Thin film deposition is a critical process in nanotechnology, enabling the creation of ultra-thin layers of material that are essential for various applications, such as integrated circuits, solar cells, and optical coatings. The techniques used for thin film deposition can be broadly categorized into physical vapor deposition (PVD) and chemical vapor deposition (CVD). PVD methods include evaporation and sputtering, while CVD involves chemical reactions to form thin films. Specific techniques like magnetron sputtering, electron beam evaporation, ion beam sputtering, and atomic layer deposition (ALD) are widely used due to their precision, ability to produce high-purity coatings, and suitability for nanoscale applications. These methods are chosen based on the desired material properties, substrate type, and application requirements.
Key Points Explained:
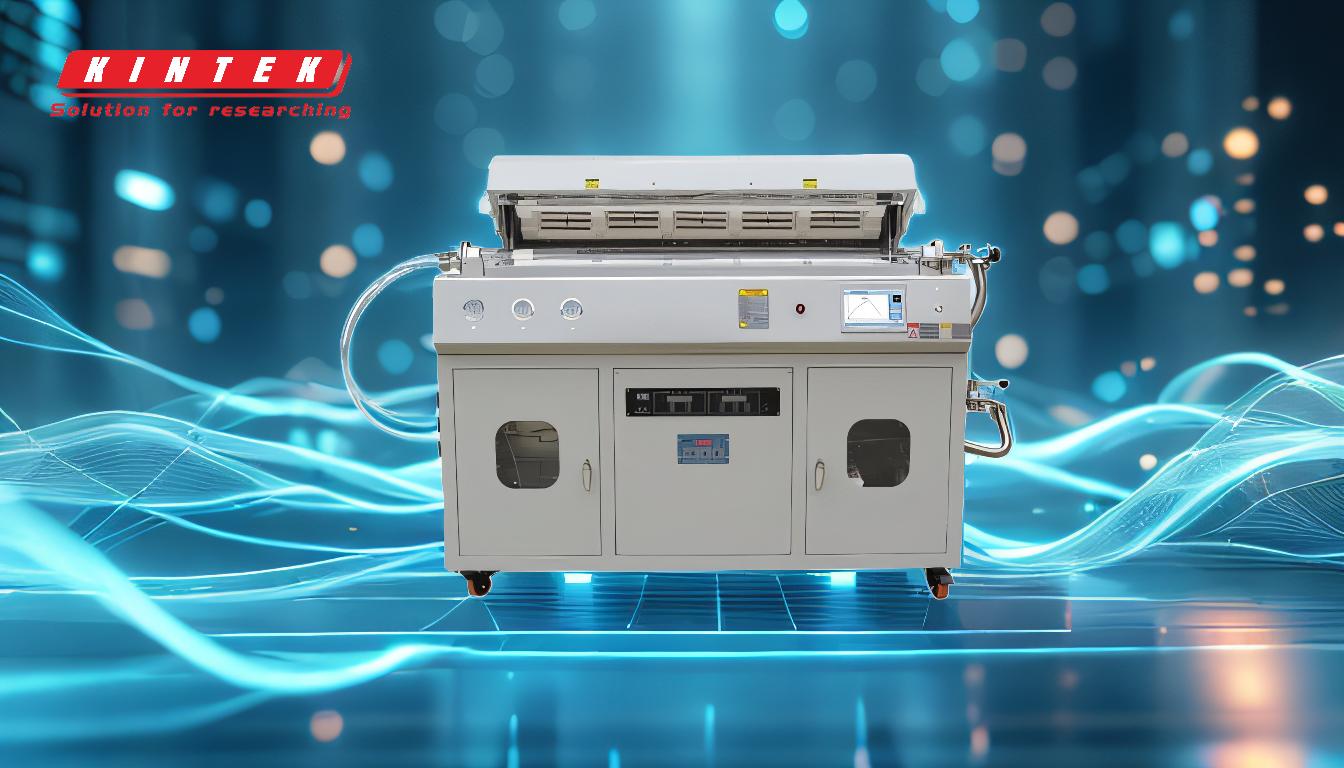
-
Physical Vapor Deposition (PVD):
- Definition: PVD involves the vaporization of a solid material in a vacuum, which is then deposited onto a substrate to form a thin film.
-
Techniques:
- Evaporation: This method uses heat to vaporize the material, which then condenses on the substrate. Electron beam evaporation is a common variant, where an electron beam is used to heat the material.
- Sputtering: In sputtering, high-energy ions bombard a target material, causing atoms to be ejected and deposited onto the substrate. Magnetron sputtering is a popular technique due to its ability to produce high-purity films with low defect levels.
- Applications: PVD is used in applications requiring high-purity films, such as optical coatings, micro-electromechanical systems (MEMS), and integrated circuits.
-
Chemical Vapor Deposition (CVD):
- Definition: CVD involves the use of chemical reactions to produce thin films. Precursor gases react on the substrate surface to form the desired material.
-
Techniques:
- Standard CVD: This involves the reaction of gases at high temperatures to deposit a thin film.
- Atomic Layer Deposition (ALD): ALD is a more precise form of CVD where thin films are deposited one atomic layer at a time, allowing for extremely controlled thickness and uniformity.
- Applications: CVD is widely used in the growth of carbon nanotubes, the creation of magnetic coatings for hard drives, and the production of thin-film solar cells.
-
Magnetron Sputtering:
- Process: Magnetron sputtering uses a magnetic field to confine electrons near the target material, increasing the efficiency of the sputtering process. This results in higher deposition rates and better film quality.
- Advantages: It produces high-purity coatings with low levels of defects, making it suitable for applications in nanotechnology, such as the fabrication of integrated circuits and optical coatings.
- Applications: Commonly used in the production of thin films for micro-fabricated mechanisms, light-emitting diodes (LEDs), and photovoltaic solar cells.
-
Electron Beam Evaporation:
- Process: In this technique, an electron beam is directed at the target material, causing it to vaporize and deposit onto the substrate.
- Advantages: It allows for the deposition of high-purity materials with precise control over thickness.
- Applications: Used in the production of thin films for optical coatings, semiconductor devices, and thin-film batteries.
-
Ion Beam Sputtering:
- Process: Ion beam sputtering involves directing a beam of ions at the target material, causing atoms to be ejected and deposited onto the substrate.
- Advantages: It provides excellent control over film thickness and uniformity, making it ideal for high-precision applications.
- Applications: Used in the fabrication of thin films for advanced optical coatings and nanotechnology applications.
-
Atomic Layer Deposition (ALD):
- Process: ALD is a cyclic process where thin films are deposited one atomic layer at a time through sequential, self-limiting chemical reactions.
- Advantages: It offers unparalleled control over film thickness and uniformity, making it ideal for nanoscale applications.
- Applications: Used in the growth of carbon nanotubes, the creation of magnetic coatings, and the production of thin-film transistors.
-
Applications of Thin Film Deposition in Nanotechnology:
- Integrated Circuits: Thin films are essential for the fabrication of integrated circuits, where they are used to create conductive, insulating, and semiconducting layers.
- Micro-Electromechanical Systems (MEMS): Thin films are used in MEMS devices to create mechanical and electrical components on a microscale.
- Optical Coatings: Thin films are used to create anti-reflective coatings, mirrors, and filters for optical devices.
- Photovoltaic Solar Cells: Thin films are used to create the active layers in solar cells, improving their efficiency and reducing costs.
- Thin-Film Batteries: Thin films are used to create the electrodes and electrolytes in thin-film batteries, enabling compact and flexible energy storage solutions.
In conclusion, thin film deposition techniques are essential for the advancement of nanotechnology, enabling the creation of materials and devices with precise control over their properties. The choice of deposition method depends on the specific requirements of the application, with each technique offering unique advantages in terms of purity, thickness control, and scalability.
Summary Table:
Technique | Key Features | Applications |
---|---|---|
Physical Vapor Deposition (PVD) | Vaporization of solid material in a vacuum; includes evaporation and sputtering. | Optical coatings, MEMS, integrated circuits. |
Chemical Vapor Deposition (CVD) | Chemical reactions to form thin films; includes standard CVD and ALD. | Carbon nanotubes, magnetic coatings, thin-film solar cells. |
Magnetron Sputtering | Uses magnetic fields for high-purity, low-defect coatings. | Integrated circuits, LEDs, photovoltaic solar cells. |
Electron Beam Evaporation | Electron beam heats material for precise, high-purity deposition. | Optical coatings, semiconductor devices, thin-film batteries. |
Ion Beam Sputtering | Ion beam ejects target material for high-precision coatings. | Advanced optical coatings, nanotechnology applications. |
Atomic Layer Deposition (ALD) | Deposits films one atomic layer at a time for ultimate precision. | Carbon nanotubes, magnetic coatings, thin-film transistors. |
Ready to enhance your nanotechnology projects with advanced thin film deposition techniques? Contact our experts today to learn more!