Vapor phase deposition techniques are essential in creating thin films and coatings for various applications, including electronics, optics, and protective coatings. These techniques are broadly categorized into Physical Vapor Deposition (PVD) and Chemical Vapor Deposition (CVD). PVD methods, such as thermal evaporation and sputtering, involve physically transferring material from a source to a substrate, while CVD relies on chemical reactions to deposit materials. Each method has unique advantages, such as high purity, uniformity, and strong adhesion, making them suitable for specific applications.
Key Points Explained:
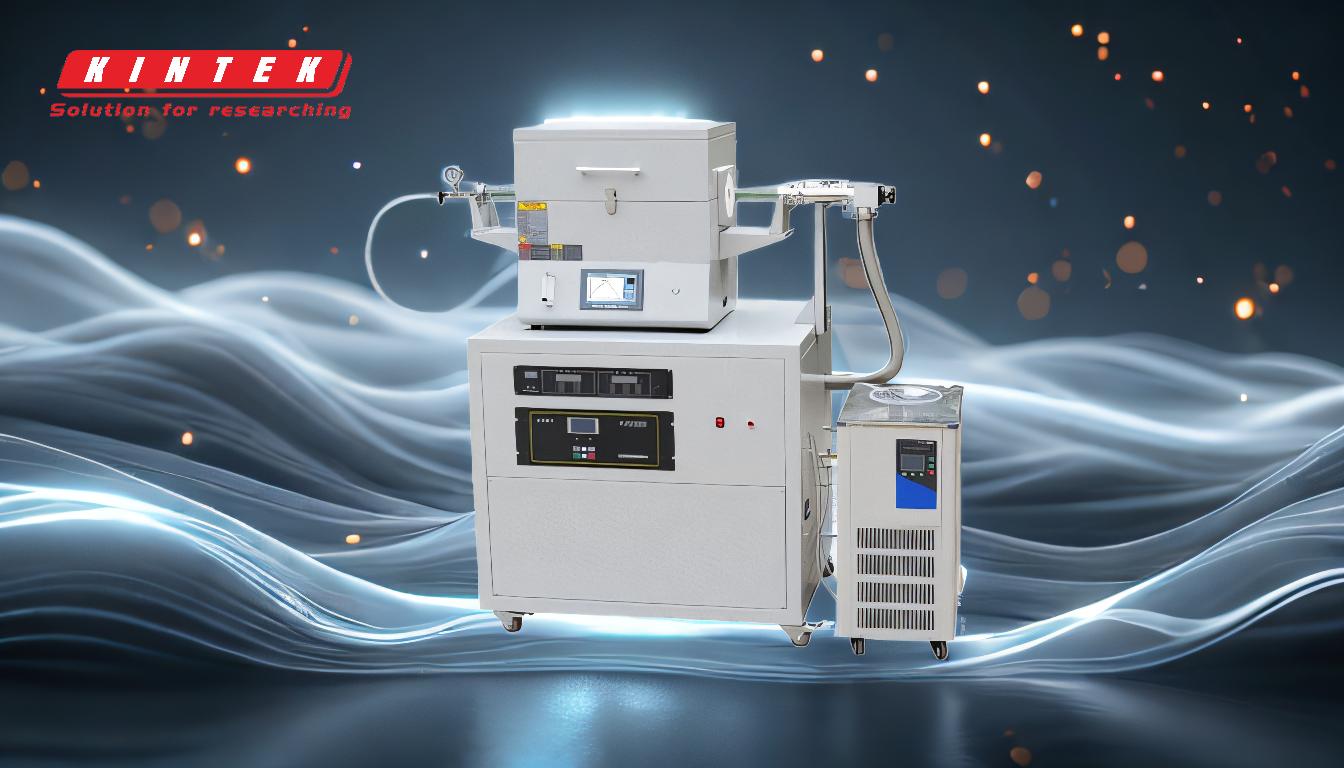
-
Physical Vapor Deposition (PVD):
- Thermal Evaporation: This technique involves heating a material until it vaporizes in a vacuum chamber. The vapor then condenses on a substrate, forming a thin film. It is commonly used for materials with low melting points and is known for producing high-purity films.
- Sputtering: In this process, high-energy ions bombard a target material, ejecting atoms into the gas phase. These atoms are then deposited onto a substrate. Sputtering is widely used for depositing metals, alloys, and compounds, offering excellent film uniformity and adhesion.
- Electron Beam Evaporation: A high-energy electron beam is used to vaporize the source material. This method is suitable for materials with high melting points and provides precise control over film thickness.
-
Chemical Vapor Deposition (CVD):
- CVD Process: This technique involves chemical reactions between gaseous precursors to form a solid film on a substrate. The chemical vapor deposition machine is a key tool in this process, enabling precise control over deposition conditions. CVD is widely used for depositing high-quality, conformal films, especially in semiconductor manufacturing.
- Plasma-Enhanced CVD (PECVD): This variant uses plasma to enhance chemical reactions at lower temperatures, making it suitable for temperature-sensitive substrates.
- Atomic Layer Deposition (ALD): ALD is a subset of CVD that deposits films one atomic layer at a time, offering exceptional control over film thickness and uniformity. It is ideal for applications requiring ultra-thin, conformal coatings.
-
Other Techniques:
- Molecular Beam Epitaxy (MBE): A specialized form of PVD, MBE is used to grow high-quality crystalline films. It is commonly employed in semiconductor research and production.
- Spray Pyrolysis: This method involves spraying a solution onto a heated substrate, where it decomposes to form a thin film. It is cost-effective and suitable for large-area coatings.
-
Applications and Advantages:
- High Purity and Uniformity: Both PVD and CVD techniques produce films with high purity and uniformity, making them ideal for applications in electronics, optics, and protective coatings.
- Strong Adhesion: These methods ensure strong adhesion between the film and the substrate, enhancing durability and performance.
- Versatility: Vapor phase deposition techniques can be tailored to deposit a wide range of materials, including metals, ceramics, and polymers, on various substrates.
By understanding the principles and applications of these techniques, manufacturers and researchers can select the most appropriate method for their specific needs, ensuring optimal performance and quality in their thin film applications.
Summary Table:
Technique | Key Methods | Advantages | Applications |
---|---|---|---|
Physical Vapor Deposition (PVD) | Thermal Evaporation, Sputtering, Electron Beam Evaporation | High purity, uniformity, strong adhesion | Electronics, optics, protective coatings |
Chemical Vapor Deposition (CVD) | CVD, PECVD, ALD | High-quality, conformal films, precise control | Semiconductor manufacturing, thin films |
Other Techniques | MBE, Spray Pyrolysis | Cost-effective, large-area coatings | Research, large-scale production |
Need help choosing the right vapor phase deposition technique? Contact our experts today for tailored solutions!