The sintering cycle in powder metallurgy is a critical process that transforms metal powders into a cohesive, durable final product. While references vary slightly in their descriptions, the core steps can be distilled into three main stages: powder compaction, sintering (heating), and cooling. These stages ensure the material achieves the desired density, strength, and structural integrity. Below, we explore these steps in detail, focusing on their purpose, mechanisms, and outcomes.
Key Points Explained:
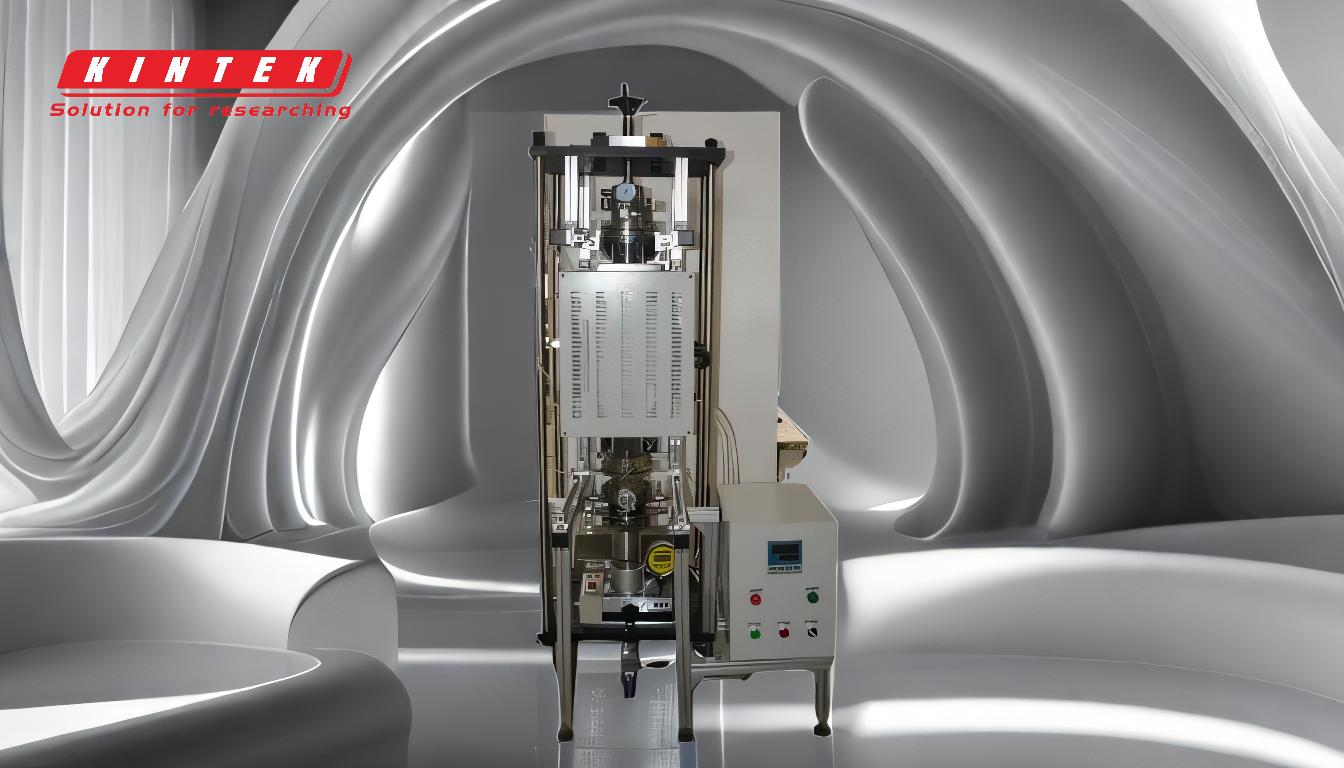
-
Powder Compaction
- Purpose: To shape the metal powder into a preliminary form (green part) with sufficient strength for handling and sintering.
-
Process:
- Metal powders are placed into a die and subjected to high pressure, typically using a hydraulic or mechanical press.
- The pressure compacts the powder, reducing voids and increasing particle contact.
- The resulting "green part" has a porous structure but is cohesive enough to maintain its shape.
-
Considerations:
- The choice of powder composition (e.g., alloy type, particle size) directly affects the compaction process and final product properties.
- Proper compaction ensures uniform density, which is critical for consistent sintering results.
-
Sintering (Heating)
- Purpose: To bond the compacted powder particles into a solid, dense structure through controlled heating.
-
Process:
- The green part is heated in a sintering furnace to a temperature just below the melting point of the metal.
- During heating, atomic diffusion occurs, causing particles to bond at their contact points (neck formation).
- The material undergoes densification as pores shrink and particles merge.
-
Mechanisms:
- Initial Stage: Particles begin to bond, and surface diffusion reduces porosity.
- Intermediate Stage: Particle density increases, and grain boundaries form.
- Final Stage: The structure becomes mostly solid, with minimal porosity and high mechanical strength.
-
Considerations:
- Temperature and time are carefully controlled to prevent melting or warping.
- Sintering atmosphere (e.g., hydrogen, nitrogen, or vacuum) is critical to avoid oxidation and ensure proper bonding.
-
Cooling
- Purpose: To solidify the sintered material into its final form while maintaining structural integrity.
-
Process:
- The sintered part is gradually cooled in a controlled environment to prevent thermal stress or cracking.
- Cooling rates vary depending on the material and desired properties (e.g., faster cooling for higher hardness).
-
Outcome:
- The final product achieves its intended mechanical properties, such as strength, hardness, and dimensional stability.
- Any remaining porosity is minimized, and the material is ready for finishing processes if required.
-
Considerations:
- Cooling must be uniform to avoid distortion or residual stresses.
- Post-sintering treatments (e.g., heat treatment, surface finishing) may be applied to enhance performance.
Summary of the Sintering Cycle:
- Powder Compaction: Metal powders are pressed into a preliminary shape, creating a green part with sufficient cohesion.
- Sintering (Heating): The green part is heated to bond particles, reduce porosity, and achieve densification.
- Cooling: The sintered part is cooled to solidify its structure and finalize its mechanical properties.
Each step is interdependent, and careful control of parameters (e.g., pressure, temperature, cooling rate) ensures the production of high-quality sintered components. Understanding these stages is essential for optimizing the sintering process and achieving the desired material properties.
Summary Table:
Stage | Purpose | Key Processes |
---|---|---|
Powder Compaction | Shape metal powder into a preliminary form (green part) for handling. | High-pressure compaction using hydraulic/mechanical press; reduces voids, increases particle contact. |
Sintering (Heating) | Bond particles into a solid, dense structure through controlled heating. | Heating below melting point; atomic diffusion, neck formation, and densification. |
Cooling | Solidify the sintered material while maintaining structural integrity. | Gradual cooling in a controlled environment; minimizes porosity and thermal stress. |
Optimize your sintering process with expert guidance—contact us today!