The sintering process is a critical step in manufacturing, particularly in powder metallurgy and ceramics, where materials are transformed into dense, cohesive structures without reaching their melting points. The process is typically divided into three main stages: composing the sintering powder, compacting the powder into a desired shape, and heating the compacted material in a sintering furnace to facilitate particle bonding and densification. Each stage plays a vital role in achieving the final product's mechanical properties, structural integrity, and dimensional accuracy. Understanding these stages helps in optimizing the sintering process for various industrial applications.
Key Points Explained:
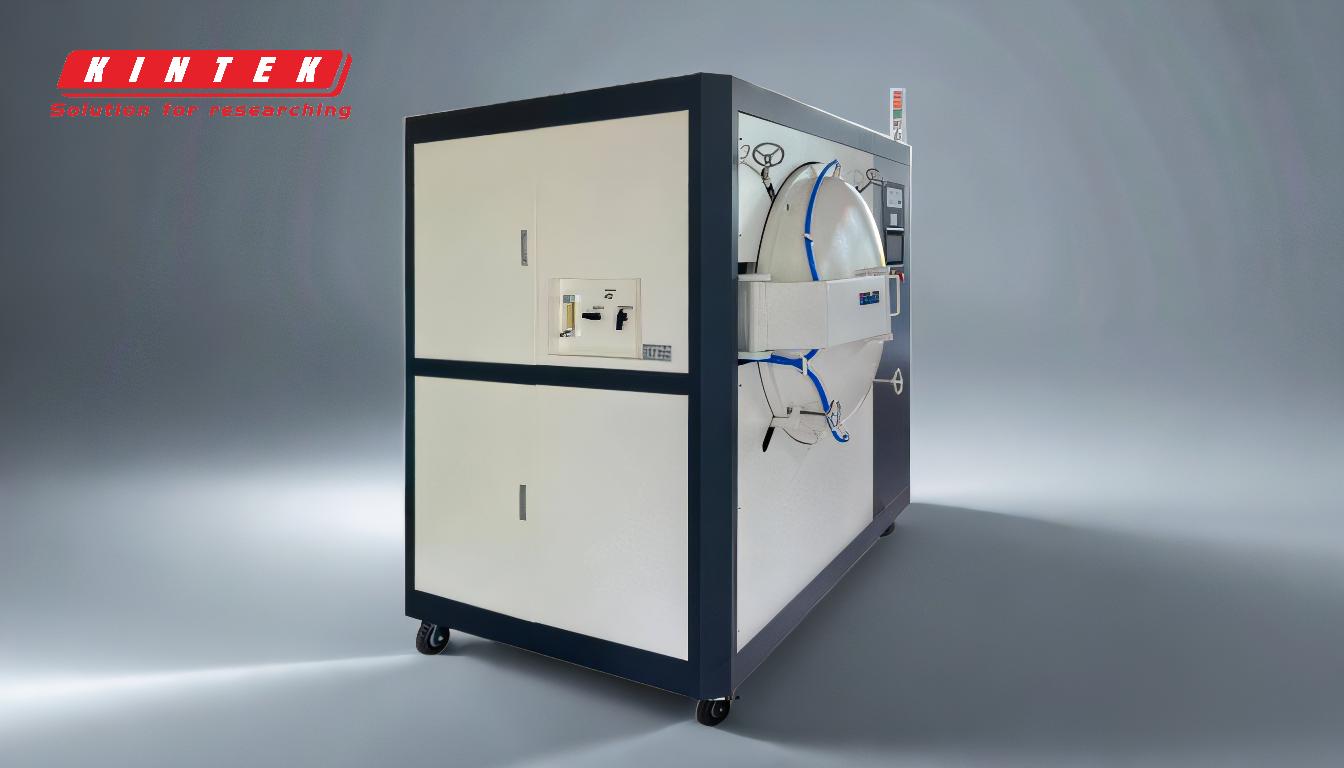
-
Composing the Sintering Powder:
- This initial stage involves selecting and mixing the raw materials, often in powdered form, to create a homogeneous blend. The composition may include primary materials, alloying elements, and additives to achieve specific properties.
- The goal is to ensure uniformity in the powder mixture, which is crucial for consistent results in the subsequent stages. Proper mixing techniques and equipment are employed to avoid segregation or uneven distribution of components.
- For example, in metal sintering, powdered metals are blended with alloying elements to enhance strength, corrosion resistance, or other desired characteristics.
-
Compacting the Powder:
- Once the powder is prepared, it is compacted into the desired shape using high-pressure tools or molds. This step is essential for eliminating voids and ensuring the material has sufficient green strength to maintain its shape during handling and sintering.
- The compaction process can be performed at room temperature or under heated conditions, depending on the material and application. The pressure applied must be carefully controlled to achieve uniform density throughout the compacted part.
- This stage often involves the use of hydraulic or mechanical presses, and the design of the mold or die must account for any shrinkage that may occur during sintering.
-
Heating in a Sintering Furnace:
- The compacted material is then subjected to controlled heating in a sintering furnace. The temperature is carefully regulated to facilitate particle bonding through diffusion without causing complete melting.
- During this stage, particles undergo neck formation, where they begin to bond at contact points, leading to densification and reduced porosity. The duration and temperature of heating depend on the material and desired properties.
- After sintering, the product is cooled gradually to solidify into a rigid and cohesive structure. This cooling process is critical to prevent thermal stresses and ensure dimensional stability.
By understanding and optimizing these three stages, manufacturers can produce high-quality sintered products with tailored properties for various applications, from automotive components to advanced ceramics.
Summary Table:
Stage | Description | Key Considerations |
---|---|---|
Composing the Powder | Selecting and mixing raw materials to create a homogeneous blend. | Uniformity, proper mixing techniques, and avoiding segregation are crucial. |
Compacting the Powder | Pressing the powder into a desired shape using high-pressure tools or molds. | Controlled pressure, uniform density, and accounting for shrinkage are essential. |
Heating in a Furnace | Heating the compacted material in a sintering furnace to bond particles. | Controlled temperature, neck formation, and gradual cooling ensure structural integrity. |
Optimize your sintering process today—contact our experts for tailored solutions!