Physical Vapor Deposition (PVD) is a widely used technique for depositing thin films of materials onto substrates in a vacuum environment. The process involves vaporizing a solid material and then condensing it onto a substrate to form a thin film. The three primary types of PVD are Evaporation, Sputtering, and Ion Plating. Each method has unique mechanisms and applications, making them suitable for different industrial and scientific purposes.
Key Points Explained:
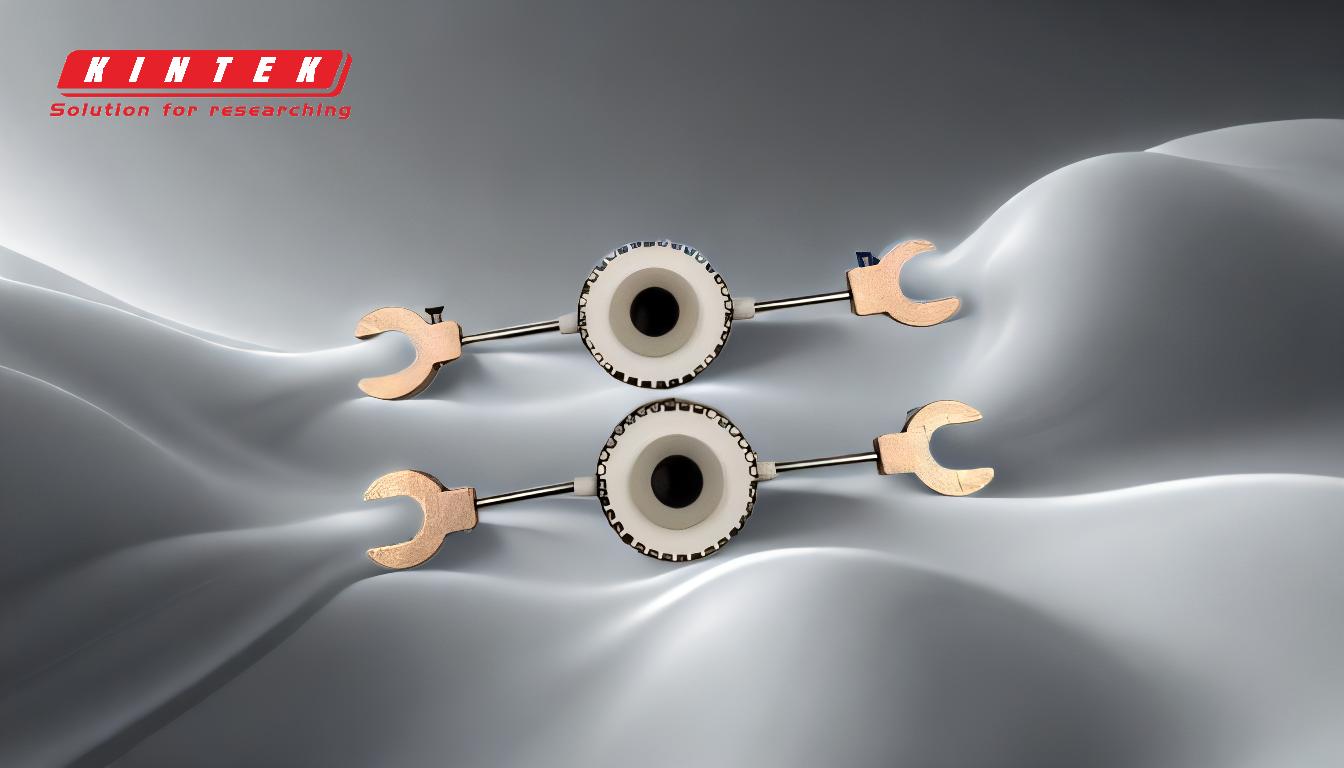
-
Evaporation:
- Mechanism: In this process, the material to be deposited is heated to its vaporization point in a vacuum chamber. The vaporized atoms or molecules then travel through the vacuum and condense on the cooler substrate, forming a thin film.
-
Types:
- Thermal Evaporation: Uses resistive heating to vaporize the material.
- Electron-Beam (E-Beam) Evaporation: Uses a focused electron beam to heat and vaporize the material, allowing for higher melting point materials to be deposited.
- Applications: Commonly used in optical coatings, semiconductor devices, and decorative coatings.
- Advantages: High deposition rates, good purity of films, and relatively simple equipment.
- Limitations: Limited to materials with lower melting points in thermal evaporation, and line-of-sight deposition can lead to uneven coatings on complex geometries.
-
Sputtering:
- Mechanism: Sputtering involves bombarding a target material with high-energy ions (usually argon) in a vacuum. The impact of these ions knocks atoms off the target, which then deposit onto the substrate.
-
Types:
- DC Sputtering: Uses a direct current (DC) power source to generate the plasma.
- RF Sputtering: Uses radio frequency (RF) power, suitable for insulating materials.
- Magnetron Sputtering: Incorporates a magnetic field to enhance the ionization of the gas, increasing the deposition rate and efficiency.
- Applications: Widely used in the semiconductor industry, thin-film solar cells, and hard coatings for tools.
- Advantages: Can deposit a wide range of materials, including metals, alloys, and ceramics. Provides good adhesion and uniformity.
- Limitations: Lower deposition rates compared to evaporation, and the process can be more complex and costly.
-
Ion Plating:
- Mechanism: Combines elements of both evaporation and sputtering. The material is vaporized (often through evaporation), and then ionized gas (plasma) is used to enhance the deposition process. The ions in the plasma help to improve the adhesion and density of the deposited film.
- Applications: Used for wear-resistant coatings, decorative finishes, and in the aerospace industry.
- Advantages: Produces highly adherent and dense coatings, suitable for complex geometries.
- Limitations: More complex equipment and process control are required, and the process can be slower than other PVD methods.
Additional Considerations:
- Microwave Plasma Chemical Vapor Deposition (MPCVD): While not a type of PVD, it's worth noting that microwave plasma chemical vapor deposition is a related technique used for depositing diamond films. In MPCVD, gases like CH4 and H2 are ionized using microwaves to create a plasma, which then reacts with a substrate to grow diamond films. This method is distinct from PVD but shares some similarities in terms of vacuum-based deposition.
In summary, the three main types of PVD—Evaporation, Sputtering, and Ion Plating—each offer unique advantages and are chosen based on the specific requirements of the application. Understanding these methods allows for the selection of the most appropriate technique to achieve desired film properties and performance.
Summary Table:
Type | Mechanism | Applications | Advantages | Limitations |
---|---|---|---|---|
Evaporation | Material is heated to vaporize and condense on a substrate. | Optical coatings, semiconductor devices, decorative coatings. | High deposition rates, good purity, simple equipment. | Limited to lower melting points, uneven coatings on complex geometries. |
Sputtering | Target material is bombarded with ions to knock off atoms for deposition. | Semiconductor industry, thin-film solar cells, hard coatings for tools. | Wide material range, good adhesion, uniform coatings. | Lower deposition rates, complex and costly process. |
Ion Plating | Combines evaporation and sputtering with ionized gas for enhanced deposition. | Wear-resistant coatings, decorative finishes, aerospace industry. | Highly adherent, dense coatings, suitable for complex geometries. | Complex equipment, slower process compared to other methods. |
Need help selecting the right PVD method for your application? Contact our experts today!