes and then condenses on the substrate.
- Sputtering: Bombarding the target with ions to eject atoms that then deposit on the substrate.
- Chemical Vapor Deposition (CVD): Using chemical reactions to produce a film on the substrate.
- Ion Beam Deposition: Directing a beam of ions to deposit material on the substrate.
- Considerations: Parameters like temperature, pressure, and deposition rate must be carefully controlled to achieve the desired film properties.
-
Post-Deposition Treatments:
- Purpose: Enhancing the film's properties and stability.
-
Process: Common treatments include:
- Annealing: Heating the film to relieve stresses and improve crystallinity.
- Heat Treatment: Modifying the film's microstructure to enhance properties like hardness or electrical conductivity.
- Considerations: The treatment conditions must be optimized to avoid damaging the film or substrate.
-
Analysis and Quality Control:
- Purpose: Ensuring the film meets the required specifications.
-
Process: Various analytical techniques are used to assess the film's properties, such as thickness, uniformity, adhesion, and chemical composition. Techniques include:
- Ellipsometry: Measuring film thickness and optical properties.
- X-ray Diffraction (XRD): Analyzing crystallographic structure.
- Scanning Electron Microscopy (SEM): Examining surface morphology.
- Considerations: Continuous monitoring and feedback are essential for process optimization and consistency.
-
Process Optimization:
- Purpose: Refining the deposition process to improve film quality and performance.
- Process: Based on the analysis results, adjustments are made to deposition parameters, substrate preparation, or post-deposition treatments.
- Considerations: Iterative testing and refinement are necessary to achieve the optimal balance of film properties and process efficiency.
By following these steps meticulously, manufacturers can produce thin films with precise properties tailored to specific applications, ensuring high performance and reliability in various engineering and technological fields.
Summary Table:
Step | Purpose | Key Considerations |
---|---|---|
Material Selection | Choose the right material for desired properties (e.g., conductivity, hardness). | Material compatibility, deposition method, and application requirements. |
Substrate Preparation | Ensure proper adhesion and uniformity of the thin film. | Surface roughness, cleanliness, and chemical composition of the substrate. |
Deposition | Form the thin film on the substrate using techniques like sputtering or CVD. | Control temperature, pressure, and deposition rate for optimal film properties. |
Post-Deposition Treatments | Enhance film properties and stability through annealing or heat treatment. | Optimize treatment conditions to avoid damaging the film or substrate. |
Analysis and Quality Control | Ensure the film meets required specifications. | Use techniques like ellipsometry, XRD, and SEM for thickness, uniformity, and adhesion. |
Process Optimization | Refine the process for improved film quality and performance. | Iterative testing and adjustments based on analysis results. |
Ready to optimize your thin film formation process? Contact our experts today for tailored solutions!